Types of Sand Used in Sand Casting
Sand casting is a widely utilized manufacturing process that involves pouring molten metal into a sand mold to create complex shapes. The quality of the casting and the efficiency of the process are heavily influenced by the type of sand used in the mold preparation. This article explores the various types of sand employed in sand casting, each with its unique characteristics and applications.
1. Silica Sand
Silica sand is the most common type of sand used in sand casting. Composed primarily of silicon dioxide (SiO2), it is derived from quartz, and its abundance makes it a cost-effective option for manufacturers. Silica sand has excellent properties, such as high refractoriness, which allows it to withstand high temperatures without decomposing. Its fine grain texture provides a smooth finish to castings, making it suitable for producing intricate details.
However, silica sand has a significant drawback it can release harmful silica dust when handled, posing health risks to workers. Therefore, safety measures such as dust control systems are essential when using silica sand in manufacturing processes.
2. Green Sand
Green sand is another popular choice for sand casting. It consists of silica sand mixed with clay, water, and a small amount of organic material. The presence of clay provides binding properties and helps the sand retain shape, allowing for excellent mold strength. Green sand molds are reusable, making this type of sand an environmentally friendly option.
The term green refers to the mold's moisture content rather than its color. Green sand molds are easy to work with and can be compacted well, which is critical for creating precision castings. However, the clay content can affect the surface finish, sometimes resulting in a slightly rougher texture compared to other sand types.
types of sand used in sand casting
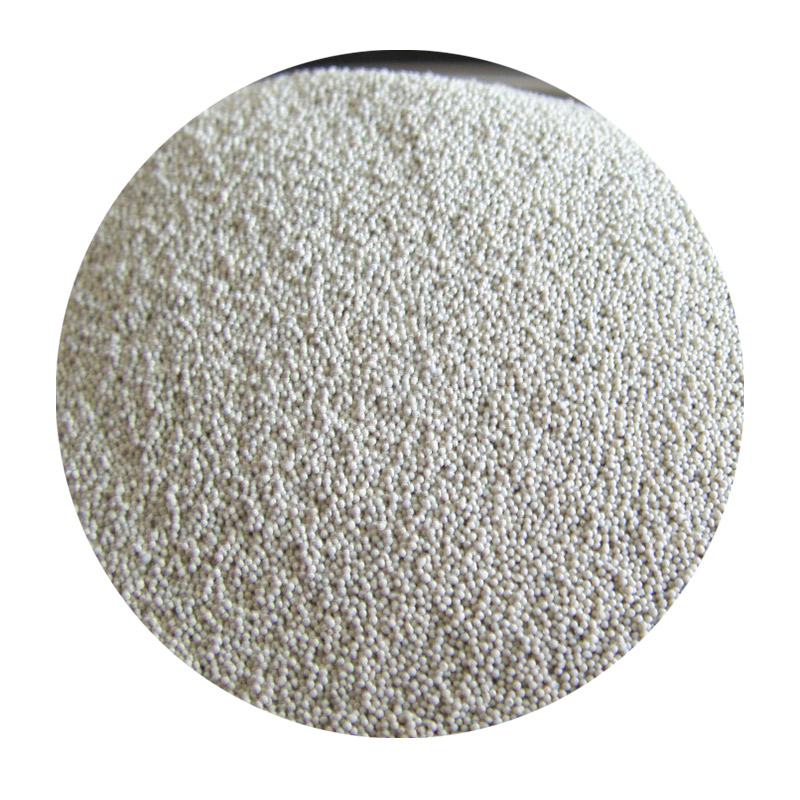
3. Resin Sand
Resin sand is a mixture of silica sand and a resin binder, which improves the mechanical properties of the mold. This type of sand is particularly known for its strength, thermal stability, and ability to produce finer details in castings. Resin sand systems can be configured to be either disposable or reusable, depending on the manufacturing needs.
The main advantage of resin sand is its adaptability to various casting processes, such as shell molding, where lightweight and precise molds are crucial. However, the cost of resin sand is typically higher than other sand types due to the additional materials and processes involved in its production.
4. Lost Foam Sand
Lost foam sand casting is a unique method using a foam pattern instead of a traditional sand mold. The pattern is coated with a layer of sand that typically contains a resin binder. Once the foam is heated, it vaporizes, leaving behind a cavity where the molten metal can be poured. This method allows for complex shapes and reduces the need for additional machining after casting.
The main advantage of lost foam sand casting is its ability to create highly detailed features and improve the surface quality of the final product. However, it requires careful control of the process, and the cost of foam patterns can be high.
Conclusion
In summary, the choice of sand type in sand casting significantly impacts the overall casting quality, mold strength, and production efficiency. Silica sand, green sand, resin sand, and lost foam sand each have their benefits and drawbacks, making them suitable for different applications. As manufacturers strive for higher precision and efficiency, understanding the characteristics of each sand type is essential for optimizing the sand casting process and achieving desired results.
Post time:Aug . 22, 2024 03:09
Next:Exploring the Benefits and Techniques of 3D Printing with Wet Sand Material