The Art and Science of Iron Sand Casting
Iron sand casting is an age-old manufacturing technique that has evolved over centuries to become a crucial process in various industries, including automotive, aerospace, and construction. This versatile casting method utilizes iron-rich sand to produce complex metal parts, showcasing both the artistry of craftsmanship and the precision of modern engineering.
Iron sand, primarily composed of magnetite (Fe3O4), is abundant in coastal regions and riverbanks, making it a readily available resource. The casting process begins with the creation of a mold. The sand is mixed with a bonding agent, typically clay, and water to enhance its cohesiveness. This mixture is then packed tightly around a pattern of the desired part, which can be made of wood, metal, or other materials. Once the mold is formed, it is carefully removed from the pattern, and the pattern is extracted, leaving a cavity in the shape of the desired part.
A significant advantage of iron sand casting is its ability to create intricate shapes with excellent dimensional accuracy. The nature of the mold allows for fine details to be captured, making it ideal for producing complex geometries that are difficult to achieve with other methods. Additionally, this process can handle large components, which is essential in industries such as construction where massive structural elements are often required.
After the mold is prepared, molten cast iron is poured into the cavity. The high heat of the molten iron causes the sand particles to partially fuse, forming a strong mold that can withstand the casting process. Once the iron has cooled and solidified, the mold is broken apart to reveal the cast part. This final product often requires minimal machining, resulting in reduced production time and costs, making iron sand casting an efficient manufacturing solution.
iron sand casting
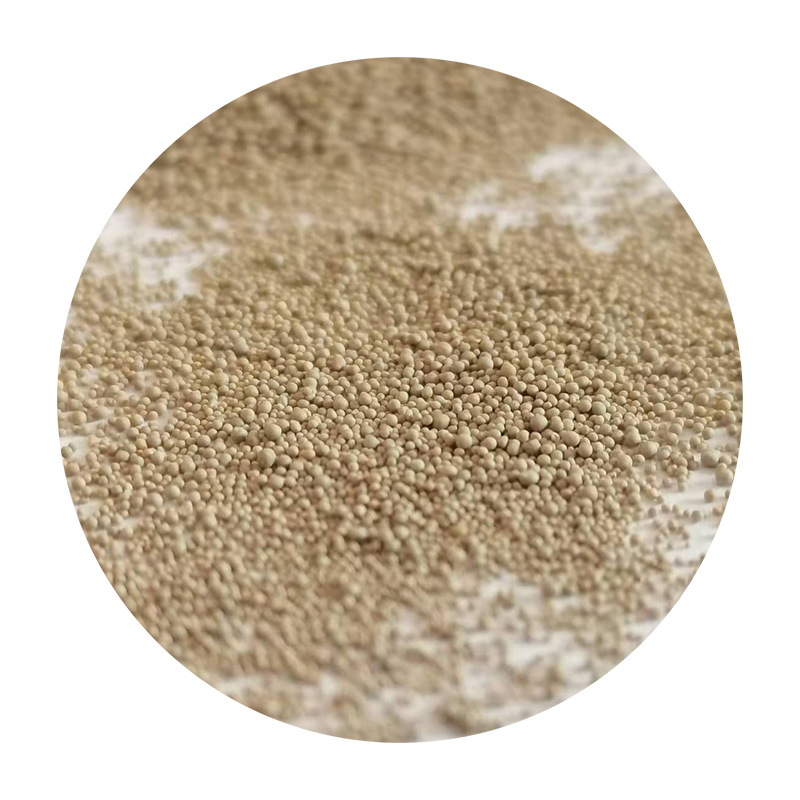
Another key benefit of iron sand casting is its environmental sustainability
. The process generates less waste compared to other manufacturing methods and utilizes natural materials readily available in the environment. Recycling of sand used in casting is also common practice, as the sand can be reclaimed and reused in subsequent casting processes, thus minimizing environmental impact.However, while there are numerous advantages to iron sand casting, it is not without its challenges. One significant concern is the potential for defects, such as air pockets and inclusions, which can occur during the pouring process. These defects can compromise the integrity of the final product, leading to failures in applications where reliability is critical. Therefore, quality control and rigorous testing of cast components are vital to ensure they meet industry standards.
In addition, advancements in technology have significantly improved the iron sand casting process. The introduction of computer-aided design (CAD) and simulation software allows engineers to design more complex molds and predict potential defects before production. Automated systems have also enhanced efficiency and precision, leading to a higher quality of cast items.
In conclusion, iron sand casting stands as a testament to the harmonious blend of tradition and innovation. This method not only celebrates the rich history of metalworking but also embraces modern advances that enhance its efficiency and sustainability. As industries across the globe continue to seek innovative solutions, the art and science of iron sand casting will undoubtedly remain a vital component of manufacturing for years to come. Through its ability to produce high-quality, intricate designs while minimizing waste, iron sand casting embodies the spirit of industrial evolution.
Post time:Aug . 09, 2024 05:50
Next:Innovative Applications and Techniques in 3D Printing Using Sand for Modern Manufacturing Solutions