Understanding the Sand Casting Process
Sand casting, also known as sand mold casting, is one of the most widely used metal casting processes. It involves creating a mold from suitably shaped sand particles to produce metal parts. This method is prevalent in various industries due to its cost-effectiveness, flexibility, and capability to produce complex geometries.
The Basics of Sand Casting
The sand casting process begins with the creation of a mold. The key ingredient in this process is sand, a naturally abundant material that is mixed with a binding agent, usually clay or resin, to hold the sand particles together. The mixture is then compacted around a pattern, which represents the final shape of the object to be cast. Patterns can be made of metal, wood, or plastic and are often double-sided to facilitate easier extraction from the mold.
Once the mold is formed, it is then prepared for the pouring of molten metal. The pattern is removed, and the resulting cavity is filled with the molten metal. The metal is poured in at high temperatures, allowing it to flow uniformly into the mold cavity. After the metal cools and solidifies, the mold is broken away to reveal the final casting.
Advantages of Sand Casting
One of the main advantages of sand casting is its versatility. It can accommodate a wide range of metals, including aluminum, bronze, iron, and steel. The process allows for the creation of intricate designs and large castings, which can weigh anywhere from a few grams to several tons. Additionally, sand molds can be reused multiple times, making the process environmentally friendly and cost-effective.
Moreover, sand casting is suitable for both short runs and high-volume production
. This adaptability makes it a preferred choice among manufacturers, particularly in industries like automotive, aerospace, and machinery.what is sand casting process
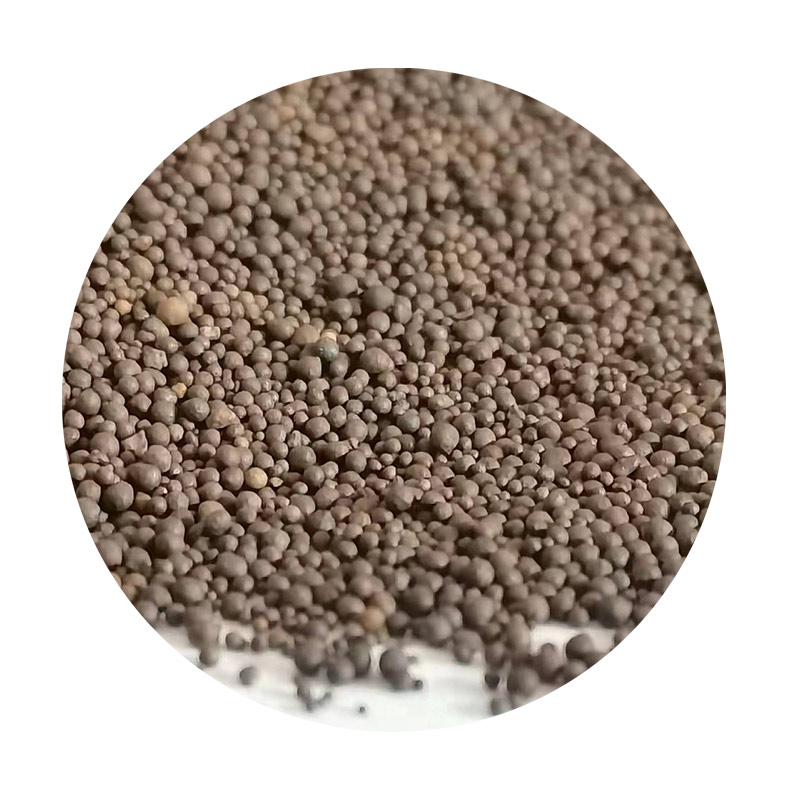
Limitations of Sand Casting
While sand casting has many benefits, it also comes with some limitations. The surface finish of sand-cast components is generally rough compared to parts produced with other casting methods. This means that additional machining may be necessary to achieve the desired surface finish and dimensional accuracy.
Another downside is the time required for mold preparation. For complex designs, the pattern-making process can be lengthy, and the setup can require significant effort. Additionally, production rates may not be as high as other casting methods, making sand casting less suitable for extremely high-volume operations.
Innovations in Sand Casting
Advancements in technology have led to improvements in the sand casting process. Modern techniques, such as the use of computer-aided design (CAD) software for pattern design and the integration of automated molding equipment, have increased efficiency and accuracy. 3D printing technology is also beginning to play a role in creating more intricate and precise sand molds.
These innovations help address some of the traditional limitations of sand casting, paving the way for its continued relevance in contemporary manufacturing.
Conclusion
In summary, sand casting is a vital manufacturing process that has stood the test of time due to its versatility, cost-effectiveness, and ability to create complex shapes. While it does face some challenges, ongoing technological advancements are enhancing the process's efficiency and accuracy. Whether used in small workshops or large industrial settings, sand casting remains a cornerstone of metal fabrication, demonstrating its enduring importance in the manufacturing landscape.
Post time:Aug . 14, 2024 05:09
Next:Exploring the Benefits and Techniques of Sanding with Epoxy Resin in DIY Projects