Understanding the Properties of Foundry Sand
Foundry sand is a crucial component in the metal casting process, serving as a mold material for shaping molten metals into desired forms. Its unique properties significantly contribute to the quality and precision of castings. This article delves into the key properties of foundry sand, which not only enhance the casting process but also affect the final product's performance.
One of the primary properties of foundry sand is its grain shape. Foundry sand typically has a spherical or sub-angular particle shape, which facilitates excellent flowability and packing density. This characteristic is essential as it allows the sand to form molds that are precise and able to withstand the weight of molten metal without collapsing. The ability to create a uniform mold is crucial for achieving a high-quality casting.
Another significant property is the sand's particle size distribution. A well-graded particle size distribution improves the packing efficiency of the sand, which minimizes gaps between particles that can lead to defects in the casting. The ideal foundry sand should have a mix of fine and coarse particles; this combination enhances mold strength and stability while allowing gases to escape during the pouring of molten metal. Fine particles fill the voids between coarser grains, creating a denser mold that can handle thermal expansion without resulting in cracks or deformities.
Additionally, the purity of foundry sand is a vital aspect that affects its performance. Contaminants such as clay, silt, or organic matter can degrade the properties of foundry sand. Properly processed foundry sand should contain minimal impurities to ensure optimal binding and strength. High purity levels contribute to better surface finishes and reduce the likelihood of casting defects such as sand inclusions and poor surface quality.
properties of foundry sand
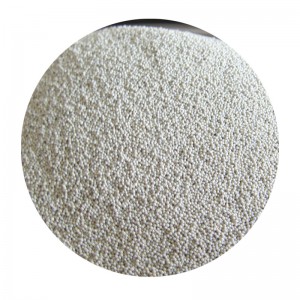
The thermal conductivity of foundry sand is also an important property. Sand with high thermal conductivity ensures that heat is effectively dissipated away from the molten metal, which helps in controlling the cooling rate and achieving uniform solidification. This property is critical for avoiding issues like hot tears and improving the overall integrity of the casting. Conversely, sand with low thermal conductivity may result in uneven cooling, leading to distortion and weakened areas in the final product.
Moisture content is another factor that plays a critical role in the performance of foundry sand. The water present in the sand affects its cohesiveness and ability to form a strong mold. However, too much moisture can lead to steam pockets and defects during the metal pouring process. Therefore, maintaining the ideal moisture level is crucial for achieving optimal mold strength and dimensional accuracy.
Lastly, the recyclability of foundry sand is gaining increasing attention in the industry. With growing environmental concerns, many foundries are seeking ways to minimize waste and promote sustainability. Used foundry sand can often be reclaimed and recycled for repeated use in the casting process, provided it is adequately treated to restore its properties. This not only reduces the demand for new sand but also lowers the operational costs associated with disposal.
In conclusion, the properties of foundry sand— including grain shape, particle size distribution, purity, thermal conductivity, moisture content, and recyclability — are fundamental to the metal casting process. Understanding and optimizing these properties allows foundries to produce high-quality castings that meet precise specifications while also addressing environmental sustainability goals. As foundry practices continue to evolve, the emphasis on the characteristics of foundry sand will remain paramount for innovation and efficiency in metal casting.
Post time:Aug . 20, 2024 20:49
Next:Innovative Ceramic Beads for Enhanced Performance in Various Applications