Lost Foam Sand Casting An Innovative Approach to Metal Casting
Lost foam sand casting is a revolutionary technique in the metal casting industry that combines the benefits of precision and efficiency. This process involves creating a foam pattern that is coated in sand to produce castings with complex shapes and thin walls. This method has gained popularity due to its ability to produce high-quality metal parts while reducing waste and improving turnaround times.
The lost foam casting process begins with the creation of a pattern made from polystyrene foam. This foam is lightweight, allows for intricate designs, and can be easily shaped to create a precise representation of the final product. Once the pattern is made, it is coated with a mixture of sand and a bonding agent. The sand used in this process is typically fine and allows for a high degree of detail, ensuring that even the most intricate designs are replicated faithfully in the final metal casting.
After coating, the foam pattern is placed into a mold, and molten metal is poured directly over it. As the molten metal comes into contact with the foam, it causes the foam to vaporize and leave a cavity that replicates the original pattern. This unique aspect of the lost foam casting process contributes to its name - the foam pattern is lost in the casting, leaving behind a highly accurate metal part. Unlike traditional sand casting, where a mold is created in two parts, lost foam casting eliminates the need for complex tooling, which helps reduce production costs and lead times.
lost foam sand casting
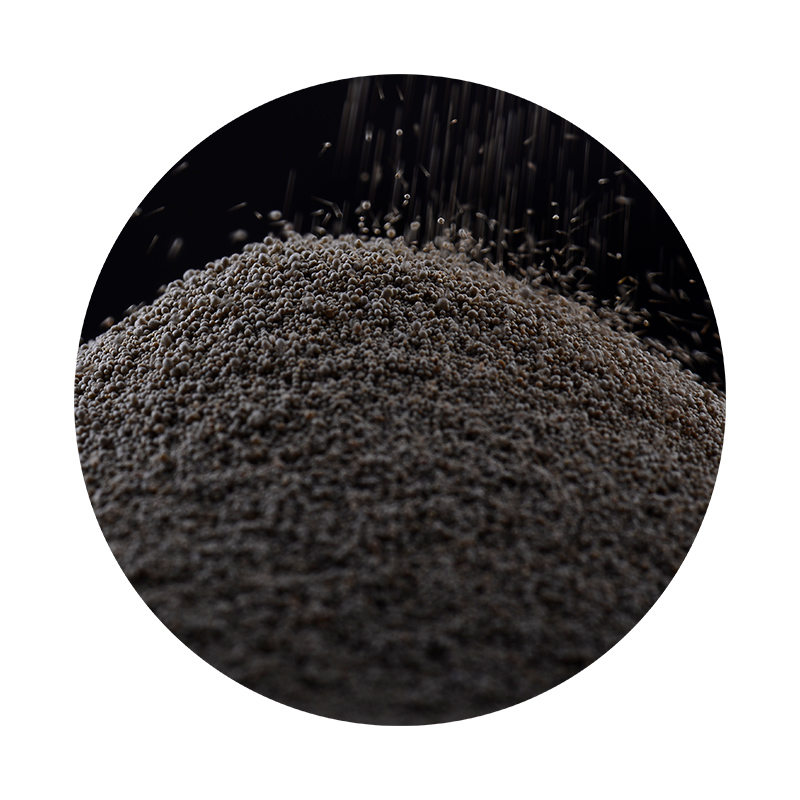
One of the significant advantages of lost foam sand casting is its ability to produce complex geometries that are often difficult or impossible to achieve with other casting methods. This capability is particularly valuable in industries such as automotive and aerospace, where lightweight and intricate components are essential for modern machinery. The lost foam process allows engineers and designers to push the boundaries of creativity while maintaining strict tolerances.
Moreover, lost foam casting is an environmentally friendly method. The use of foam patterns reduces the need for excessive materials, and the process generates less waste than traditional casting methods. Furthermore, the ability to recycle sand and reuse the foam materials contributes to a more sustainable manufacturing process. Many industries are increasingly prioritizing eco-friendly practices, making lost foam casting an attractive option for environmentally conscious manufacturers.
In terms of material versatility, lost foam casting is compatible with a wide range of metals, including aluminum, brass, and iron. This flexibility allows manufacturers to choose the most suitable material for their specific application, enhancing the overall performance of the final product. Additionally, the process can accommodate both small and large production runs, making it suitable for both prototyping and large-scale manufacturing.
In conclusion, lost foam sand casting represents a significant advancement in the field of metal casting. Its ability to produce intricate designs, reduce costs, improve efficiency, and minimize environmental impact positions it as a top choice for modern manufacturers. As industries continue to evolve and demand higher precision and quality, lost foam sand casting is likely to play a central role in meeting these challenges. With ongoing advancements in materials and technology, the future of lost foam casting looks promising, paving the way for even more creative and sustainable solutions in the metalworking landscape.
Post time:Aug . 22, 2024 03:39
Next:Various Sand Types Utilized in the Sand Casting Process for Metal Shaping