Understanding Sand Casting Tolerances Key Factors for Quality and Precision
Sand casting is a widely used manufacturing process that involves creating metal parts by pouring molten metal into a sand mold. The precision and quality of the final product are largely influenced by the tolerances maintained throughout the casting process. Tolerances define the permissible limits of variation in physical dimensions, ensuring that components meet design specifications and function correctly. This article explores the factors influencing sand casting tolerances and their significance in the manufacturing industry.
Importance of Tolerances in Sand Casting
Tolerances are crucial in sand casting as they directly affect the performance, assembly, and longevity of the final product. Poorly managed tolerances can result in parts that do not fit together correctly, leading to increased assembly times, potential product failures, and wasted materials. In industries like automotive, aerospace, and heavy machinery, where safety and precision are paramount, adhering to strict tolerances is essential.
Factors Affecting Tolerances
1. Mold Design The design of the mold plays a significant role in determining tolerances. Factors such as mold thickness, shape, and complexity can introduce variations. A well-designed mold minimizes the potential for defects, enabling tighter tolerances.
2. Material Selection The choice of metal influences how it behaves during cooling and solidification. Different metals have distinct shrinkage rates, which affect the final dimensions of the casting. For instance, aluminum alloys usually exhibit a higher shrinkage compared to cast iron.
3. Casting Process Parameters Variables such as pouring temperature, cooling rate, and the time the molten metal spends in the mold all impact the final dimensions and surface finish of the casting. Consistency in these parameters is vital for achieving desired tolerances.
sand casting tolerances
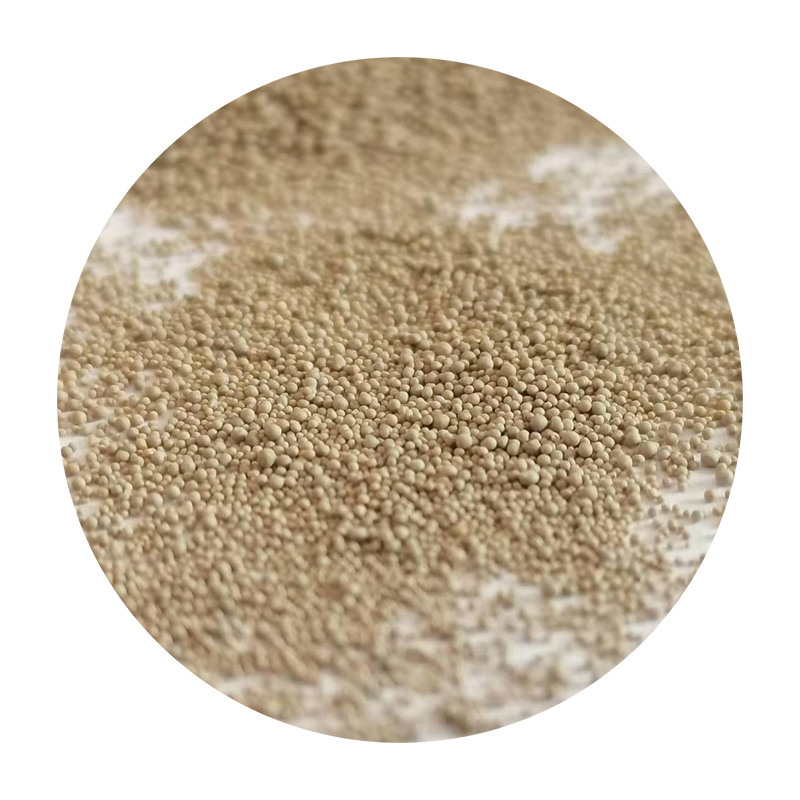
4. Post-Casting Processes After casting, parts often undergo machining or finishing operations to achieve required specifications. Machining can correct minor dimensional errors, helping to meet tighter tolerances. However, relying on post-processing can increase production time and costs.
5. Quality Control Measures Implementing rigorous quality control throughout the sand casting process ensures that tolerances are met. Techniques such as statistical process control, dimensional inspections, and non-destructive testing are employed to monitor and maintain quality standards.
Typical Tolerances in Sand Casting
Tolerances in sand casting can vary significantly based on the size and complexity of the part being produced. Generally, the following ranges are common
- General Tolerances For sand castings, tolerances of ±0.030 inches are typical for small parts, while larger castings may have tolerances of ±0.125 inches. - Complex Geometry Parts with more complex geometries may require tighter tolerances, often around ±0.015 inches. - Critical Functional Dimensions For critical areas where precision is vital, tolerances may be specified as tight as ±0.005 inches.
Conclusion
In conclusion, maintaining proper sand casting tolerances is integral to producing high-quality metal parts that meet industry standards. As sand casting continues to be a vital manufacturing method, understanding the factors affecting tolerances and implementing effective quality control measures will ensure that companies deliver reliable and precise products to their customers. As technology advances, the capabilities to achieve tighter tolerances will continue to improve, leading to advancements in various applications across numerous industries.
Post time:Aug . 09, 2024 06:10
Next:Exploring the Techniques and Benefits of Iron Sand Casting in Modern Metalworking Applications