Understanding Foundry Molding Sand
Foundry molding sand is an essential material in the casting industry, playing a pivotal role in the production of metal parts through the casting process. The properties and characteristics of molding sand directly influence the quality of the final metal products, making it crucial to understand its composition, types, and applications.
Composition of Molding Sand
Molding sand is typically composed of four primary ingredients silica sand, clay, water, and additives. Silica sand, the principal component, provides the bulk of the sand mixture and contributes to the mold's strength and stability. The grain size, shape, and distribution of silica particles significantly affect the mold's permeability and its ability to withstand the pouring of molten metal.
Clay acts as a binder in the sand mix, helping to hold the grains together and giving the mold flexibility and strength. Common types of clay used include bentonite, which is known for its excellent bonding properties. Water is added to the sand mixture to activate the clay, enhancing its binding capabilities. Finally, various additives may be included to improve specific properties, such as thermal stability, permeability, and moldability.
Types of Molding Sand
Several types of molding sand are commonly used in foundries, each chosen based on the desired properties for particular casting applications
1. Green Sand This is the most widely used molding sand, composed of silica sand mixed with clay and water. It is called green because it is used in a damp state. Green sand molds allow for excellent gas permeability, making them suitable for a variety of casting processes.
2. Dry Sand In contrast to green sand, dry sand molds are allowed to dry before use. This type of sand is often used for more detailed and intricate castings that require a firmer mold structure. The drying process enhances the mold's thermal stability, allowing it to withstand higher temperatures during casting.
foundry molding sand
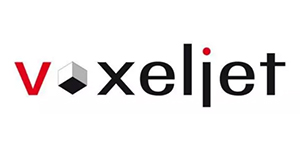
3. Resin Sand This type of molding sand uses synthetic resins as a binder instead of clay. Resin sand molds offer superior dimensional accuracy and surface finish, making them ideal for high-precision castings. They can be further categorized into phenolic and furan resin sands, each suited for specific applications.
4. Shell Sand This is a specialized type of sand that is bonded with thermosetting resins and used to create thin-walled molds. The shell mold process provides excellent surface finishes and is commonly used for intricate castings requiring high precision.
Applications in the Foundry Industry
Foundry molding sands are utilized in various casting methods, including sand casting, shell molding, and investment casting. Each method has its own set of advantages, but molding sand remains a fundamental component in achieving the desired cast properties.
The versatility of molding sand allows it to be employed in various industries, including automotive, aerospace, and general manufacturing. It is particularly crucial in producing parts such as engine blocks, transmission cases, and complex machinery components where dimensional accuracy and surface finish are critical.
Environmental Considerations
As the foundry industry evolves, so does the focus on sustainability and the environmental impact of molding sand. Innovations in sand recycling and the use of eco-friendly additives are on the rise. The recycling of spent sand can significantly reduce waste and lower material costs, contributing to a more sustainable production process.
Conclusion
In conclusion, foundry molding sand is a vital component in the metal casting industry, influencing the quality of the final products significantly. Understanding its composition, types, and applications helps foundry professionals to optimize casting processes and enhance product quality. As technological advancements continue to shape the industry, the importance of molding sand will remain a cornerstone of casting excellence.
Post time:Aug . 21, 2024 01:24
Next:Understanding the Process and Benefits of Resin Sand Casting Techniques