3D Printing and Sand Casting Revolutionizing Manufacturing Processes
The intersection of technology and manufacturing has brought about transformative changes across various industries. Among these advancements, 3D printing and sand casting stand out as two prominent methods that have significantly influenced modern production techniques. Each method offers unique advantages while addressing different manufacturing needs, and their integration has the potential to revolutionize the way objects are designed and manufactured.
Understanding Sand Casting
Sand casting is one of the oldest manufacturing processes, dating back thousands of years. It involves creating a mold from sand and then pouring molten metal into that mold to form a desired shape. The versatility of sand casting allows for the production of complex geometries and a wide range of materials, including irons, steels, and non-ferrous metals. This process is particularly favored for large-scale components, such as engine blocks and heavy machinery parts, due to its cost-effectiveness and ability to produce large quantities.
However, traditional sand casting does come with its limitations. The process can be time-consuming, requiring the creation of molds that are often labor-intensive. Additionally, achieving precise tolerances can be challenging, leading to the need for post-processing steps that can add time and cost to production.
The Rise of 3D Printing
In contrast, 3D printing, or additive manufacturing, is a modern technique that builds objects layer by layer from digital models. This process allows for unmatched design freedom and the ability to create complex structures that would be impossible with traditional manufacturing methods. Unlike subtractive processes, 3D printing generates less material waste, making it an environmentally friendly option.
3d printer sand casting
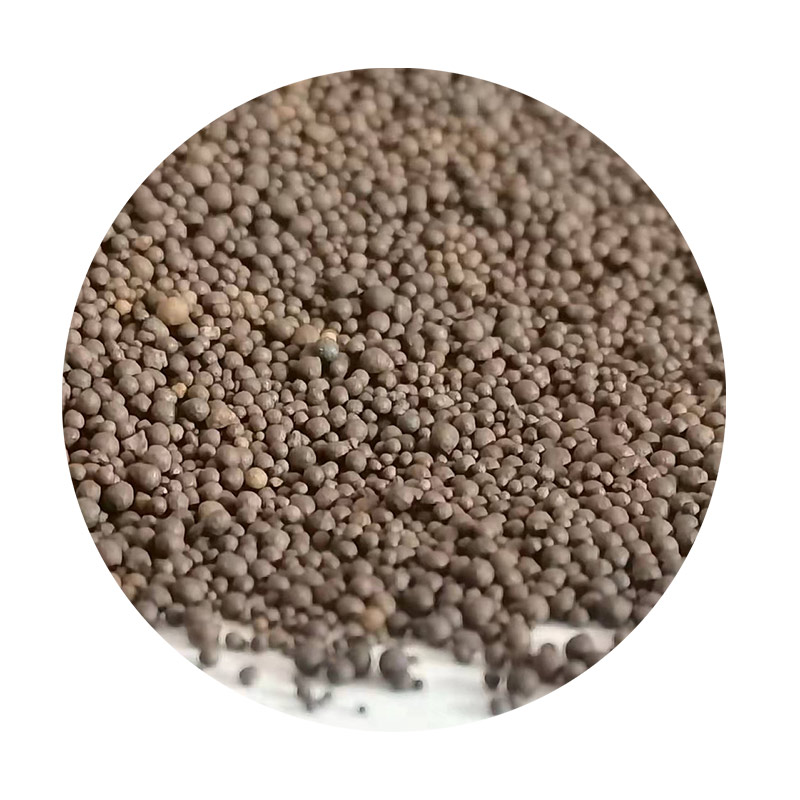
The convergence of 3D printing and sand casting has emerged as a powerful combination. By utilizing 3D printing to create sand molds for casting processes, manufacturers can overcome many challenges associated with traditional sand casting. Rapid prototyping, for instance, becomes achievable since 3D-printed molds can be produced quickly and at a lower cost than their traditionally manufactured counterparts.
Enhancing Efficiency through Integration
The integration of 3D printing in sand casting processes enhances overall efficiency. Manufacturers can quickly iterate their designs, making adjustments without the substantial time and costs of creating new physical molds. Furthermore, 3D-printed molds can be optimized for improved material flow and reduced defects, leading to higher-quality castings.
One notable application of this integration is seen in the aerospace and automotive industries, where lightweight components are critical. The ability to use 3D printing to create intricate sand molds allows manufacturers to produce geometric designs that are both lightweight and structurally sound. This not only reduces fuel consumption in aircraft but also improves performance in high-speed vehicles.
Conclusion
The synergy between 3D printing and sand casting exemplifies the evolution of modern manufacturing. By leveraging the strengths of both methods, manufacturers can enhance production efficiency and offer greater design flexibility. As technological advancements continue to drive innovation in these fields, the potential for increased sustainability and reduced lead times will continue to reshape the landscape of manufacturing. Ultimately, the combination of 3D printing and sand casting represents an exciting frontier that promises to enhance the capabilities of manufacturers across various industries, ensuring they remain competitive in a rapidly changing market. The future looks bright as these methods evolve together, paving the way for smarter, more efficient manufacturing processes.
Post time:Jul . 25, 2024 14:14
Next:Innovative Techniques and Benefits of Resin Coated Sand in Modern Casting Applications