Advantages and Disadvantages of the Sand Casting Process
Sand casting, a widely used manufacturing process, involves pouring molten metal into a sand mold to create a desired object. This method has been prevalent for centuries due to its versatility and cost-effectiveness. However, like any manufacturing process, sand casting comes with its own set of advantages and disadvantages.
Advantages of Sand Casting
1. Cost-Effectiveness One of the most notable advantages of sand casting is its cost-effectiveness. The materials used, primarily sand, are relatively inexpensive and readily available. This makes the process an attractive option for small-scale production runs, prototyping, or situations where large quantities of complex parts are needed.
2. Versatility Sand casting is not limited to a specific type of metal. It can be used with a variety of metals, including aluminum, copper, and iron. This versatility makes it suitable for numerous applications across different industries, from automotive to aerospace.
3. Complex Shapes and Sizes The sand casting process can produce complex geometries and large components that would be challenging to achieve with other methods. The molds can be designed to accommodate intricate designs, allowing for greater creative freedom during the design phase.
4. Low Initial Investment The tools and equipment needed for sand casting are relatively simple and do not require a large initial investment. This is particularly beneficial for startups or small businesses looking to enter the manufacturing industry without significant financial risks.
5. Excellent Mechanical Properties Cast products often exhibit good mechanical properties, such as strength and durability. Sand-cast components can withstand high-stress applications, making them ideal for a variety of demanding environments.
advantages and disadvantages of sand casting process
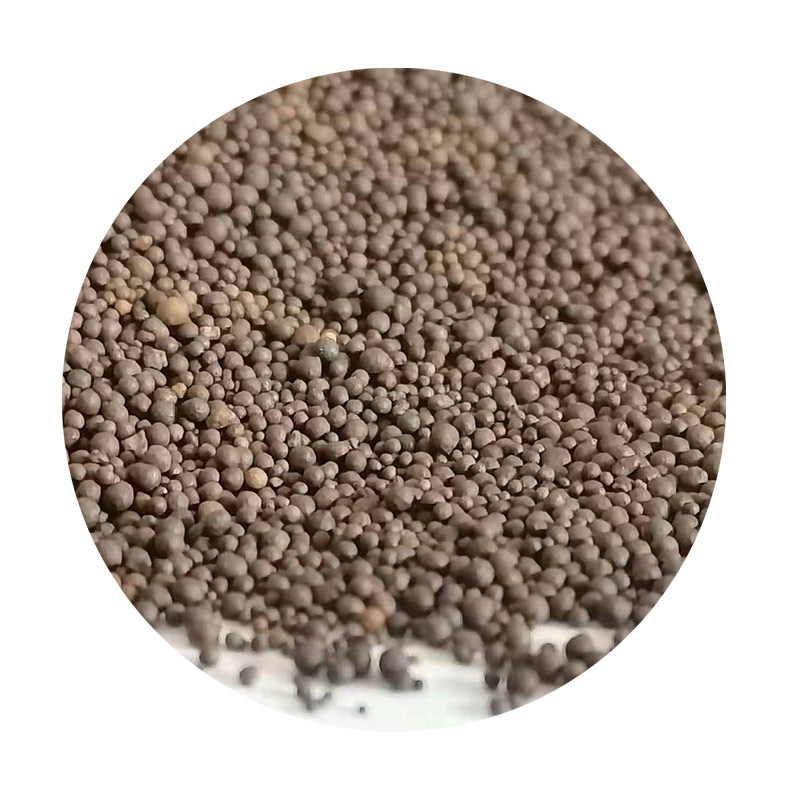
Disadvantages of Sand Casting
1. Surface Finish One of the primary drawbacks of sand casting is the surface finish quality. Cast parts typically have a rougher surface compared to those produced by methods such as injection molding or machining. This can necessitate additional finishing processes, which can increase production time and costs.
2. Dimensional Tolerances Sand casting generally requires larger tolerances compared to more precise casting methods. This can lead to variations in the final dimensions of the components, which is a significant consideration for applications where precise measurements are critical.
3. Labor-Intensive The sand casting process can be labor-intensive. Creating molds and performing finishing operations often require skilled labor, which can increase the overall cost of production. Additionally, the process can be time-consuming, especially for large or complex parts.
4. Environmental Concerns The sand casting process generates waste materials, such as used sand and metal scraps. While many foundries have improved recycling methods for sand, environmental impacts are still a consideration that manufacturers must address to remain compliant with regulations and sustainability standards.
5. Limitations in Production Volume While sand casting is effective for small to medium production volumes, it is not always the best choice for high-volume production. The time-consuming nature of creating molds and the labor involved can become prohibitive when large quantities are required.
Conclusion
In summary, sand casting is a valuable manufacturing process with distinct advantages, such as cost-effectiveness, versatility, and the ability to produce complex shapes. However, it also has its drawbacks, including surface finish quality, dimensional tolerances, and environmental concerns. Understanding these factors is crucial for manufacturers and designers when selecting the most appropriate casting method for their specific needs. As technologies evolve and sustainable practices are implemented, the sand casting process may continue to adapt and thrive in the ever-changing landscape of manufacturing.
Post time:Aug . 08, 2024 06:45
Next:Exploring the Techniques and Applications of Sand Casting in Chinese Manufacturing Industry