Sand Casting Foundry Process An Overview
Sand casting is one of the most ancient and widely used manufacturing processes in the metalworking industry. It is the process of creating metal parts by pouring molten metal into a mold made from sand. This method has a long-standing reputation for its versatility and cost-effectiveness, making it a preferred choice for a variety of applications, from small intricate parts to large industrial components.
The sand casting process begins with the preparation of the mold. A pattern, which is a replica of the final product, is created using materials such as wood, metal, or plastic. The pattern is slightly larger than the final product to allow for material contraction during cooling. This replica is then used to form the mold cavity, which is typically made of a mixture of sand, clay, and water. The sand provides strength while the clay acts as a binding agent, ensuring the mold retains its shape.
Sand Casting Foundry Process An Overview
After the mold is assembled, it is subjected to quality checks to ensure it meets the necessary specifications. Once approved, the next step is melting the metal. Depending on the desired material properties, common metals used in sand casting include aluminum, iron, and bronze. The metal is melted in a furnace and must reach a temperature that is higher than its melting point, ensuring it is sufficiently fluid for pouring.
sand casting foundry process
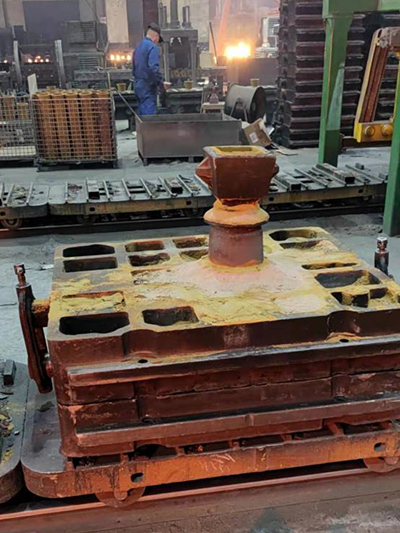
With the metal in liquid form, it is poured into the prepared mold. This step requires precision and care, as the temperature and speed of pouring can significantly affect the final properties of the cast part. After the mold is filled, it is allowed to cool. The cooling time can vary depending on the size and thickness of the cast part.
Once the metal has cooled and solidified, the mold is removed. This process is known as shakeout, where the sand is separated from the cast part. The sand can often be reclaimed and reused, making sand casting an environmentally friendly option. The final cast part is then subjected to various finishing processes, which may include grinding, machining, or painting to achieve the desired specifications and surface finish.
One of the major advantages of sand casting is its ability to produce complex shapes with great accuracy while accommodating a wide range of material types. Moreover, it is particularly cost-effective for low to medium production runs, as it requires relatively low initial investment in tooling and setup compared to other casting methods like die casting or investment casting.
However, sand casting does have some limitations. The surface finish of cast parts may not be as smooth as those produced through other processes, and achieving tight tolerances can be more challenging. Additionally, the sand mold has a limited lifespan, necessitating the creation of new molds for large-scale production.
In conclusion, sand casting remains a vital manufacturing process within the foundry industry. Its ability to produce diverse and intricate components makes it an invaluable technique for engineers and designers. As technology progresses, advancements in sand casting processes, materials, and equipment continue to enhance its efficiency and precision, ensuring its relevance in modern manufacturing applications. With its rich history and ongoing evolution, sand casting is poised to play a significant role in the future of metal parts manufacturing.
Post time:Aug . 14, 2024 23:16
Next:A Comprehensive Guide to Creating High-Quality Foundry Sand for Metal Casting Applications