Sand Used for Sand Casting
Sand casting, also known as sand mould casting, is a widely used metal casting process that involves creating a mold from sand in which molten metal is poured to create a desired shape. The sand used in this process plays a crucial role in determining the quality and precision of the final product. This article explores the types of sand commonly used in sand casting, their properties, and various considerations for selecting the right sand for a specific application.
Types of Sand Used in Sand Casting
1. Silica Sand This is the most common type of sand used in sand casting. Silica sand consists mainly of quartz, with very fine grains that provide excellent flowability and mold strength. It is resistant to high temperatures, making it suitable for casting metals such as aluminum, steel, and iron. Silica sand's availability and cost-effectiveness contribute to its popularity in foundries around the world.
2. Green Sand Green sand is a mixture of silica sand, clay, moisture, and other additives. The moisture content gives it a green character, allowing it to retain shape and harden upon drying. The clay component serves as a bonding agent, enhancing mold strength and preventing sand from collapsing under the weight of the molten metal. Green sand is favored for its versatility and lower production costs, making it an ideal choice for small to medium-sized castings.
3. Resin-Bonded Sand This type of sand is mixed with a resin and hardener, which polymerizes when heated, creating a strong and durable mold. Resin-bonded sand offers excellent dimensional accuracy and can produce more intricate designs compared to traditional green sand. This technique is often used in high-quality and complex castings, although it is generally more expensive than other sand types.
4. Oil-Bonded Sand Similar to resin-bonded sand, oil-bonded sand uses oil as a bonding agent. This type of sand allows for finer details in the castings, thanks to its ability to create smoother surfaces and sharper edges. It has good permeability, which is essential for the release of gases generated during the pouring process.
Properties of Sand for Casting
sand used for sand casting
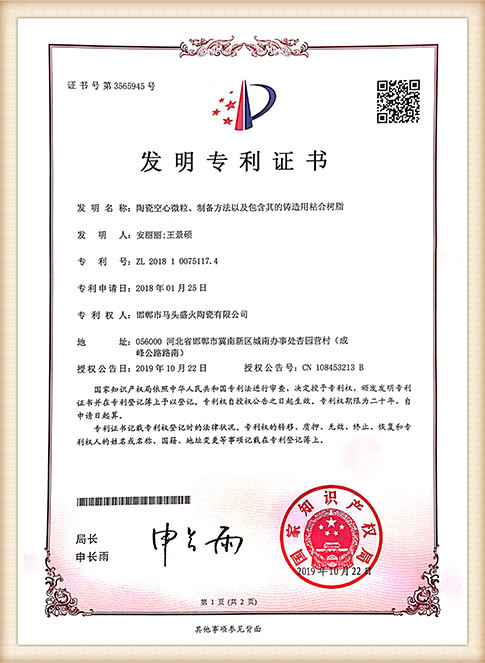
The properties of sand used in sand casting significantly influence the casting process. Some key properties include
- Grain Size The size of the sand grains can affect the surface finish of the casting
. Finer sand yields smoother surfaces, while coarser sand may result in rougher finishes.- Permeability This refers to the sand’s ability to allow gases to escape. High permeability is essential to prevent defects such as blowholes and ensuring a successful casting.
- Moisture Content The right balance of moisture content is crucial. Insufficient moisture can lead to poor mold strength, while excessive moisture can create steam during pouring, causing defects.
- Reusability Many types of sand can be reused multiple times in the casting process, which contributes to cost-effectiveness and minimizes waste in foundries.
Conclusion
Sand casting is a time-tested method utilized in various industries, from automotive to aerospace, owing to its versatility and cost-effectiveness. Selecting the right type of sand, understanding its properties, and taking into account factors such as grain size, permeability, and reusability are vital for achieving high-quality castings. As technology advances, innovations in sand casting materials and processes are likely to enhance its applications, making it a continued staple in metalworking for years to come. The choice of sand ultimately impacts not only the efficiency of the casting process but also the performance of the final product, highlighting the importance of informed decision-making in material selection.
Post time:Aug . 07, 2024 13:05
Next:Exploring the Advantages and Techniques of Sand Casting in Metal Fabrication and Manufacturing Processes