Understanding the Sand Casting Process
Sand casting, also known as sand mold casting, is one of the oldest and most widely used metal casting processes in manufacturing. It is particularly favored for its versatility and ability to produce complex shapes with relative ease and minimal costs. The fundamental principle of sand casting involves creating a mold from sand, pouring molten metal into the mold, and allowing it to solidify to form the desired part. This process is employed in various industries, including automotive, aerospace, and construction.
The Process Breakdown
The sand casting process typically involves several crucial steps
1. Pattern Making The first step is to create a pattern, which is a replica of the final product. Patterns can be made from various materials, including wood, metal, or plastic. The choice of pattern material often depends on the desired durability and the complexity of the part. Patterns are designed with allowances for shrinkage, machining, and dimensional changes.
2. Mold Preparation After the pattern is ready, the next step is to prepare the mold. This is done by compacting a mixture of sand (usually silica sand), a binder (such as clay), and water around the pattern. The compacted sand holds its shape and forms a cavity in the same shape as the desired part. Once the sand is packed, the pattern is removed, leaving a hollow mold.
3. Core Making For parts with internal cavities or complex geometries, cores made from sand can be inserted into the mold. Cores are typically produced from the same sand mixture as the mold. They create additional cavities within the casting that are essential for the part's final shape.
4. Melting and Pouring The next step involves melting the metal to its liquid state, which can be achieved through various methods such as induction melting, cupola melting, or electric arc melting. Once melted, the metal is poured into the mold cavity through a pouring basin and runner system, allowing it to fill the mold evenly.
5. Cooling and Solidification After pouring, the molten metal must cool and solidify. The cooling time varies depending on the type of metal and the section thickness of the casting. Once solidified, the mold is broken apart to retrieve the casting.
sand casting process
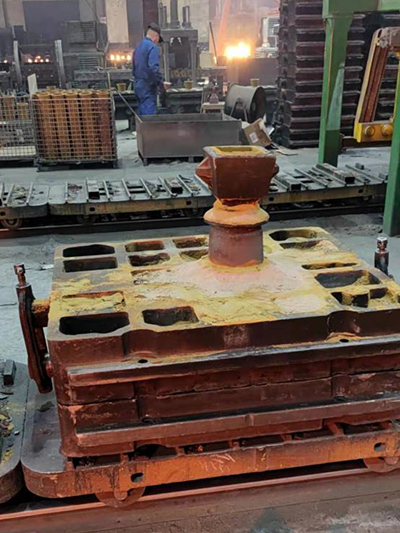
6. Finishing Operations After the casting is removed, it usually requires several finishing operations such as cleaning, machining, and surface treatment. This step is crucial for achieving the desired surface finish and dimensional accuracy.
Advantages of Sand Casting
Sand casting offers several advantages, making it an attractive choice for many manufacturers
- Cost-effectiveness The materials used for sand casting are relatively inexpensive, and the process allows for large-scale production at a low cost.
- Versatility It can be used to cast a wide range of metals and alloys, including iron, steel, aluminum, and bronze, making it suitable for various applications.
- Complex Geometries The process can accommodate intricate shapes, including hollow and complex parts, which can be difficult to produce with other methods.
- Low Setup Time Unlike more advanced casting techniques that require significant setup and tooling, sand casting can be rapidly reconfigured for different designs, enabling quick prototyping and production runs.
Conclusion
In summary, sand casting remains a fundamental technique in the manufacturing landscape, thanks to its simplicity and adaptability. As industries evolve and technological advancements continue, the sand casting process is likely to see improvements through the integration of modern techniques, software, and materials, ensuring its relevance for years to come. Whether it's for iconic automotive parts or complex aerospace components, sand casting plays a critical role in the manufacturing ecosystem, making it an essential process for engineers and manufacturers alike.
Post time:Jul . 25, 2024 14:14
Next:Exploring the Synergy Between 3D Printing and Sand Casting Techniques for Enhanced Manufacturing Solutions