The Importance of Sand Casting and Key Suppliers in the Industry
Sand casting is one of the oldest and most versatile manufacturing processes used to create metal parts and components. This method involves creating a mold from a mixture of sand and a binding agent, which is then filled with molten metal to shape the desired object. Its simplicity, cost-effectiveness, and ability to produce complex geometries make sand casting an extremely popular choice in various industries, including automotive, aerospace, and manufacturing.
Understanding Sand Casting
The sand casting process begins with the preparation of the mold. Typically, fine sand is mixed with a binder, which helps the sand retain its shape when compressed. The mixture is then packed around a pattern that outlines the shape of the final product. Once the mold is formed, it is carefully removed, and the pattern is extracted, leaving a cavity that will be filled with molten metal. After the metal has cooled and solidified, the sand is broken away to reveal the final casting.
One of the key advantages of sand casting is its adaptability. It can accommodate a wide range of metals, including aluminum, bronze, iron, and steel. Furthermore, the process allows for the production of large parts or intricate designs that may be challenging to achieve with other manufacturing methods, such as die casting or forging.
The Role of Suppliers in Sand Casting
The effectiveness of sand casting is greatly influenced by the suppliers of the materials and equipment involved in the process. High-quality sand, binders, and additives are critical for producing durable and accurate castings. Moreover, equipment such as molds, pouring systems, and cooling devices must be reliable and efficient to meet production demands.
Key suppliers in the sand casting industry include those providing
1. Foundry Sand Fine-grade silica sand is the most commonly used material in sand casting. Suppliers who specialize in providing consistent quality and granularity are essential for ensuring mold integrity and surface finish.
sand casting suppliers
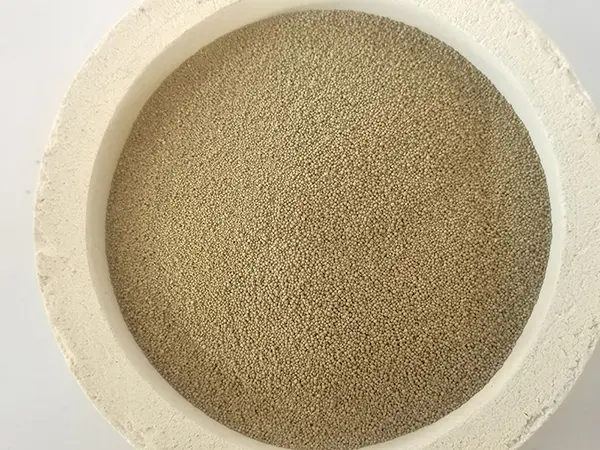
2. Binders and Additives Various chemical binders are used to enhance the properties of the sand mold, including resin and clay options. Suppliers focused on these materials contribute to the effectiveness of the mold by improving its strength and thermal stability.
3. Metal Suppliers The choice of metal is crucial depending on the application's requirements. Suppliers who provide a range of alloys and specialty metals ensure that manufacturers can select the best materials for their specific casting needs.
4. Casting Equipment Suppliers Companies that manufacture and supply casting equipment, such as furnaces for melting metal and molds for shaping, play an essential role in the efficiency of the sand casting process. Their technology can determine the speed and quality of production.
Finding Reliable Sand Casting Suppliers
When looking for sand casting suppliers, businesses should consider several factors to ensure they partner with reliable sources. These include
- Experience and Industry Reputation Suppliers with extensive experience and positive customer reviews are more likely to provide high-quality products and services. - Quality Certifications Suppliers that adhere to quality certifications, such as ISO, demonstrate their commitment to maintaining strict manufacturing standards. - Technical Support A supplier offering technical service can help manufacturers troubleshoot issues and optimize their casting processes. - Customization Capabilities The ability to customize materials and solutions is beneficial, particularly when dealing with unique projects requiring specific specifications.
Conclusion
As industries increasingly turn to sand casting for its versatility and cost-effectiveness, the importance of selecting the right suppliers becomes evident. With advancements in technology and materials, collaborating with reputable sand casting suppliers can lead to better product quality, reduced production costs, and enhanced efficiency. By understanding the dynamics of this process and the role of suppliers, manufacturers can effectively harness the potential of sand casting to meet their production needs and thrive in a competitive landscape.
Post time:Aug . 17, 2024 07:10
Next:Exploring Various Types of Foundry Sand for Improved Casting Results