Advantages of Lost Foam Casting
Lost foam casting (LFC) is an advanced metal casting process that has gained popularity in various industries due to its unique advantages. This method, which relies on the use of a foam pattern that evaporates when molten metal is poured into the mold, offers a range of benefits that make it an attractive option for manufacturers. Below, we explore the key advantages of lost foam casting.
1. Dimensional Accuracy and Surface Finish
One of the most notable advantages of lost foam casting is its ability to produce highly accurate and intricately detailed parts. The foam patterns used in this process are manufactured using an expanded polystyrene material, which allows for precise replication of complex geometries. As the foam evaporates, it leaves a negative impression in the sand mold, allowing for an excellent surface finish and tight tolerances in the final product. This precision reduces the need for secondary machining operations, thereby saving time and costs.
2. Design Flexibility
Lost foam casting offers designers a remarkable degree of freedom when it comes to creating complex shapes. Traditional casting methods often require the use of multiple cores and cores can lead to complications during assembly and finishing. In contrast, lost foam casting simplifies the production process by enabling the creation of intricate components in a single pour. This flexibility is particularly beneficial when producing components for industries such as automotive, aerospace, and art where design innovation is crucial.
3. Lower Production Costs
Another significant benefit of lost foam casting is its cost-effectiveness, especially for low to medium production runs. The elimination of machining processes due to the high accuracy of the cast parts means that manufacturers can reduce labor and tooling costs significantly. Furthermore, the use of foam patterns reduces the need for expensive metal patterns that are often required in traditional casting methods. This cost-saving aspect makes LFC an attractive option for both small and large businesses looking to optimize their production processes.
advantages of lost foam casting
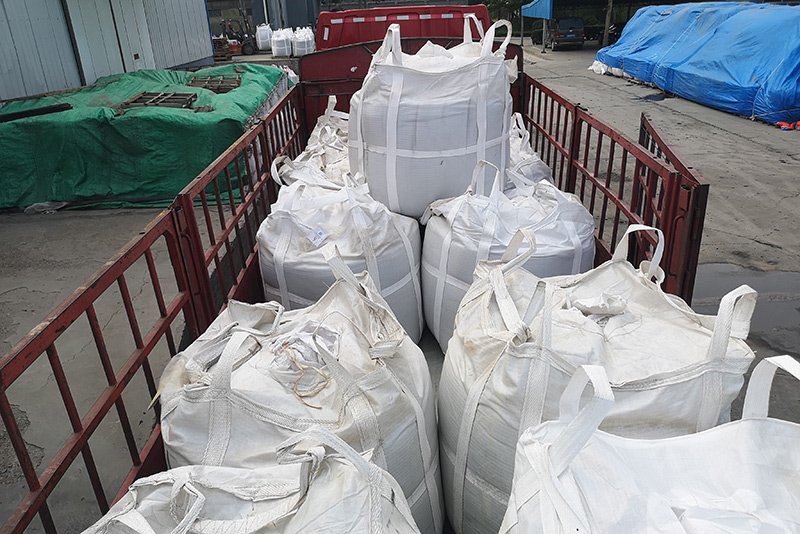
4. Material Efficiency
Lost foam casting is also advantageous in terms of material usage. The method allows for minimal waste generation as the foam pattern is completely consumed during the process. Moreover, LFC can accommodate a variety of metals, including iron, aluminum, and steel, making it an adaptable method for different applications. This versatility in material selection helps manufacturers optimize resource utilization while still achieving high-quality results.
5. Reduced Environmental Impact
In the context of increasing environmental awareness, LFC stands out as a more environmentally-friendly casting process. The foam material used in lost foam casting is recyclable, and the process itself generates fewer emissions compared to traditional casting methods. By reducing the need for additional machining and the consumption of raw materials, LFC contributes to a more sustainable manufacturing approach.
6. Improved Turnaround Time
Lastly, lost foam casting can significantly improve production turnaround times. The efficient nature of this casting process allows for quicker production cycles, enabling manufacturers to meet tight deadlines and respond rapidly to changing market demands. This agility is essential in industries that require fast-paced production without sacrificing quality.
Conclusion
In summary, lost foam casting is a highly advantageous method of producing metal components. Its ability to deliver dimensional accuracy, design flexibility, cost-effectiveness, material efficiency, reduced environmental impact, and improved turnaround times makes it an appealing choice for manufacturers across diverse industries. As technology continues to evolve, lost foam casting is poised to play an increasingly important role in the future of manufacturing.
Post time:Aug . 13, 2024 05:32
Next:Exploring the Best Sand Casting Manufacturers for Quality and Precision in Metal Fabrication Solutions