The Importance of Foundry Sand in Metal Casting
Foundry sand is a crucial element in the metal casting industry, serving as a key component in the production of metal components. This specialized sand, often made from high-quality silica, plays a vital role in creating molds and cores that shape molten metals into various products used across numerous industries, including automotive, aerospace, and construction. Understanding the significance of foundry sand is essential for appreciating its contributions to metal casting and the broader manufacturing sector.
Composition and Properties
Foundry sand is primarily composed of fine silica particles, which are known for their thermal stability, durability, and ability to withstand high temperatures. These properties are critical, as molds must retain their shape and integrity when exposed to molten metal, which can exceed temperatures of 1,500 degrees Celsius (2,732 degrees Fahrenheit). The sand also exhibits excellent permeability, allowing gases to escape from the mold during the casting process, thus preventing defects such as blisters and inclusions in the final product.
Types of Foundry Sand
There are several types of foundry sands, including natural silica sand, synthetic sand, and reclaimed sand. Natural silica sand is mined and processed to achieve the desired grain size and purity. Synthetic sand, on the other hand, is engineered from recycled materials and designed to provide specific characteristics tailored to particular casting processes.
Reclaimed sand is an essential innovation in the foundry industry, as it plays a significant role in promoting sustainability. After a casting cycle, the sand can be cleaned and reused, reducing the need for new sand extraction and minimizing waste. This not only lowers production costs but also lessens the environmental impact associated with sand mining and disposal.
The Role of Foundry Sand in the Casting Process
making foundry sand
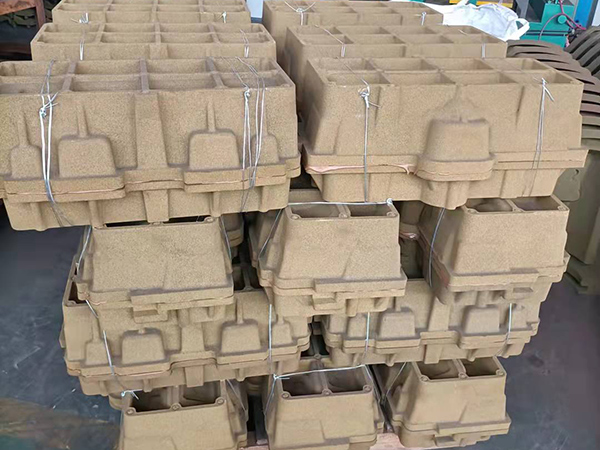
The casting process begins with the preparation of the mold using foundry sand. The sand is mixed with a binding agent, typically a resin, to create a cohesive material that can hold its shape. Once the mold is formed, it is heated to cure the binding agent, resulting in a strong and durable mold capable of withstanding the pressures of molten metal. After the metal is poured and solidifies, the sand mold is broken apart to reveal the final casted piece.
The quality of foundry sand directly impacts the surface finish and dimensional accuracy of the castings. Poor-quality sand can lead to defects in the cast metal, such as rough surfaces, dimensional inaccuracies, or structural weaknesses. Thus, selecting the right type of foundry sand and ensuring its quality is paramount for foundries to produce high-quality components consistently.
Challenges and Innovations
While foundry sand plays a vital role in the casting process, the industry faces several challenges, including the depletion of natural sand resources and increasing environmental regulations. Additionally, foundries must adapt to changing market demands, including the need for greater efficiency and reduced lead times.
Innovations in foundry sand technology are continually emerging, aimed at improving the casting process and enhancing the quality of the final products. For instance, the development of advanced sand additives and synthetic alternatives allows for better performance, improved recycling processes, and enhanced mold strength. Furthermore, ongoing research into alternative materials aims to identify new sources of foundry sand that can meet the industry's high standards while minimizing environmental impact.
Conclusion
Foundry sand is an indispensable component in the metal casting industry, with its unique properties profoundly affecting the quality of cast products. As the industry evolves, it continues to explore sustainable practices and innovative solutions to meet the challenges ahead. Understanding the role and importance of foundry sand is essential for appreciating its significant contributions to metal casting and the broader manufacturing landscape.
Post time:Aug . 07, 2024 13:30
Next:Optimal Sand Selection Techniques for Effective Sand Casting Processes in Metalworking Industries