Different Types of Foundry Sand
Foundry sand plays a crucial role in the metal casting process, acting as a mold material that shapes molten metal into various products. The choice of sand affects the quality, finish, and overall performance of the final casting. There are several types of foundry sand, each with unique properties, advantages, and applications. In this article, we will explore the most common types of foundry sand used in the industry.
1. Silica Sand
Silica sand is one of the most widely used types of foundry sand due to its excellent casting properties. It is composed primarily of silicon dioxide (SiO2) and is characterized by its high temperature resistance and durability. Silica sand is ideal for producing molds and cores in ferrous and non-ferrous casting processes. Its uniform grain size helps in achieving fine surface finishes and precise dimensional accuracy. However, excessive inhalation of silica dust can pose health hazards, leading to regulatory measures in its usage.
2. Olivine Sand
Olivine sand, also known as peridotite sand, is composed of magnesium iron silicate and is renowned for its high fusion point and thermal stability. It is less reactive than silica sand and exhibits superior resistance to thermal shock. Olivine sand is particularly favored in casting steel and iron, as it helps in reducing defects like sand burn-on and veining. Furthermore, olivine sand is characterized by its greenish color, which can be beneficial for identifying mold failures.
different types of foundry sand
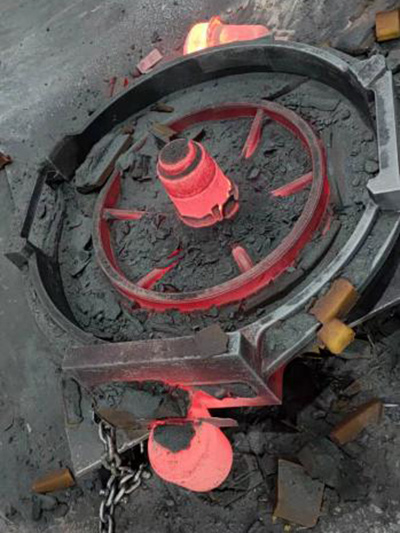
Chromite sand is derived from chromite ore and is used primarily in high-performance applications. It boasts high thermal conductivity and excellent resistance to thermal shock, making it suitable for high-temperature casting processes, such as stainless steel. The use of chromite sand can enhance the surface finish and dimensional accuracy of castings. Due to its cost and availability, chromite sand is often utilized in specialty applications rather than for general-purpose casting.
4. Green Sand
Green sand refers to a mixture of sand, clay, moisture, and other additives. It is named green because it contains moisture when used, allowing it to maintain its shape. The clay content binds the sand grains together, providing strength and elasticity to the mold. Green sand is commonly used in the iron and aluminum casting industries due to its ability to produce intricate shapes and fine surface finishes. Its reusability and cost-effectiveness make it a popular choice among foundries.
5. Resin-Coated Sand
Resin-coated sand is a modern alternative to traditional sand systems. This type of sand is coated with a thermosetting resin that enhances its binding properties. The use of resin-coated sand allows for precise core and mold designs with high dimensional accuracy. It also provides excellent surface finishes and reduces sand sticking to the castings. Typically, resin-coated sand is used in applications requiring intricate details and high-quality finishes, such as aerospace and automotive components.
Conclusion
The choice of foundry sand significantly influences the quality of castings produced. Each type of foundry sand offers distinct advantages, making it essential for foundries to select the appropriate material based on their specific casting requirements. Understanding the characteristics and applications of different types of foundry sand can lead to improved efficiency and product quality in the casting industry. As technology evolves, new materials and processes will likely emerge, further enhancing the capabilities of foundry sands and their applications in various industries.
Post time:Aug . 17, 2024 06:34
Next:Exploring the Synergy of Sand and Resin in Innovative Applications