Facing Sand in Foundry A Critical Component of Metal Casting
In the realm of metal casting, the intricacies of the foundry process are pivotal to achieving high-quality outcomes. Among various elements that contribute to the success of casting, facing sand plays a crucial role. Understanding what facing sand is and its significance in the foundry industry can vastly improve casting results and enhance the performance of metal components.
Facing Sand in Foundry A Critical Component of Metal Casting
The composition of facing sand is crucial; it traditionally includes high-quality silica sand combined with a bonding agent like clay or resin. These materials enable the sand to withstand the heat and pressure exerted by the molten metal. A well-formulated facing sand not only enhances the surface finish but also minimizes the occurrence of defects such as sand burn-on, which can mar the appearance and integrity of the final product.
facing sand in foundry
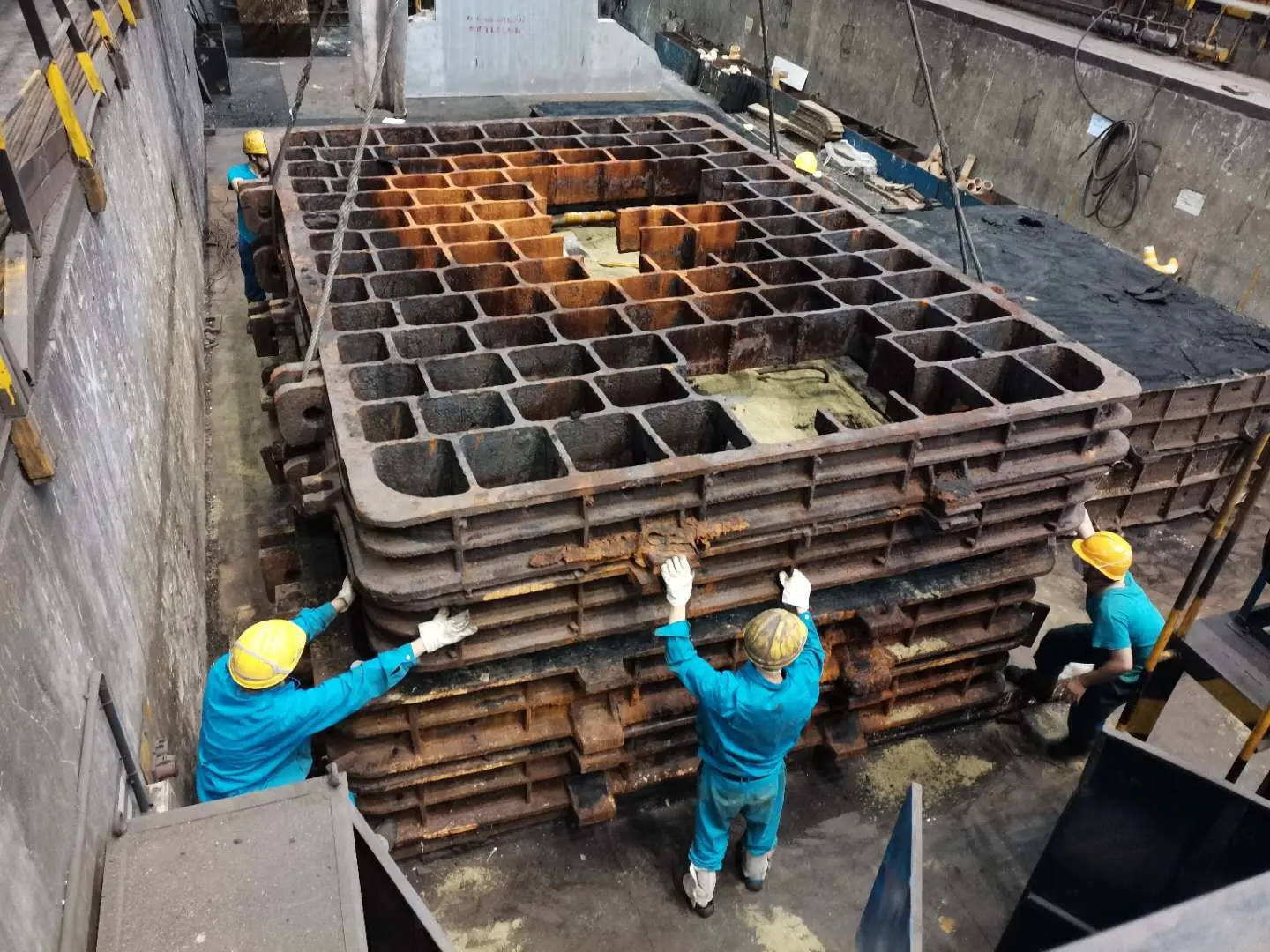
Moreover, the choice of facing sand impacts the thermal properties of the mold. When molten metal is poured, intense heat is transferred to the facing sand layer. A good facing sand should have excellent thermal conductivity to facilitate better heat transfer, which is particularly crucial in processes such as sand casting. This ensures that the outer layer of the mold solidifies appropriately, allowing for the creation of precise and accurate metal parts.
In addition to these thermal and mechanical properties, the environmental aspects of facing sand usage are frequently discussed, especially in the context of sustainable manufacturing practices. With the pressing need for eco-friendly solutions, foundries are increasingly exploring alternative binders and sand materials that reduce the environmental footprint associated with sand casting. The introduction of synthetic sands and recycling efforts is making strides in this area, providing foundries with options that do not compromise performance while being kinder to the environment.
The application of facing sand goes beyond merely serving as the interface between the mold and the molten metal. It is integral to the pattern-making process in casting. Foundries need to meticulously design the sand mold to ensure that the faced layer adheres well and does not crumble under strain. Proper handling and conditioning of the facing sand are also paramount, as moisture content and particle size can significantly influence the final cast’s quality.
In conclusion, facing sand is a fundamental element in metal casting within the foundry industry. Its role in defining the surface finish, protecting underlying materials from thermal shock, and contributing to the overall structural integrity of cast components cannot be overstated. As the foundry industry moves toward sustainability and innovation, the evolution of facing sand—both in material composition and application—will continue to play a significant part in enhancing the efficiency and quality of metal casting processes. Understanding and optimizing the use of facing sand can yield substantial benefits, ultimately culminating in superior casting results that meet the growing demands of various industries.
Post time:Aug . 13, 2024 06:02
Next:Exploring the Benefits of Lost Foam Casting in Modern Manufacturing Processes and Applications