Ceramsite Foundry Sand A Revolutionary Material in Metal Casting
In the metal casting industry, the choice of sand plays a vital role in determining the quality and characteristics of the final product. Traditionally, silica sand has been the go-to material; however, a modern approach has seen the emergence of ceramsite foundry sand as a revolutionary alternative. This innovative material is redefining casting processes, enhancing product quality, and becoming increasingly popular for a variety of applications.
What is Ceramsite Foundry Sand?
Ceramsite foundry sand, also known as ceramic sand, is produced by the thermal treatment of raw materials such as kaolin clay. The process involves heating the clay at high temperatures, resulting in a lightweight, spherical particle with excellent flow characteristics. This unique structure grants ceramsite sand several advantages over traditional sand types.
Advantages of Ceramsite Foundry Sand
1. Superior Thermal Properties Ceramsite sand exhibits remarkable thermal stability, which allows it to withstand higher temperatures without deforming. This property is crucial in metal casting, as it reduces the likelihood of defects caused by sudden temperature changes during the pouring and cooling phases.
2. Enhanced Mold Strength The spherical shape and high density of ceramsite sand provide better packing density compared to conventional sands. This results in improved mold strength and reduces the likelihood of mold collapse during the pouring process. Consequently, manufacturers experience fewer defects and higher yields.
ceramsite foundry sand
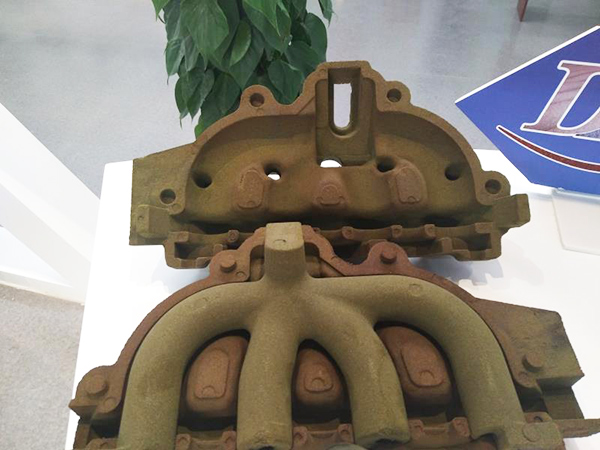
3. Lower Expansion Rate While traditional sand can expand and lead to surface finishes that require additional finishing processes, ceramsite sand features lower thermal expansion rates. This characteristic ensures that the mold maintains its shape during casting, allowing for finer surface finishes and reducing the need for post-casting modifications.
4. Reduced Environmental Impact The use of ceramsite sand contributes positively to environmental sustainability. Unlike silica sand, which is subject to depletion, ceramsite can be manufactured from abundant raw materials. Moreover, it is recyclable, leading to decreased consumption of new materials and minimizing waste.
5. Cost Efficiency Although the initial cost of ceramsite foundry sand may be higher than traditional sands, its reusability, enhanced durability, and improved cast quality can lead to significant cost savings in the long run. Additionally, reduced scrap rates and fewer defective castings translate into better profitability for foundries.
Applications of Ceramsite Foundry Sand
Ceramsite foundry sand is versatile and can be used across various industries, including automotive, aerospace, and machinery. Its ability to produce precise molds makes it ideal for casting complex geometries and high-precision components, which are often required in these sectors. Furthermore, as industries increasingly prioritize sustainability, the adoption of ceramsite sand continues to rise as part of responsible manufacturing practices.
Conclusion
Ceramsite foundry sand stands out as a superior alternative to traditional molding materials in metal casting. With its exceptional thermal properties, improved mold strength, lower expansion rates, environmentally friendly profile, and cost-effectiveness, it is not surprising that ceramsite sand is gaining traction in the industry. As metal casting technologies continue to evolve, embracing innovative materials like ceramsite sand will be imperative for manufacturers aiming to enhance efficiency and product quality while adhering to sustainable practices. The future of foundry operations looks promising with ceramsite sand leading the way in advanced casting solutions.
Post time:Aug . 13, 2024 11:12
Next:Exploring the Innovative Intersection of 3D Printing Technology and Sand Casting Techniques in Manufacturing