Advantages and Disadvantages of Sand Casting Process
Sand casting is one of the oldest and most versatile metal casting processes used in manufacturing industries today. It involves the use of sand as the primary mold material for shaping molten metal into desired forms. While sand casting offers numerous advantages, it also comes with certain drawbacks that manufacturers must consider before opting for this method.
Advantages of Sand Casting
1. Cost-Effectiveness One of the most significant advantages of sand casting is its low cost. The materials used in sand casting, such as sand, clay, and water, are inexpensive and readily available. This makes the process suitable for both small-scale and large-scale production.
2. Versatility Sand casting can accommodate a wide variety of metals, including aluminum, iron, and bronze. This versatility allows manufacturers to produce a broad range of products, from simple components to complex shapes, making it an ideal choice for many applications.
3. Large Size Capabilities Sand casting can produce large components that are often difficult to mold using other techniques. This capability is especially useful in industries such as automotive and aerospace, where large, heavy parts are commonplace.
4. Complex Geometries The sand casting process allows for the creation of intricate designs that would be challenging to produce through other methods. This ability to form complex geometries with fine details expands the possibilities for product design.
5. Ease of Modification Modifying a sand casting mold is relatively straightforward. If adjustments are needed, manufacturers can easily alter the sand mold without incurring significant costs. This flexibility in design is particularly beneficial during the prototyping phase.
6. Scalability Sand casting is adaptable for both short and long production runs. Whether a manufacturer requires a few hundred pieces or several thousand, the process can be scaled accordingly, making it an attractive option for various production needs.
advantages and disadvantages of sand casting process
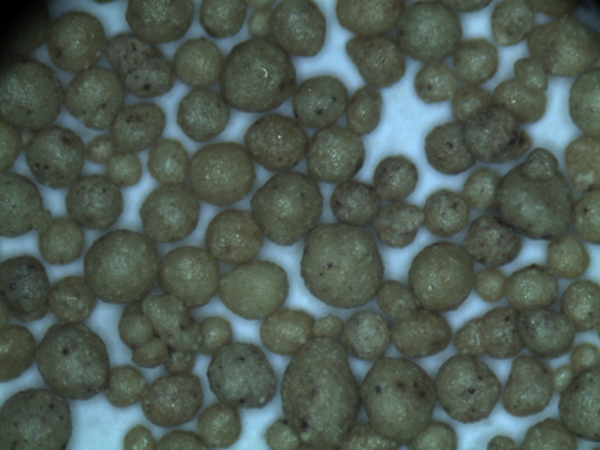
Disadvantages of Sand Casting
1. Surface Finish and Tolerances One of the main drawbacks of sand casting is the finish quality of the cast parts. The surface roughness is generally higher compared to other casting methods like die casting. Achieving tight tolerances can also be challenging, necessitating additional machining for certain applications, which can increase overall production costs.
2. Labor-Intensive Sand casting can be a labor-intensive process, particularly in terms of mold-making and handling. Skilled labor may be required to ensure that molds are properly formed and that casting processes are executed smoothly, which could lead to higher operational costs.
3. Dimensional Accuracy Due to the inherent nature of sand as a mold material, castings produced via sand casting may suffer from dimensional inaccuracies. This can lead to variations in the final product, impacting overall quality and performance.
4. Environmental Concerns The sand casting process can generate considerable waste, including used sand and other materials. Additionally, the emissions from molten metal can pose environmental risks if not managed properly. Manufacturers need to implement effective waste management and recycling strategies to mitigate these concerns.
5. Cycle Time Sand casting typically has a longer cycle time compared to some modern casting methods. The time required for the sand to set and cool can extend the overall production process, which may not be ideal for projects requiring rapid turnaround times.
Conclusion
In summary, sand casting is a time-tested manufacturing process with distinct advantages and disadvantages. Its cost-effectiveness, versatility, and ability to produce complex shapes make it a popular choice in various industries. However, issues related to surface finish, dimensional accuracy, and environmental impact may pose challenges that need to be navigated. When deciding whether to utilize sand casting, manufacturers must weigh these pros and cons to determine if it aligns with their production goals and quality standards.
Post time:Aug . 20, 2024 16:14
Next:Various Sand Types Used in Foundry Applications for Casting Processes