What is Resin Coated Sand?
Resin coated sand is a specialized material used primarily in the foundry industry for the production of metal castings. It is produced by coating high-quality silica sand with a thermosetting resin, which provides several advantages over traditional sand casting methods. This article explores what resin coated sand is, its production process, applications, and benefits.
Production Process
The process of creating resin coated sand involves mixing high-purity silica sand with a resin, typically a phenolic resin, and a hardener. This mixture is heated to facilitate the coating of the sand grains with the resin. The heat activates the resin, allowing it to bond to the sand particles. Once the necessary coating has been achieved, the coated sand is typically cooled and can be stored for later use.
The quality of the silica sand used is crucial. It must possess the right grain size, shape, and purity to ensure optimal performance in the casting process. The resin coating significantly improves the sand's properties, enhancing its usability in various applications.
Applications
Resin coated sand is widely employed in the foundry industry for creating molds and cores for steel, aluminum, and iron castings. One of the primary applications is in producing automotive parts, machinery components, and various industrial machinery. The ability of resin coated sand to withstand high temperatures and give fine details makes it particularly suitable for complex geometries often found in modern manufacturing.
In addition to the foundry industry, resin coated sand has found applications in other sectors, including construction, where it is used in the production of precast concrete products. Its unique properties also make it suitable for the oil and gas industry, specifically for proppant materials used in hydraulic fracturing.
what is resin coated sand
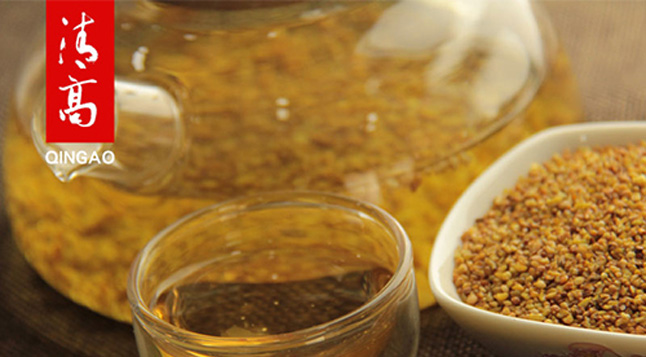
Benefits
One of the standout benefits of using resin coated sand is its superior strength and durability compared to traditional sand molds. The resin coating provides enhanced binding characteristics, allowing for finer details and smoother surfaces in cast products. This is particularly valuable in industries where precision is critical.
Another significant advantage is the reduced need for mold release agents when using resin coated sand. Traditional sand often requires additional coatings to prevent the metal from sticking to the sand, which can add complexity and cost to the casting process. However, the resin allows for a smoother release, facilitating easier demolding and reducing production time.
The thermal stability of resin coated sand also exceeds that of conventional sands, enabling it to maintain its shape and properties even under extreme heat. This makes it an ideal choice for casting materials that require high temperatures, minimizing the risk of mold distortion or failure during the casting process.
Moreover, resin coated sand can be customized for specific applications by altering the type of resin used, the coating thickness, and the choice of silica sand. This flexibility allows manufacturers to tailor the material for a variety of casting requirements, enhancing productivity and reducing waste.
Conclusion
In summary, resin coated sand is a versatile and high-performance material that is revolutionizing the foundry industry and beyond. Its ability to produce high-quality castings with superior detail and strength makes it an essential component in modern manufacturing. With ongoing advancements in resin technology and processing techniques, the use of resin coated sand is expected to expand, offering even more opportunities for efficiency and precision in various industries.
Post time:Jul . 21, 2024 01:02
Next:A Guide to Stainless Steel Sand Casting Techniques and Advantages for Modern Foundries