Understanding the Sand Casting Process
Sand casting, a versatile and widely used manufacturing process, plays a crucial role in producing metal parts and components. It operates by creating a mold from sand and then pouring molten metal into that mold to create intricate shapes and designs. This method has been utilized for thousands of years, but it remains an essential fabrication technique in various industries today, including automotive, aerospace, and art.
The Basics of Sand Casting
At the core of the sand casting process is the creation of a mold, typically made from a mixture of sand, clay, and water. This mixture is known for its ability to hold shape while also providing permeability for gases released during the metal pouring process. The first step in sand casting involves creating a pattern, which is a replica of the desired final product. This pattern is generally made of metal, wood, or plastic and is slightly larger than the finished product to account for thermal expansion and contraction during cooling.
Once the pattern is ready, the next step involves creating the mold itself. The sand mixture is packed around the pattern to form a mold shell. This is done in two halves, known as the cope (top half) and the drag (bottom half). After packing, the two halves are separated, and the pattern is removed, leaving an impression of the final shape. To ensure the mold facilitates the casting process, features such as gating and riser systems are added. Gating allows the molten metal to flow into the mold, while risers act as reservoirs to compensate for shrinkage as the metal cools.
Pouring the Metal
With the mold in place, the next step is pouring the molten metal. This requires heating the desired metal to its melting point and carefully funneling it into the mold through the gating system. Common metals used in sand casting include aluminum, iron, and bronze. The choice of metal depends on the desired properties of the final product.
The cooling period is crucial, as the time taken for the metal to solidify affects the final piece's quality. It is essential to monitor the cooling process since rapid cooling can lead to defects such as cracking or warping. Once the metal has cooled and solidified, the mold is broken apart to reveal the cast part.
what is sand casting process
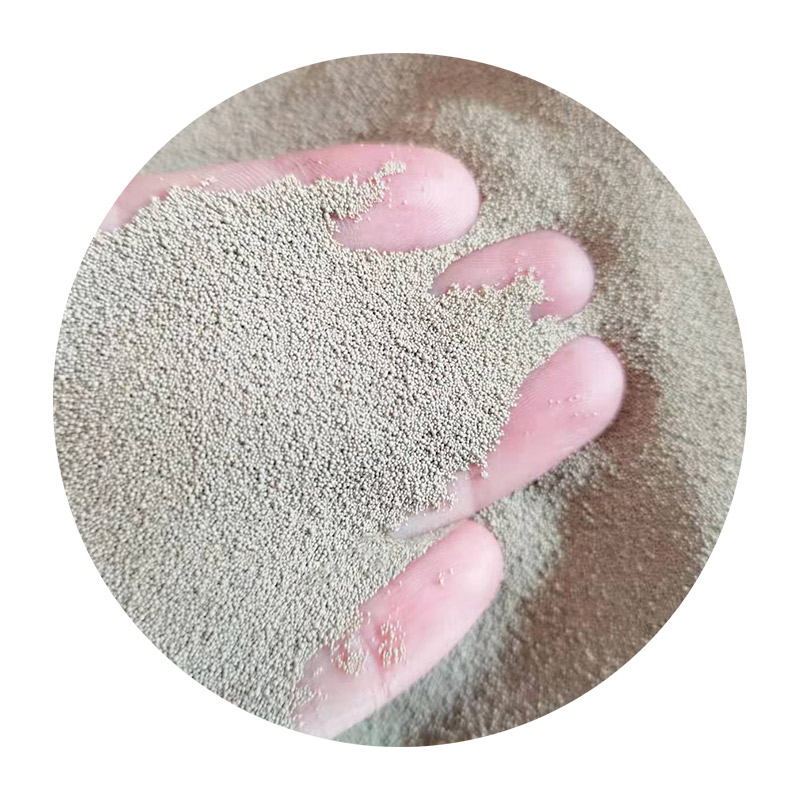
Finishing Touches
After the casting is removed from the mold, several finishing processes may be necessary. These can include trimming excess material, surface smoothing, and applying coatings for protection or aesthetic purposes. Depending on the complexity of the cast part, machining may also be required to achieve precise dimensions and specifications.
Advantages of Sand Casting
One of the primary advantages of sand casting is its capability to produce complex shapes that would be challenging to achieve with other manufacturing processes. The materials used are generally inexpensive, and the process can accommodate large and heavy parts. Furthermore, sand molds can be reused, making the process cost-effective for high-volume production runs.
Another significant benefit is the flexibility of the sand casting process regarding material choice. Manufacturers can select a variety of metals based on the mechanical properties required for specific applications. As a result, sand casting continues to be an indispensable method in various sectors that demand durability and reliability in their components.
Conclusion
In conclusion, sand casting is a fundamental process in the manufacturing landscape. Its ability to produce intricate designs from a wide array of metals while remaining economically feasible makes it a preferred choice for many industries. As technology advances, the sand casting process is likely to evolve further, incorporating innovative techniques and materials to meet the demands of modern manufacturing. Understanding this process not only highlights its significance but also opens the doors to exploring new possibilities in manufacturing technology.
Post time:Aug . 14, 2024 05:21
Next:Understanding the Sand Casting Process and Its Importance in Metal Fabrication Techniques