Understanding Resin Coated Sand
Resin coated sand (RCS) is a specialized material widely used in the foundry industry, particularly in the manufacturing of metal castings. Its development has been a significant advancement in casting technology, enhancing the overall quality of cast products, reducing defects, and improving operational efficiencies.
What is Resin Coated Sand?
Resin coated sand is essentially sand that has been coated with a resin binder. This process involves mixing fine silica sand with thermosetting resins, which are adhesives that harden when exposed to heat. The resulting material retains the shape and consistency of traditional sand but offers superior performance characteristics due to the resin coating.
Composition and Production
The production of resin coated sand typically starts with high-quality silica sand as the base material. The sand is then cleaned and treated to remove any impurities. Once prepared, it is mixed with specific types of resins, such as phenolic or epoxy resins. The mixing process is carefully controlled to ensure an even distribution of the resin over the sand particles.
After mixing, the coated sand is usually cured by heating, which solidifies the resin and forms a durable, hard structure. This curing process is crucial as it sets the sand for use in various casting applications, providing enhanced mold strength and stability during the metal pouring process.
Advantages of Resin Coated Sand
1. High Strength and Stability One of the most significant advantages of resin coated sand is its ability to maintain high strength during the casting process. The resin binder provides excellent dimensional stability, which reduces mold deformation and leads to more accurate castings.
what is resin coated sand
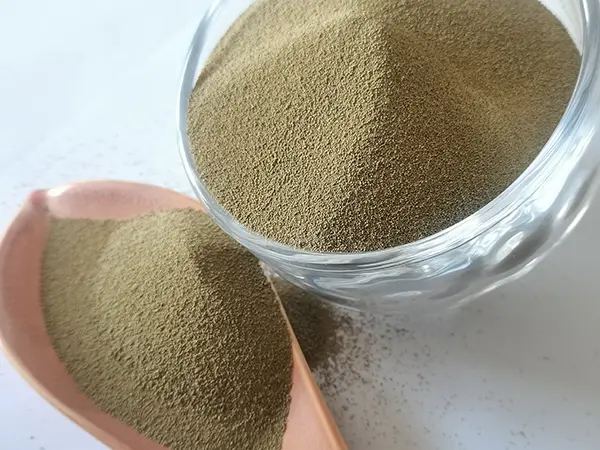
2. Smooth Surface Finish Castings made with resin coated sand often exhibit a superior surface finish. The fine grain structure created by the resin allows for smoother surfaces, reducing the need for additional machining and finishing processes.
3. Reduced Defects The use of resin coated sand significantly reduces the occurrence of casting defects, such as blowholes and sand inclusions. The improved flowability of the resin-sand mixture allows for better filling of complex molds, resulting in higher-quality finished products.
4. Environmental Considerations Many modern resins used in coated sand processes are designed to be less harmful to the environment compared to older binder technologies. Some resins are even made from renewable resources, which aligns with the industry's growing focus on sustainability.
Applications
Resin coated sand is used in various applications, primarily in the production of ferrous and non-ferrous castings. Industries such as automotive, aerospace, and heavy machinery rely on RCS for the manufacturing of engine blocks, cylinder heads, and intricate components that require high precision and reliability.
Additionally, RCS is becoming increasingly popular in other areas, such as in the production of molds for art and sculpture, as well as in the construction of architectural features where detailed designs are crucial.
Conclusion
Resin coated sand represents a critical advancement in casting technology that has revolutionized the foundry industry. By providing high strength, stability, and a superior surface finish, it addresses many of the traditional challenges associated with sand casting. As industries continue to prioritize quality and efficiency, the role of resin coated sand will likely expand, leading to even more innovative applications and advancements in the field. With ongoing developments in resin technology, the future of sand casting looks promising, paving the way for new opportunities and enhanced production capabilities.
Post time:Aug . 21, 2024 11:18
Next:Innovative Techniques and Benefits of Sand Castings in Modern Manufacturing Processes