Sand Casting Resin An Innovative Approach to Metal Casting
Sand casting is one of the oldest and most versatile metal casting processes known to mankind. Traditionally, sand is used as a mold material, with metal poured into a cavity created in this sand. Recently, advancements in materials technology have introduced a new dimension to this age-old technique the use of resin in sand casting. This combination not only enhances the properties of the cast product but also improves efficiency and precision in the casting process.
Understanding Sand Casting
Sand casting involves creating a mold from sand mixed with a bonding agent, which can be clay or resin. This mixture allows for the formation of intricate shapes and details. Once the mold is prepared, molten metal is poured into the cavity, which solidifies into the desired shape. The mold is then destroyed to reveal the finished product. This process is widely used across industries, from automotive parts to intricate sculptures.
The Role of Resin in Sand Casting
The introduction of resin into sand casting has revolutionized the way molds are created. Unlike traditional clay-bound sands, resin-bound sands provide greater strength and durability. Resins react chemically when mixed with sand and then cured, creating a robust mold that can withstand the high temperatures of molten metal. This chemical bonding enhances the mold's integrity, resulting in high-quality castings with excellent surface finishes.
One of the primary advantages of using resin is its ability to produce more precise and intricate molds. This means that manufacturers can reduce the finishing work required after the casting process, ultimately saving time and costs. Moreover, the accurate reproduction of fine details allows for creating complex geometries that were previously challenging to achieve with traditional sand casting methods.
sand casting resin
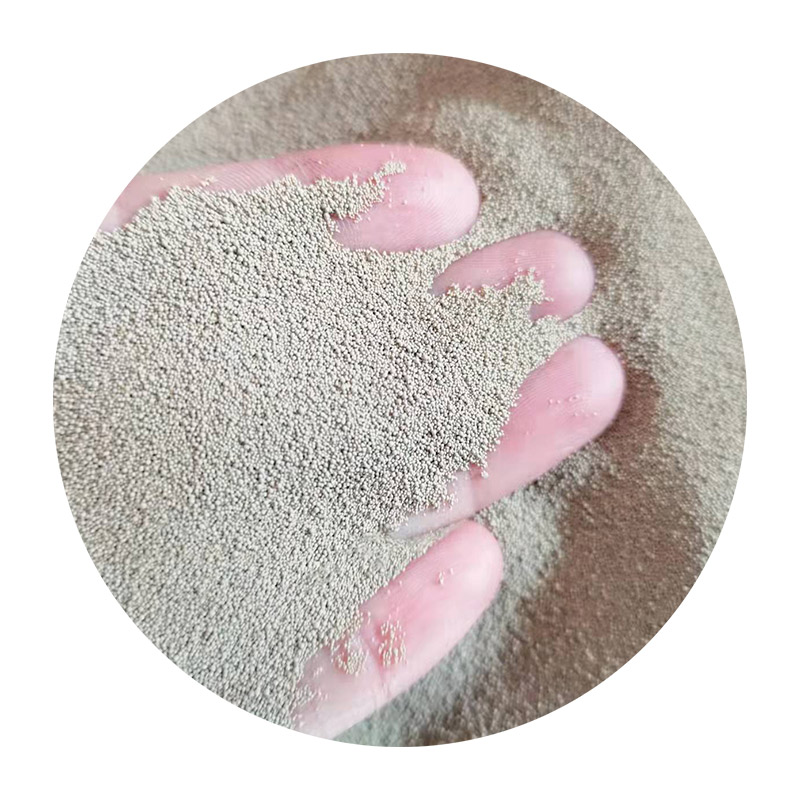
Environmental Considerations
Another important aspect of resin sand casting is its potential for improved environmental sustainability. Traditional sand casting processes often lead to significant waste and require large amounts of sand, which may not be reused effectively. In contrast, resin systems can be designed to minimize waste through recycling and reusability. Furthermore, advances in eco-friendly resin formulations reduce the environmental impact, making the process more aligned with current sustainability goals.
Applications of Sand Casting Resin
The versatility of resin sand casting makes it suitable for various applications. In the automotive industry, manufacturers utilize this method for producing engine blocks and intricate components that demand precision and durability. In the field of art and design, artists and sculptors can take advantage of resin sand casting to create unique pieces that showcase fine details and complex shapes.
Additionally, the aerospace sector benefits from resin sand casting for creating lightweight yet durable components. These components are not only essential for performance but also contribute to fuel efficiency and reduced emissions—qualities increasingly demanded in modern aviation.
Conclusion
Sand casting resin stands as a testament to the evolution of manufacturing processes. By integrating resin into traditional sand casting, industries have witnessed improved accuracy, reduced waste, and enhanced product quality. As technology continues to advance, the application of resin-based sand casting promises to play a significant role in various sectors, paving the way for more innovative and sustainable practices in metal casting. As we move forward, the fusion of traditional methods with modern materials not only preserves the rich history of casting but also reshapes the future of manufacturing.
Post time:Aug . 10, 2024 01:15
Next:Understanding the Principles and Techniques Behind Sand Casting in Foundry Manufacturing Processes