Resin Sand Casting An Innovative Approach to Metal Casting
Resin sand casting is an advanced and versatile method used in the production of metal components. This casting technique combines the traditional sand casting process with modern resin bonding, significantly enhancing the quality of castings while improving efficiency. As industries continue to evolve, resin sand casting is becoming a popular choice due to its numerous advantages and applications.
At its core, resin sand casting involves the use of sand mixed with a resin binder. The sand grains are coated with a thermosetting resin, which, when heated, cures to form a solid structure. This mixture is packed around a pattern, typically made from metal or plastic. Once the pattern is removed, the mold is ready for pouring molten metal. This process can be particularly beneficial for producing intricate shapes and designs that were once challenging to achieve with traditional methods.
One of the most notable benefits of resin sand casting is its ability to produce high-quality surface finishes. The resin-coated sand allows for a smoother finish compared to conventional green sand casting, where moisture is used as a binder. This reduction in surface roughness leads to parts that require minimal machining after casting, saving both time and costs in production. Furthermore, the high dimensional accuracy provided by resin sand molds means that manufacturers can achieve superior tolerances and reduce the likelihood of defects.
Additionally, resin sand casting is exceptionally versatile in terms of the metals and alloys that can be used. It is suitable for casting ferrous and non-ferrous materials, including aluminum, brass, and iron. The ability to accommodate a wide range of materials makes this method ideal for various industries, including automotive, aerospace, and machinery manufacturing.
resin sand casting
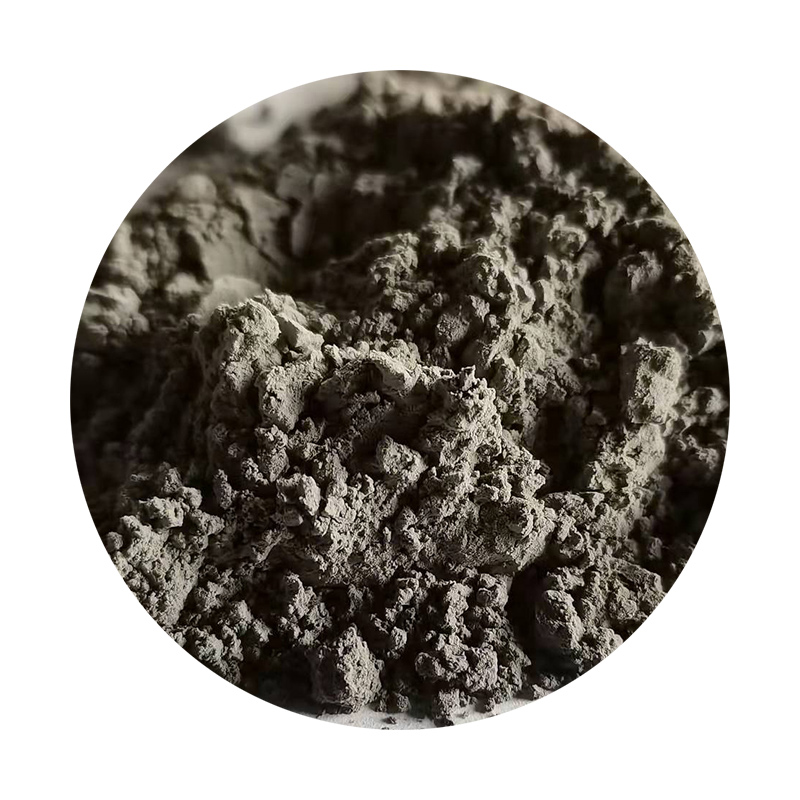
Another significant advantage of resin sand casting is its process efficiency. The rapid setting time of the resin allows for quicker mold production and turnaround between casting cycles. This speed enables manufacturers to respond more efficiently to market demands and reduces lead times for customers. Moreover, the reusability of the sand after separating it from the casting can lead to lower material costs, making resin sand casting a cost-effective solution in the long run.
The environmental impact of manufacturing processes is a growing concern across industries. Resin sand casting addresses this issue by minimizing waste and improving the recyclability of materials. Advanced techniques and modern resins have been developed to reduce harmful emissions, further making resin sand casting a more environmentally friendly option compared to traditional casting methods.
However, like any manufacturing process, resin sand casting does have some limitations. The cost of resin and the initial setup for producing molds can be higher than traditional sand casting techniques. Additionally, the handling of resins requires proper safety measures and environmental considerations.
In conclusion, resin sand casting is a progressive and efficient method of producing high-quality metal parts. Its combination of precise dimensional control, superior surface finishes, and rapid production times make it an appealing choice for manufacturers across various industries. As technology continues to develop, the applications and efficiency of resin sand casting are likely to expand, further solidifying its position as a leading method in the field of metal casting. By embracing this innovative technique, manufacturers can meet the demands of modern production while maintaining quality and sustainability.
Post time:Aug . 21, 2024 00:52
Next:Steel Sand Casting Foundry Innovations and Techniques for Efficient Production and Quality Improvement