Sand Casting Foundry Process
Sand casting is one of the oldest and most widely used metal casting processes. It involves creating a mold from sand, which is then used to shape molten metal into a desired form. This process has been a fundamental technique in the manufacturing sector for centuries due to its versatility, cost-effectiveness, and ability to produce complex geometries.
The Sand Casting Process
The sand casting process consists of several key steps pattern making, mold preparation, metal pouring, cooling, and finishing
.1. Pattern Making The first step in sand casting is the creation of a pattern, which is a replica of the final object to be cast. Patterns can be made of various materials such as wood, metal, or plastic. The size and shape of the pattern must take into account the shrinkage of the metal as it cools, so patterns are often slightly oversized.
2. Mold Preparation The pattern is then placed in a sand mixture to create the mold. This mixture typically consists of silica sand, a bonding agent (like clay), and water. The sand is packed tightly around the pattern, ensuring that it captures the fine details. After the pattern is removed, two halves of the mold are created, which will be later joined together.
3. Metal Pouring Once the mold is prepared, molten metal is poured into the cavity formed by the two halves of the mold. The temperature and composition of the molten metal depend on the specific type of metal being cast. Common metals used in sand casting include aluminum, iron, and brass. The pouring process must be carefully controlled to avoid defects such as air bubbles or inclusions, which can compromise the integrity of the final product.
4. Cooling After the mold has been filled, the metal is left to cool and solidify. The cooling time may vary depending on the thickness of the cast object and the type of metal used. It is essential for the metal to cool slowly to prevent cracking and to ensure uniformity in the metal structure.
sand casting foundry process
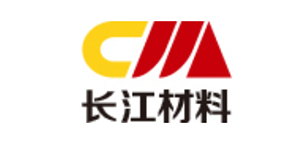
5. Finishing Once the metal has cooled and hardened, the mold is broken apart to retrieve the cast object. This process can involve various finishing techniques such as grinding, polishing, or machining to achieve the desired surface finish and dimensions. Any additional features, such as holes or threads, may also be added during this stage.
Advantages of Sand Casting
Sand casting offers numerous advantages that make it a popular choice in various industries. One of the main benefits is its ability to produce large and intricate parts without the need for specialized equipment. The durability and reusability of sand molds allow for high production volumes with minimal investment. Additionally, the sand casting process is not limited to a single metal type, providing flexibility for manufacturers to work with various alloys.
Applications of Sand Casting
Sand casting is used across multiple sectors, including automotive, aerospace, and industrial machinery. It is particularly valued for producing engine components, hardware fittings, and decorative items. The ability to create complex geometries makes it an ideal choice for prototypes as well as mass production.
Conclusion
In summary, sand casting is a time-honored manufacturing process that effectively bridges the gap between artistry and engineering. Its simple yet effective methodology has stood the test of time, adapting to the evolving needs of various industries. As manufacturers continue to seek cost-effective and versatile production methods, sand casting remains a key player in the foundry landscape, demonstrating the enduring appeal of this ancient technique.
Post time:Aug . 21, 2024 02:01
Next:Understanding the Importance of Foundry Molding Sand in Metal Casting Processes