The Sand Casting Process An Overview
Sand casting, also known as sand molded casting, is one of the oldest and most widely used metal casting processes. It is characterized by its simplicity and versatility, making it a preferred method for producing complex shapes and large components in various metals, including aluminum, iron, and brass. The process involves several stages, each contributing to the final product's quality and precision.
The Sand Casting Process
The sand casting process begins with the creation of a mold. The first step is to prepare a pattern, which is a replica of the object to be cast. Patterns can be made from various materials, including wood, metal, or plastic, and are crafted slightly larger than the final product to account for shrinkage during cooling.
Once the pattern is ready, it is placed into a sand mixture, typically composed of silica sand, clay, and water. The sand is tightly packed around the pattern to create a mold, which captures the intricate details of the pattern. In many cases, the mold is divided into two halves, called cope and drag, allowing for easy removal of the pattern once the mold is set.
After the sand is properly compacted, the two halves of the mold are carefully separated, and the pattern is removed, leaving a cavity that replicates the shape of the desired part. The mold halves are then reassembled and secured, often using pins or clamps to maintain alignment.
Pouring the Metal
With the mold prepared, the next step is to pour the molten metal into the cavity. The metal is heated to a liquid state and transferred to the pouring basin, where it flows into the mold through channels called gates. The design of the gating system is crucial as it affects both the filling of the mold and the quality of the casting.
As the metal fills the mold, it takes the shape of the cavity. It is essential to control the pouring temperature and speed to minimize defects such as gas porosity or cold shuts. This phase requires significant skill and experience to ensure a successful cast.
describe sand casting process
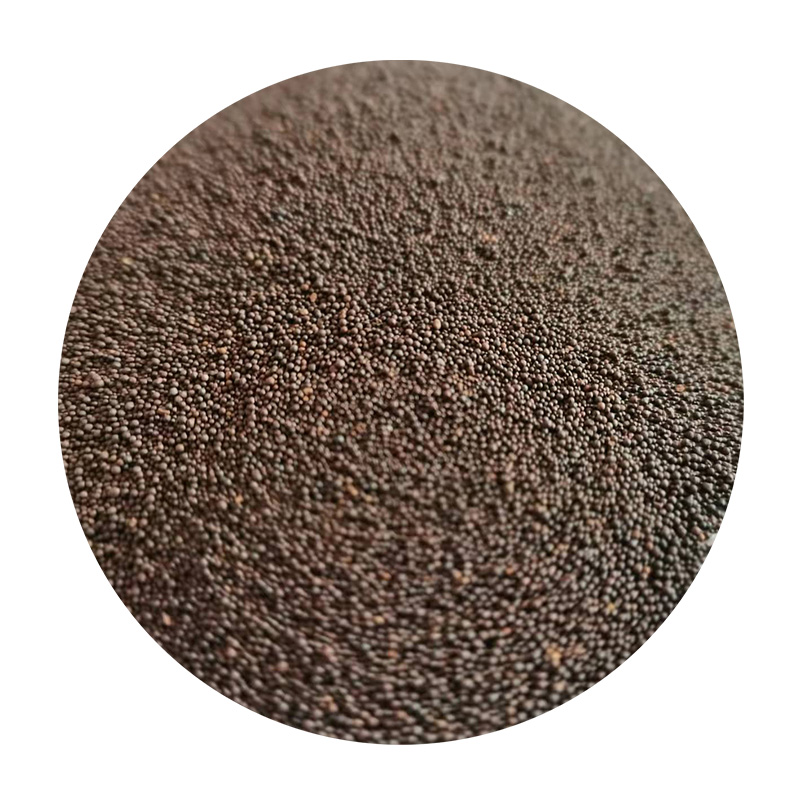
Cooling and Finishing
After the mold is filled, the metal is left to cool and solidify. The cooling time depends on the metal type, thickness of the casting, and ambient conditions. Once cooled, the mold is broken apart to retrieve the casting.
The result is a rough casting that usually requires further finishing processes. This can include machining, sanding, grinding, or polishing to achieve the desired surface finish and dimensional accuracy. Additional processes like heat treatment may be performed to enhance the mechanical properties of the final product.
Advantages and Applications
Sand casting offers several advantages, such as the ability to produce large and intricate parts with ease. It is cost-effective for low to medium production runs and can accommodate various materials. This versatility has made sand casting a popular choice in many industries, including automotive, aerospace, and construction.
Furthermore, the technique allows for the use of multiple types of sand, enabling custom properties to be tailored for specific applications. It also supports recycling of sand, which contributes to its sustainability.
Conclusion
In summary, the sand casting process is a crucial manufacturing technique characterized by its adaptability and efficiency. From the creation of the mold to the final finishing of the cast product, each step plays a vital role in determining the overall quality of the casting. As industries continue to evolve, sand casting remains an indispensable process for producing complex metal parts, highlighting its enduring relevance in modern manufacturing.
Post time:Aug . 19, 2024 11:41
Next:Exploring the Benefits of Coated Sand Casting for Optimal Metal Foundry Results