Sand Castings An Overview of a Timeless Manufacturing Technique
Sand casting, one of the oldest forms of metal shaping, has been an essential manufacturing process for centuries. This method involves creating a mold from sand and then pouring molten metal into it to create various parts and components. Its simplicity, versatility, and cost-effectiveness make sand casting a popular choice in various industries, including automotive, aerospace, and art.
The Process of Sand Casting
The sand casting process begins with the creation of a pattern, which is a replica of the final product. This pattern can be made from various materials such as wood, metal, or plastic, depending on the complexity and desired finish of the final product. Once the pattern is completed, a mold is formed by packing sand around it. The sand mixture usually contains a binder, allowing it to hold its shape while also being easily removable.
After forming the mold, the pattern is removed, leaving a cavity that mirrors the intended shape of the final piece. The two halves of the mold are then assembled, ensuring that they fit together perfectly to prevent any leakage of the molten metal later on. The final step in the preparation involves creating channels, known as gates and risers, that allow the molten metal to flow into the cavity and help trap any air pockets.
Once the mold is prepared, molten metal is poured into the cavity. The heat from the liquid metal causes the sand to retain its shape despite the high temperature. After allowing sufficient time for the metal to cool and solidify, the mold is broken apart, revealing the cast metal component. Any necessary finishing processes, like machining or sanding, may follow to achieve precise dimensions and surface quality.
Advantages of Sand Casting
sand castings
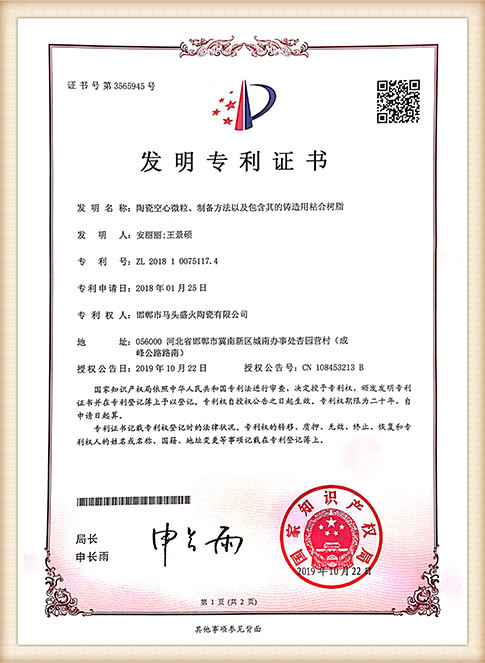
One of the most significant advantages of sand casting is its cost-effectiveness. The materials involved—primarily sand and a binder—are relatively inexpensive, making it an ideal choice for both large and small production runs. Additionally, sand casting is suitable for a wide range of metals, including iron, steel, aluminum, and bronze, allowing manufacturers to adapt the process for different applications.
Another notable benefit is its versatility. Sand casting can accommodate complex geometries and large parts that are challenging to manufacture with other techniques. This capability makes it particularly valuable in industries that require custom components, such as the aerospace sector, where precision and quality are paramount.
Moreover, sand casting allows for the production of large components with a relatively fast turnaround time. While the initial setup, including creating the mold, can be time-consuming, once established, the process rallies to quickly produce multiple casts.
Limitations and Future Trends
Despite its many advantages, sand casting does have limitations. Surface finish and dimensional accuracy may not meet the strict requirements for every application. Therefore, further machining or finishing processes might be necessary to achieve the desired specifications. Additionally, the casting may have some porosity, which can be detrimental in applications requiring high strength and durability.
Looking to the future, advancements in technology are poised to enhance sand casting processes. Techniques such as 3D printing are beginning to revolutionize mold creation, allowing for greater precision and reduced lead times. Additionally, improvements in materials and binders are being researched to enhance the quality and performance of sand casts.
In conclusion, sand casting remains a cornerstone of manufacturing due to its versatility, cost-effectiveness, and ability to produce complex components. While it faces certain limitations, ongoing technological advancements suggest a bright future for this ancient yet enduring method of metalworking. As industries evolve, sand casting will continue to adapt, proving once again that innovation can breathe new life into traditional practices.
Post time:Aug . 21, 2024 10:39
Next:Analyzing the Key Findings and Implications of Sand Casting Techniques and Applications