The Types of Sand Used in Sand Casting
Sand casting is one of the most versatile and widely used metal casting methods, recognized for its simplicity and effectiveness. It involves creating a mold from a sand mixture that forms the negative shape of the desired metal part. The type of sand used in this process is critical to achieving the desired finish and integrity of the final product. This article explores the various types of sand used in sand casting, highlighting their properties, advantages, and applications.
1. Silica Sand
Silica sand is the most commonly used sand in sand casting. Composed primarily of silicon dioxide (SiO2), this sand is abundant and cost-effective. Silica sand provides excellent thermal stability, which is essential when pouring molten metal. It can withstand high temperatures without deforming or breaking down. The grains of silica sand vary in size and shape, which can be modified to influence the surface finish and porosity of the castings.
While silica sand is prevalent and functional, it does have its limitations. One of the significant concerns with silica is the potential for health issues due to inhalation of fine silica dust, which can lead to respiratory problems. As a response, many foundries have adopted measures to control dust exposure and have begun exploring alternative sand materials.
2. No-Bake Sand (Resin Sand)
No-bake sand, also known as resin sand, is a mixture of silica sand and resin binders that hardens at room temperature through a chemical reaction. This method allows for more intricate designs and finer detail than traditional sand molds. The use of no-bake sand enables higher dimensional accuracy and a better surface finish, reducing the need for additional machining.
The primary advantage of no-bake sand is its ability to capture fine details, making it suitable for complex shapes and high-quality casts. However, it is generally more expensive than traditional silica sand and may involve additional processing time due to the curing of the resin.
what type of sand is used in sand casting
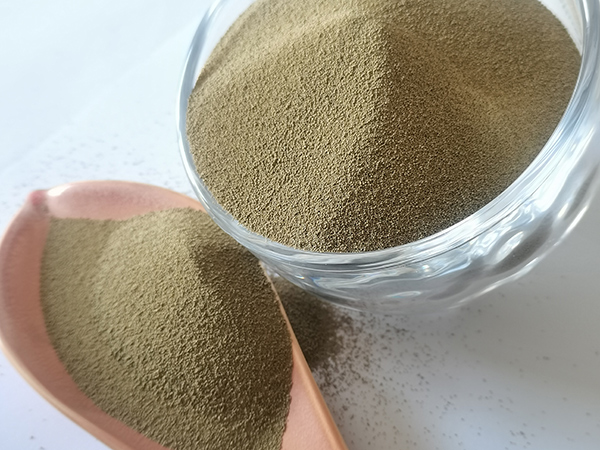
3. Green Sand
Green sand refers to a mixture of silica sand, clay, water, and a few other additives. It is called green because it is used in a moist state, which provides specific binding properties that help maintain the shape of the mold. The clay acts as a binder, while moisture adds further cohesive strength.
Green sand processes are relatively simple and inexpensive, making them popular in both small-scale foundries and industrial applications. This type of sand is especially favored for producing large items and is utilized for cast iron, aluminum, and steel components. Its effective adaptability to various casting techniques also contributes to its popularity.
4. Chemically Bonded Sands
Chemically bonded sands, such as cold-box and hot-box sands, employ chemical binders that harden upon the application of heat or a catalyst. Cold-box sand processes are characterized by the use of a gas that activates the binder; thus, it can be used in thin-walled castings. In contrast, hot-box sand involves the application of heat to cure the binder, producing robust molds suitable for heavy-duty applications.
These chemically bonded sands offer superior dimensional control and surface finish, making them ideal for high-precision castings. However, they also come with higher costs and handling requirements, further demanding proper management in the foundry.
Conclusion
The choice of sand type in the sand casting process significantly influences the properties of the final product, including surface finish, dimensional accuracy, and overall integrity. While silica sand remains the most widely used due to its affordability and availability, alternatives like no-bake sand, green sand, and chemically bonded sands provide additional options for specialized applications. By understanding the unique properties of each type of sand, foundries can better tailor their processes to meet the specific needs of their casting projects.
Post time:Aug . 08, 2024 07:55
Next:Evaluating the Pros and Cons of Utilizing Sand Casting in Manufacturing Processes