The Sand Casting Foundry Process A Comprehensive Overview
Sand casting is one of the oldest and most versatile metal casting processes still in widespread use today. It involves creating a mold from sand to cast liquid metal, and it is highly favored due to its ability to produce complex shapes and large parts. In this article, we will explore the sand casting foundry process, its components, advantages, and applications.
The Sand Casting Process
The sand casting process begins with the creation of a pattern, usually made from metal or wood, which represents the object to be cast. Patterns are designed with consideration for shrinkage, draft, and other factors to ensure that the final product is accurate. After the pattern is ready, it is used to create a mold made of a mixture of sand, clay, and water, known as molding sand.
The sand used in foundries is typically a silica-based sand that is mixed with a binding agent, usually clay, and water. This mixture allows the mold to hold its shape while also being permeable enough to let gases escape when the molten metal is poured in.
Once the mold is prepared, the pattern is placed into a mold box, and sand is compacted around it. After the sand has been compacted and set, the pattern is removed, leaving a cavity in the shape of the object. The mold can be either a single part (called a one-piece mold) or a multi-part mold that allows for more complex designs.
Pouring the Metal
With the mold ready, the next step is to prepare the molten metal, which is typically heated in a furnace until it reaches a liquid state. Commonly used metals include aluminum, cast iron, and bronze, each chosen for its unique properties. The molten metal is then poured into the mold cavity.
A key aspect during this stage is managing the pouring temperature and speed, which can influence the final properties of the casting, such as porosity and integrity
. The metal must be poured carefully to avoid creating air pockets or introducing impurities.sand casting foundry process
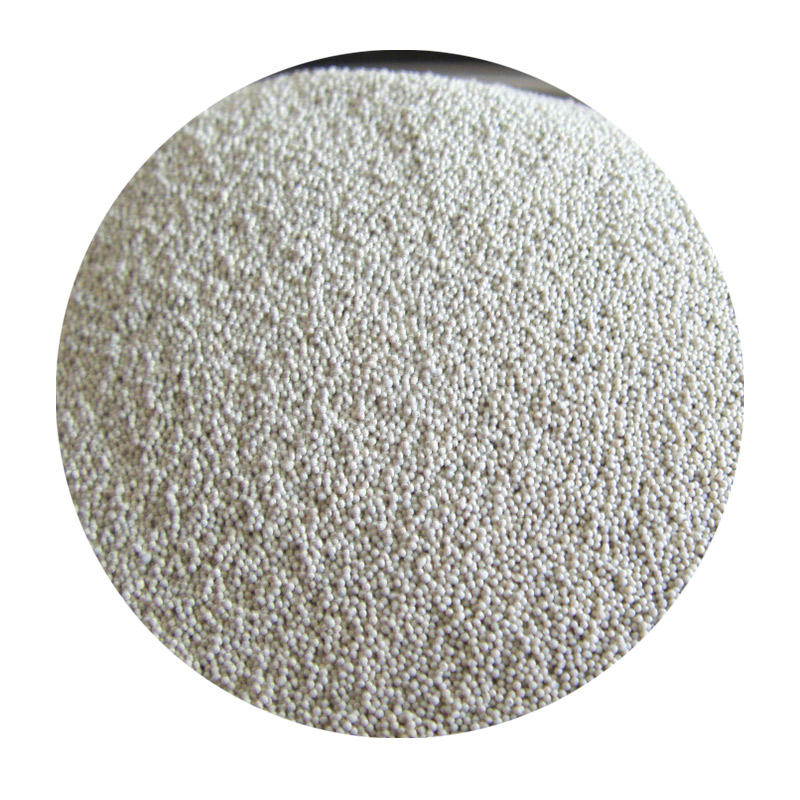
Cooling and Finishing
After the metal has been poured into the mold, it is allowed to cool and solidify. The cooling time varies depending on the size and material of the casting. Once cooled, the mold is broken apart to retrieve the casting. This step often involves shaking out the sand, which can be reused for future molds.
Following the extraction, the casting often requires finishing processes. These might include machining, grinding, or sandblasting to achieve the desired dimensions and surface quality. Additional processes like heat treatment or surface coating may also be applied to enhance mechanical properties or corrosion resistance.
Advantages of Sand Casting
Sand casting is widely recognized for its numerous advantages. One of the most significant benefits is its flexibility in producing a range of sizes, from small to very large components. It is also relatively inexpensive as it uses readily available materials. Furthermore, the process allows for intricate details and complex geometries, making it suitable for various industries, including automotive, aerospace, and art.
Applications
The applications of sand casting are diverse. It is commonly used to produce engine blocks, turbine housings, and various components for industrial machinery. Its ability to accommodate both ferrous and non-ferrous metals makes it invaluable in manufacturing.
Conclusion
In conclusion, the sand casting foundry process is a well-established technique that combines simplicity with versatility. Understanding its intricacies not only highlights its importance in the manufacturing industry but also showcases the craftsmanship involved in transforming raw materials into functional products. With ongoing innovations, sand casting continues to evolve, maintaining its relevance in modern production environments.
Post time:Jul . 26, 2024 07:07
Next:Understanding the Properties and Applications of Sand Casting Alloys in Modern Manufacturing Techniques