How to Make Foundry Sand
Foundry sand is a critical material used in metal casting processes. It is primarily composed of high-quality silica sand, which can withstand high temperatures and is capable of forming intricate molds. In this article, we will explore the process of making foundry sand, the materials involved, and the steps to ensure that the sand meets the necessary specifications for successful metal casting.
Materials Required
1. Silica Sand The primary ingredient for foundry sand, it should be clean and free of impurities. The grain size often ranges from 70 to 100 mesh, depending on the specific casting requirements. 2. Clay Often added to enhance the cohesiveness of the sand mixture. Bentonite clay is typically used due to its excellent binding properties. 3. Water Used to moisten the sand and clay mixture to ensure proper binding during the molding process. 4. Additives Various additives can be incorporated to improve the properties of foundry sand, such as silt, carbonaceous materials, or other binding agents to enhance strength and reduce gas emissions during casting.
Steps to Make Foundry Sand
Step 1 Selecting the Right Sand
The first step in making foundry sand is selecting high-quality silica sand. It should be extracted from a reputable source and tested for purity, grain shape, and size. Avoid sand that contains contaminants like clay, silt, or organic materials that can compromise the mold's integrity.
Step 2 Testing and Processing
Before mixing, test the silica sand for its physical properties. Key tests include grain size analysis, moisture content, and thermal stability. Once the sand passes the required tests, it may need to be processed to eliminate any impurities. This can be accomplished through washing, drying, and screening.
Step 3 Mixing with Clay
how to make foundry sand
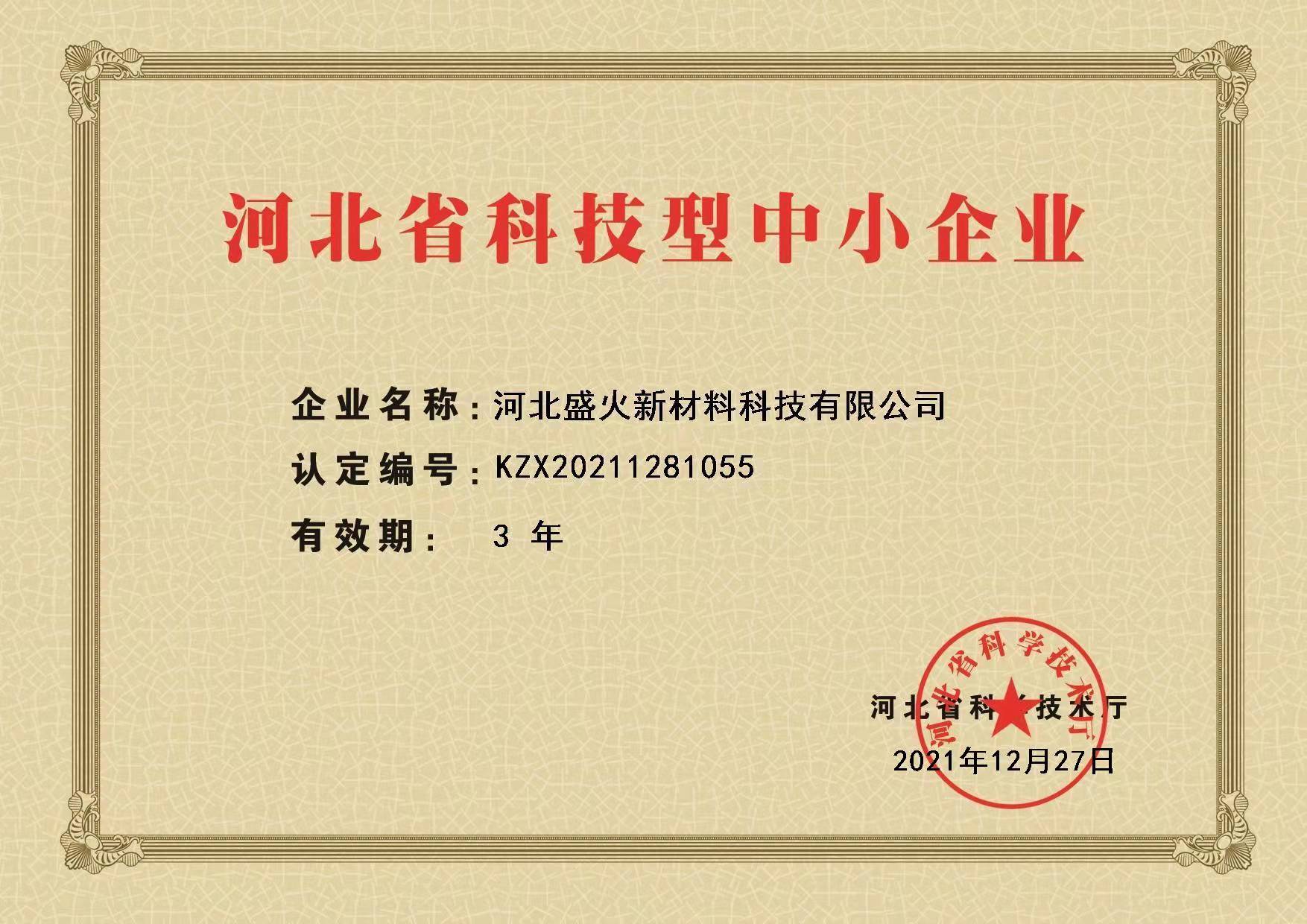
Once the silica sand has been processed, the next step is to add bentonite clay. A typical ratio for clay to sand is approximately 5-10% by weight, although this can vary based on specific requirements and the casting process. Thoroughly mix the sand and clay together to ensure an even distribution of the clay throughout the sand.
Step 4 Adding Water
After mixing the sand and clay, it is essential to add water to facilitate the binding process. The moisture content should be carefully controlled, typically around 2-4% for initial mixing. Gradually add water while continuously mixing until the desired consistency is achieved. The mixture should be damp enough to hold its shape but not so wet that it becomes clumpy.
Step 5 Testing and Adjusting
After mixing, it is crucial to test the properties of the foundry sand. Check for consistency, moldability, and strength. If the sand crumbles or does not hold shape, additional clay or water may need to be added. Conversely, if the mixture is too wet or sticky, more sand can be incorporated.
Step 6 Storing the Foundry Sand
Once the foundry sand meets all specifications, it should be stored properly to maintain its quality. Keep the sand in a dry, covered area to prevent moisture absorption and contamination. Proper storage will ensure that the foundry sand remains suitable for future casting operations.
Conclusion
Making foundry sand is a detailed process that requires careful selection of materials, precise mixing, and thorough testing. The quality of foundry sand directly affects the performance of molds and the overall success of metal casting. By following these steps, foundry operators can create high-quality sand that meets their specific needs, ultimately leading to better casting results and reduced production costs.
Post time:Aug . 14, 2024 22:59
Next:Creating a 3D Printed Sanding Machine for Enhanced Surface Finishing and Efficiency in Woodworking Projects