Sanding a 3D Print Achieving the Perfect Finish
3D printing is an incredible technology that allows creators, hobbyists, and professionals to turn digital designs into tangible objects. However, one challenge many faces is achieving a smooth, polished finish on their printed models. While 3D printers can produce complex shapes with remarkable precision, the surface quality of the printed items often leaves much to be desired. Luckily, sanding is a practical solution to this common issue. In this article, we will discuss the importance of sanding a 3D print, the materials and tools needed, and step-by-step instructions to help you achieve that perfect finish.
Why Sanding Matters
Sanding serves multiple purposes when it comes to 3D prints. First and foremost, it helps eliminate the visible layer lines that are characteristic of most 3D printed objects, especially those produced using Fused Deposition Modeling (FDM) printers. These layer lines can detract from the overall aesthetic, particularly for models intended for display or professional use. Secondly, sanding provides a better surface for painting and finishing. A smooth surface allows for more even application of paint, resulting in a more professional appearance. Lastly, sanding can help improve the fit of parts in assemblies by ensuring a better mating surface.
Tools and Materials Needed
Before you start sanding, it's essential to gather the right tools and materials. Here’s a checklist to get you started
1. Sandpaper Use a range of grits, typically from coarse (around 80-120 grit) to fine (up to 1000 grit). The initial sanding uses coarse paper to remove large imperfections, while fine paper is for finishing. 2. Sanding Sponge or Block For larger surfaces, a sanding sponge or block can help provide an even pressure distribution and reduce the risk of creating uneven spots.
3. Dust Mask To protect yourself from inhaling fine dust particles.
4. Safety Glasses It’s always a good practice to protect your eyes when sanding.
5. Water or Lubricant Wet sanding is highly effective for reducing dust and minimizing scratches, especially on softer materials like PLA (Polylactic Acid).
sanding a 3d print
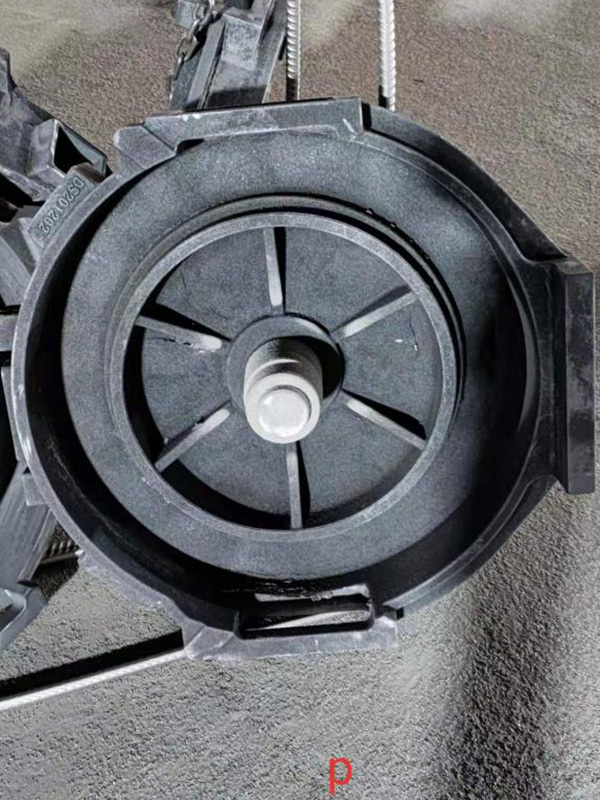
Step-by-Step Sanding Process
1. Preparation Start by ensuring your workspace is clean and well-ventilated. Wear your dust mask and safety glasses before handling your print.
2. Initial Sanding Using coarse sandpaper (80-120 grit), gently sand the surface of the print. Apply even pressure and move in circular or back-and-forth motions. Focus on the areas with the most pronounced layer lines or imperfections.
3. Examine the Print After the first round of sanding, inspect your print closely. You should notice a significant reduction in layer lines. Depending on the print's material, you may want to wet sand, which can reduce dust and provide a finer finish. If needed, switch to a finer grit sandpaper (around 220 grit) and repeat the sanding process.
4. Fine Sanding Gradually move to finer grits (320 to 1000 grit). This step is crucial for achieving a smooth surface. As you sand, you may want to switch to a sanding block or sponge for better control.
5. Clean the Surface After sanding, make sure to clean off any dust using a brush or cloth. If you are planning to paint your print, consider rinsing it with water to ensure that no dust remains.
6. Final Touches Once the print is clean and dry, you can decide whether to apply a primer, paint, or a finish. The smoother the surface after sanding, the better the final paint job will look.
Conclusion
Sanding a 3D print may seem like an arduous task, but the rewards are well worth the effort. With the right techniques and tools, you can transform a rough model into a beautifully finished piece. Whether you’re preparing a prototype for a presentation or crafting a display-worthy item, proper sanding will elevate your 3D printing game to new heights. So, don’t overlook the importance of this step; embrace it and enjoy the satisfaction of a job well done!
Post time:Aug . 13, 2024 06:22
Next:Understanding the Role of Facing Sand in Foundry Processes and Its Impact on Casting Quality