The Sand Casting Process An Overview
Sand casting, also known as sand mold casting, is one of the oldest and most widely used metal casting processes. It involves creating a mold from a mixture of sand, clay, and water, which is then used to pour molten metal to form a desired shape. This versatile process is employed in various industries, including automotive, aerospace, and art, due to its cost-effectiveness and ability to produce complex shapes.
The Components of Sand Casting
The primary materials used in sand casting include sand, a bonding agent (commonly clay), and water. The sand provides a granular texture that is essential for forming molds, while the clay acts as a binder that helps the sand grains stick together. The mixture is typically moistened with water to enhance its cohesiveness. A variety of sands can be used, with silica sand being the most common due to its excellent thermal properties and availability.
The Sand Casting Process
The sand casting process can be broken down into several key steps
1. Pattern Creation A pattern, typically made of metal, plastic, or wood, is crafted to represent the final object. The pattern is slightly larger than the intended final product to account for metal shrinkage that occurs during cooling.
2. Mold Making The pattern is placed in a mold box, and sand is packed around it to form the mold. Once the sand is compacted, the pattern is removed, leaving a negative impression in the sand. This impression serves as the shape of the mold.
3. Core Making (if needed) For hollow sections of the product, cores made of sand or metal are created to be placed within the mold. This allows the molten metal to fill in the cavity and form the desired internal features.
sand casting process
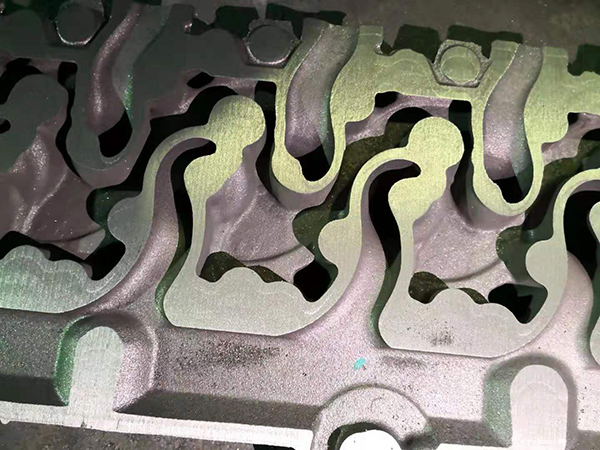
4. Pouring After the mold and cores are prepared, it is ready for pouring. The mold is heated and then molten metal is poured into it. The metal flows into the cavity, filling it completely, and is allowed to cool and solidify.
5. Cleaning Once the metal has cooled sufficiently, the mold is broken away to reveal the cast object. The casting typically requires cleaning to remove any excess sand, gating systems, or rough edges.
6. Finishing After cleaning, the casting may undergo further finishing processes such as machining, polishing, or coating to achieve the desired surface quality and dimensions.
Advantages of Sand Casting
One of the main advantages of sand casting is its ability to create complex shapes that would be difficult or impossible to achieve with other methods. Additionally, it is suitable for a variety of metals, including aluminum, iron, and bronze. The process is relatively low-cost, especially for small production runs, as the materials are readily available and the setup time is minimal.
Moreover, sand casting is highly flexible, allowing for modifications to patterns and molds without significant expense. This adaptability makes it an excellent choice for prototypes and custom parts.
Challenges and Considerations
While sand casting has many benefits, it also comes with challenges. The quality of the cast product can be affected by the properties of the sand mixture, mold preparation, and pouring techniques. Defects such as sand inclusion, porosity, and shrinkage can occur if the process is not carefully controlled.
In conclusion, sand casting is a time-honored manufacturing method that continues to be an essential part of many industries today. Its cost-effectiveness, ability to create intricate shapes, and versatility in materials make it a popular choice for both small and large-scale production. Whether producing automotive components or intricate artistic sculptures, sand casting remains a relevant and valuable technique in the world of manufacturing.
Post time:Aug . 13, 2024 11:20
Next:Exploring the Applications and Benefits of Ceramsite in Foundry Sand Manufacturing