The Art and Science of Stainless Steel Sand Casting Foundries
Stainless steel sand casting is a critical method employed in the manufacturing of various components across multiple industries. The technique involves pouring molten stainless steel into a sand mold, which is then allowed to cool and solidify into the desired shape. This process is widely appreciated for its ability to produce complex geometries, high precision, and excellent surface finishes. In this article, we explore the intricacies of stainless steel sand casting foundries, highlighting the advantages, applications, and challenges inherent in this ancient yet modern manufacturing technique.
The Art and Science of Stainless Steel Sand Casting Foundries
The sand casting process begins with the creation of a pattern, typically made from wood, metal, or plastic, which serves as a template for the mold. Once the pattern is prepared, it is pressed into a special sand mixture, often containing silica sand and a binding agent, to form a mold cavity. The pattern is then removed, leaving a hollow impression that mirrors the design. After assembling the two halves of the mold, molten stainless steel is poured into the cavity. As the metal cools and solidifies, it takes on the shape of the mold. Once the casting has cooled sufficiently, the sand mold is broken away to reveal the final product.
stainless steel sand casting foundry
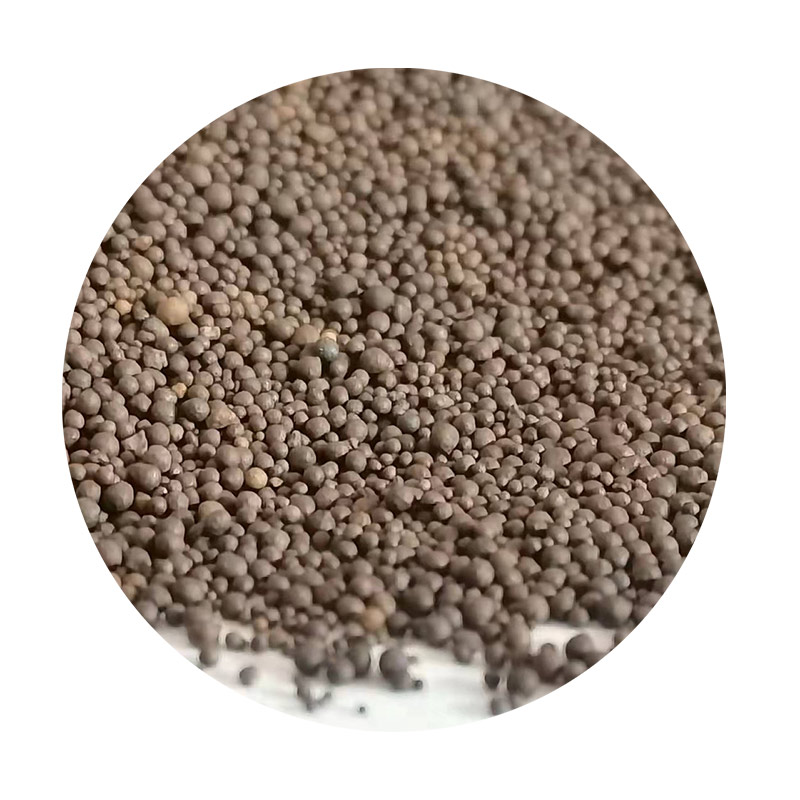
While stainless steel sand casting has many advantages, it is not without its challenges. The quality of the final product largely depends on the precision of the mold and the quality of the stainless steel used. The presence of impurities or variations in the melting process can lead to defects such as porosity or inclusions, affecting the mechanical properties of the cast. Additionally, maintaining consistent temperatures during melting and molding is critical to ensuring uniform cooling and solidification rates. Foundries must also consider the environmental impact of their operations, as sand casting can produce waste material and emissions that need to be managed responsibly.
Advanced technologies have been incorporated into the sand casting process to address these challenges. Numerical simulations and computer-assisted design tools are now commonly utilized to optimize mold designs and predict cooling rates, thereby enhancing the final product's quality. Moreover, the introduction of automated systems in foundries has increased production rates and ensured greater precision in the casting process.
The future of stainless steel sand casting foundries looks promising as industries continue to embrace innovation and sustainability. With the rise of additive manufacturing and other advanced fabrication techniques, foundries are poised to evolve. Techniques such as 3D printing for mold creation are already being explored, allowing for greater design freedom and reduced lead times. Furthermore, the utilization of recycled materials in the sand mixture and the stainless steel itself aligns with global sustainability efforts, making this traditional manufacturing method more environmentally friendly.
In conclusion, stainless steel sand casting foundries play a vital role in producing high-quality components that meet the demands of various industries. The combination of artistic craftsmanship and scientific precision allows for the creation of intricate designs and robust products. As technology advances, the sand casting process will continue to adapt, finding new ways to optimize production, enhance quality, and promote sustainability—all while maintaining the timeless art of casting that has been honed over centuries.
Post time:Jul . 21, 2024 01:02
Next:Exploring the Benefits and Techniques of Sand Casting for Steel Manufacturing Applications