Resin Bonded Sand Casting A Comprehensive Overview
Resin bonded sand casting is a modern and efficient metal casting process that is widely utilized in manufacturing industries for the production of complex shapes and components. This method is particularly favored due to its ability to produce high-precision, high-quality castings with excellent surface finishes.
At the core of the resin bonded sand casting process is the use of sand as the primary mold material, which is mixed with a resin binder. The resin used in this process can be either phenolic or urethane-based, which, when activated by heat or chemical catalysts, hardens the sand mixture to form a solid mold. This innovation addresses several limitations associated with traditional sand casting methods, where water-based binders are used, resulting in weaker molds that may not withstand high temperatures or the rigors of metal pouring.
One of the major advantages of resin bonded sand casting is its versatility. This technique can efficiently create intricate designs and details that would be challenging or impossible to achieve with conventional casting methods. The ability to produce thin-walled sections without compromising the integrity of the casting makes it particularly appealing for industries such as aerospace, automotive, and precision engineering.
Moreover, the process allows for rapid prototyping and shorter lead times, which is critical in today's fast-paced manufacturing environment. Since the sand molds are created using patterns (often made of metal or plastic), manufacturers can quickly produce molds for testing and development. This capability not only reduces costs but also enables more frequent iterations in design, ultimately leading to better product outcomes.
resin bonded sand casting
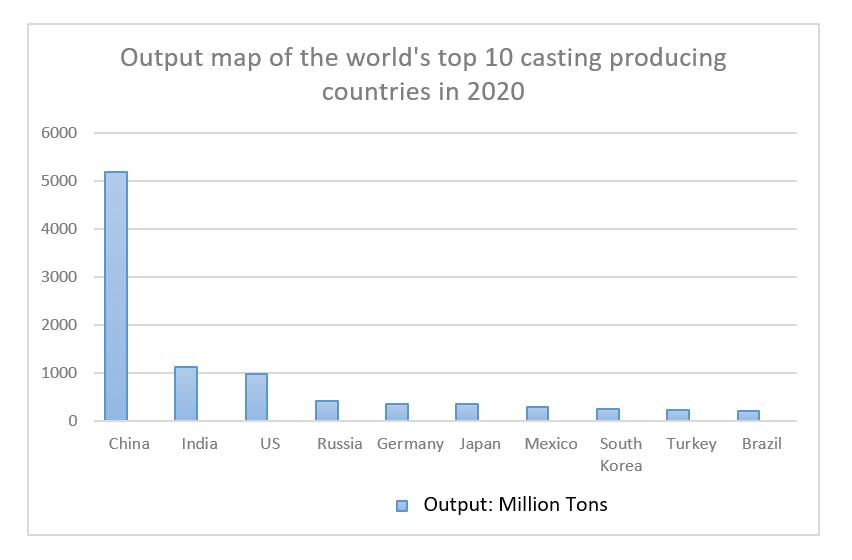
The environmental impact of resin bonded sand casting has also become a point of discussion
. Traditional sand casting can produce a significant amount of waste, particularly due to the use of conventional binders. In contrast, modern developments in resin formulations have led to the creation of more environmentally friendly options, which help minimize excess material and reduce the overall carbon footprint of the casting process.However, despite its many benefits, resin bonded sand casting does have some challenges. The handling and disposal of resin materials require careful management, as many resins can be hazardous to health and the environment. Proper ventilation and personal protective equipment are essential when working with these materials to ensure safety in the workplace. Furthermore, the cost of resin materials can exceed that of traditional sand molding processes, which may deter some manufacturers from adopting this technology.
In terms of process execution, the resin bonded sand casting begins with the preparation of sand and resin mixture, which is typically achieved by mechanically mixing green sand with the binder and an appropriate catalyst. The next step involves creating a mold by compacting the sand mixture around a pattern. Once the mold is formed and cured, the pattern is removed, and the mold is ready for metal pouring. After the metal has cooled and solidified, the mold is broken apart to reveal the cast component.
In conclusion, resin bonded sand casting represents a significant evolution in the metal casting industry. Its capability to produce complex shapes and high-quality castings efficiently makes it an excellent choice for manufacturers looking for precision and reliability. As technology continues to advance and the demand for sustainable practices grows, resin bonded sand casting will likely play an increasingly prominent role in future manufacturing processes, reflecting the industry's adaptability to both challenges and opportunities.
Post time:Aug . 20, 2024 21:33
Next:Characteristics and Applications of Foundry Sand in Metal Casting Processes