The Density of Foundry Sand An Overview
Foundry sand plays a crucial role in the metal casting industry, serving as a key component in the production of molds and cores. One of the most important physical properties of foundry sand is its density. Understanding the density of foundry sand is vital for foundry operations, as it influences the quality of castings, the efficiency of production processes, and the overall economics of the foundry.
What is Foundry Sand?
Foundry sand is typically composed of high-purity silica, often rounded or sub-rounded in shape, which contributes to its desirable properties for casting applications. It is primarily used to create molds for various metal casting processes, including sand casting, an ancient but still prevalent manufacturing method. The primary function of foundry sand is to provide a stable and consistent form that can withstand the heat of molten metal while delivering precise dimensional accuracy.
Importance of Density in Foundry Sand
The density of foundry sand is a measure of its mass per unit volume and can significantly affect casting quality. High-density sands can better withstand the thermal and mechanical stresses imposed during the casting process. If the sand is too loose or has a low density, it can cause issues such as poor mold integrity, increased permeability, and potentially lead to defects in the final cast product.
Moreover, density affects the handling and flow characteristics of the sand during the molding process. Foundry sands must be able to flow easily into molds and cores to ensure uniform coating and adequate filling. Therefore, the appropriate density is important not only for the structural integrity of the mold but also for the efficiency of the casting process.
density of foundry sand
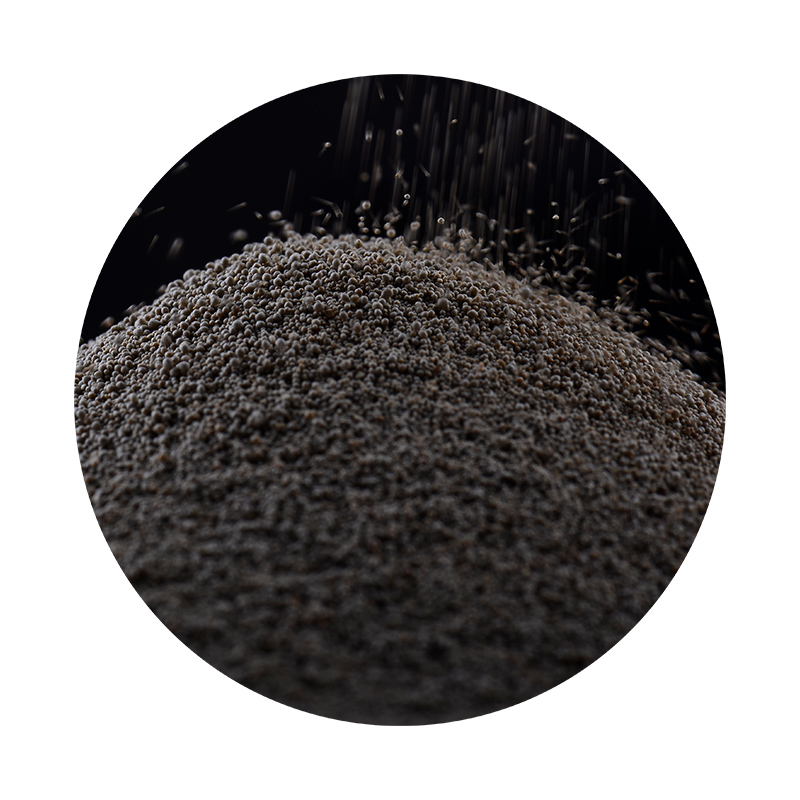
Factors Influencing the Density of Foundry Sand
Several factors can influence the density of foundry sand, including sand grain size, shape, moisture content, and the presence of additives. Finer sands tend to have higher densities because they pack together more tightly than coarser sands. The shape of the sand grains also plays a role; rounded grains typically have lower densities compared to angular grains, which can interlock more effectively and provide higher packing density.
Moisture content is another critical factor that can alter the density. Foundry sands are often mixed with a binder and water to enhance mold strength and cohesion. However, excessive moisture can lower the density and lead to other casting problems. Thus, controlling the moisture level is essential for maintaining the desired density of the foundry sand.
Measuring Density
The density of foundry sand is typically measured in grams per cubic centimeter (g/cm³) or pounds per cubic foot (lb/ft³). Various methods can be used to measure the density, including using a pycnometer, volumetric flask, or specialized sand density test apparatus. Regular measurement and monitoring of sand density help ensure that it meets the specifications required for different casting applications.
Conclusion
In conclusion, the density of foundry sand is a critical parameter that impacts the performance of the sand in molding processes and the quality of cast products. Its influence on mold strength, thermal resistance, and handling characteristics makes it an essential consideration for foundry operations. By understanding and controlling the factors that affect density, foundries can enhance their production efficiency and product quality, ultimately leading to improved economic outcomes. As the industry continues to evolve, ongoing research into the properties and behaviors of foundry sand will further optimize casting processes and enhance the performance of metal castings.
Post time:Aug . 10, 2024 02:15
Next:Exploring Innovative Techniques in Sand Casting with Advanced Resin Materials for Enhanced Craftsmanship and Durability