The Importance of Coated Sand Casting in Modern Manufacturing
Coated sand casting is a widely used manufacturing process that plays a crucial role in producing high-quality metal components for various industries. This method involves the use of sand that is coated with a resin or other binding agents, creating a durable and versatile mold for casting metals. The innovative nature of coated sand casting not only enhances the mechanical properties of the final products but also improves the overall efficiency of the casting process.
One of the primary advantages of coated sand casting is its ability to produce molds with excellent surface finish and dimensional accuracy. The coated sand creates a tighter mold surface, reducing the likelihood of defects such as imperfections or rough edges. This is particularly important in industries where precision is paramount, such as aerospace, automotive, and medical equipment manufacturing. The smooth surface finish achieved through coated sand casting often eliminates the need for extensive post-processing, thereby saving time and reducing production costs.
In addition to surface quality, coated sand casting allows for intricate designs that may be challenging to achieve through traditional sand casting methods. The binding agents used to coat the sand enable it to retain its shape more effectively during the pouring of molten metal. This characteristic allows manufacturers to produce complex geometries and features that enhance the functionality of the final product. As industries continue to demand more sophisticated components, the ability to create detailed designs becomes increasingly beneficial.
The environmental impact of manufacturing processes is a growing concern in today’s world, and coated sand casting is no exception. However, advancements in coating materials have led to the development of more eco-friendly options. Manufacturers are now using water-based resins and recyclable sand, reducing the environmental footprint of the casting process. This shift not only aligns with global sustainability goals but also appeals to consumers and businesses that prioritize eco-conscious practices.
coated sand casting
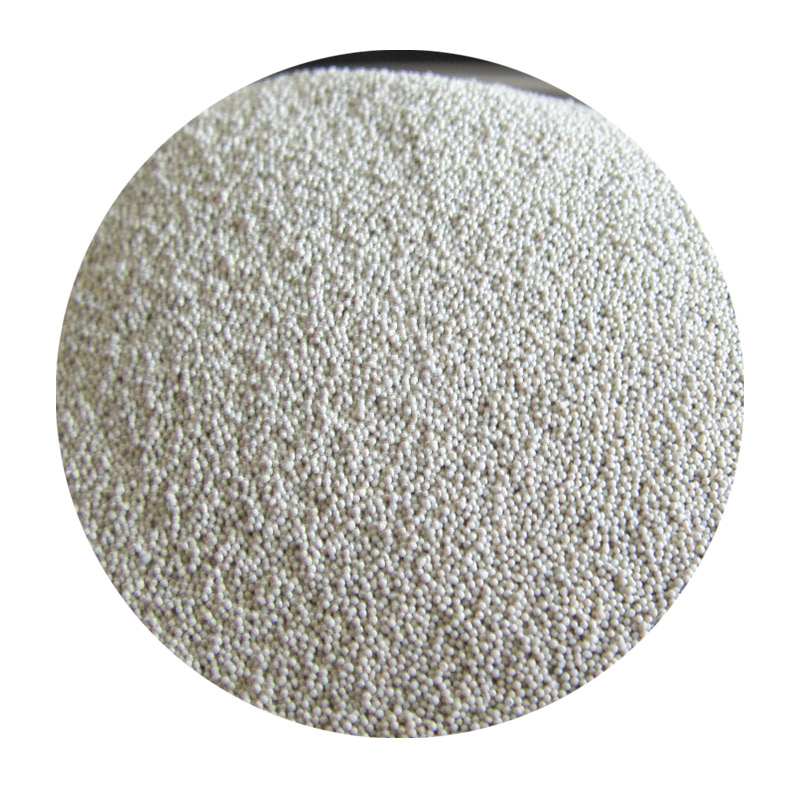
Moreover, the adaptability of coated sand casting makes it suitable for a wide range of materials. Whether dealing with ferrous alloys, non-ferrous metals, or their composites, the method can be tailored to accommodate different alloy compositions. This flexibility allows manufacturers to respond swiftly to changing market demands and material requirements, ultimately leading to a more efficient production cycle.
The turnaround time for producing molds using coated sand casting is also considerably reduced compared to other casting processes. Traditional casting techniques often require extensive waiting periods for curing and hardening. In contrast, the application of coated sand allows for rapid mold production, which is especially advantageous in industries where speed is critical. Companies can shorten their lead times, meet tight deadlines, and maintain a competitive edge in the market.
Despite its many advantages, coated sand casting does pose certain challenges. For instance, the initial setup costs may be higher due to the need for specialized equipment and materials. Additionally, the process requires skilled labor to manage the coating and ensure the quality of the molds. However, with ongoing advancements in technology and training, these hurdles are becoming increasingly manageable.
In conclusion, coated sand casting stands out as a revolutionary method in the field of metal casting. Its ability to deliver superior surface quality, accommodate complex designs, and enhance production efficiency makes it an invaluable resource across various sectors. As the manufacturing landscape continues to evolve, the significance of coated sand casting will only grow, shaping the future of how high-quality metal components are produced.
Post time:Aug . 19, 2024 05:54
Next:High-Performance Ceramic Sanding Discs for Optimal Surface Finishing and Efficiency