Sand Casting Alloys An Overview
Sand casting is one of the oldest and most versatile metal casting processes used in manufacturing today. This technique involves creating a mold from sand, into which molten metal is poured to form a desired shape. The choice of alloy used in sand casting is crucial, as it directly influences the properties of the final product. In this article, we delve into various alloys suitable for sand casting, their characteristics, and their applications.
Common Alloys Used in Sand Casting
1. Aluminum Alloys Aluminum is one of the most frequently used metals in sand casting due to its lightweight nature, excellent corrosion resistance, and good castability. Common aluminum alloys for sand casting include 356 and 319. The 356 alloy is popular for its high strength-to-weight ratio and is often used in aerospace and automotive applications. On the other hand, the 319 alloy offers better fluidity and is often used for producing engine components.
2. Iron Alloys Cast iron is a traditional and widely used material in sand casting. Its excellent castability, wear resistance, and machinability make it suitable for a wide range of applications. Gray cast iron is the most common type, known for its excellent vibration dampening properties, making it ideal for engine blocks, pipes, and machinery parts. Ductile iron, also known as nodular iron, provides higher tensile strength than gray iron and is used in critical engineering components.
3. Copper Alloys Copper-based alloys, such as brass and bronze, are also popular choices for sand casting. Brass, an alloy of copper and zinc, exhibits good corrosion resistance and is utilized in applications such as plumbing fixtures, fittings, and decorative items. Bronze, an alloy of copper and tin, offers superior wear resistance and toughness, making it suitable for bearings, marine components, and sculptures.
sand casting alloys
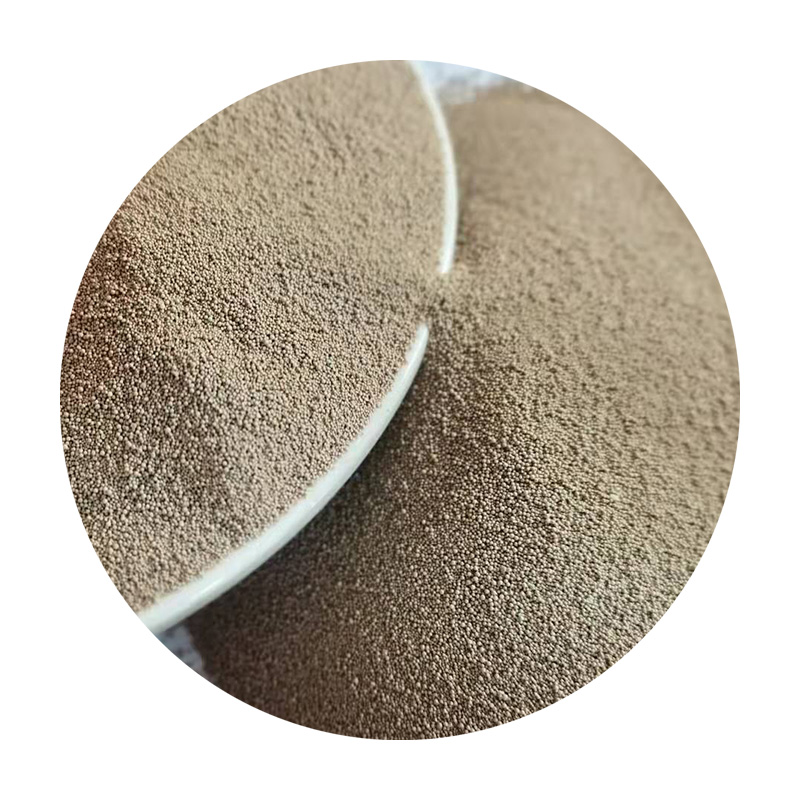
4. Magnesium Alloys Magnesium alloys are increasingly popular in sand casting due to their low density and high strength. They are often used in aerospace and automotive applications to reduce weight while maintaining strength. AZ91D is a well-known magnesium alloy that offers good casting properties and can be used for various complex shapes.
Factors Influencing Alloy Selection
When selecting an alloy for sand casting, several factors must be considered. These include the intended application, mechanical property requirements, corrosion resistance, and cost. For instance, if the final product will be exposed to harsh environmental conditions, an alloy with superior corrosion resistance, such as aluminum or certain copper alloys, would be preferable. Conversely, if the application requires high strength and durability, iron or magnesium alloys might be more suitable.
Conclusion
Sand casting remains a crucial method in the metalworking industry, and the choice of alloy is fundamental to the success of this process. With a diverse range of materials available, manufacturers can tailor their selections based on the desired properties of the final product. Whether it’s the lightweight and corrosion-resistant characteristics of aluminum, the strength of iron, or the durability of copper alloys, each option presents unique advantages. As technology advances, the development of new alloys and casting techniques will continue to enhance the capabilities and applications of sand casting, ensuring its relevance in modern manufacturing. The versatility and adaptability of sand casting alloys will undoubtedly play a significant role in the future of the industry.
Post time:Jul . 26, 2024 07:07
Next:Exploring the Benefits and Applications of Resin Sand in Modern Foundry Processes