Types of Sand in Foundry Casting
The foundry industry is a cornerstone of manufacturing, responsible for producing metal castings through various processes including sand casting. Among the various materials used in foundry processes, sand is the most significant. Its properties and characteristics determine the quality and precision of the final castings. In this article, we will explore the different types of sand used in foundries, highlighting their unique attributes and applications.
1. Silica Sand
Silica sand is the most commonly used type of sand in the foundry industry. It consists primarily of silicon dioxide (SiO2) and is appreciated for its high melting point, durability, and excellent thermal properties. Silica sand is ideal for molding because it can withstand high temperatures without breaking down. It is often used in the creation of sand molds that are essential for shaping molten metal. By adding binders to silica sand, foundries can enhance its strength and cohesion, making it suitable for intricate designs. Furthermore, the roundness and grain size of silica sand play a pivotal role in determining the quality of the mold, influencing the surface finish and dimensional accuracy of the final casting.
2. Green Sand
Green sand is a mixture of silica sand, clay, water, and other additives. This type of sand gets its name from the moisture it retains, which gives it a green appearance. Green sand is widely used in foundry operations due to its excellent molding and casting properties. The clay in green sand acts as a binder, giving it the ability to retain shape and provide high strength. It is especially useful in producing complex shapes and details. When heated, the moisture evaporates, allowing the sand to harden, thus securing the integrity of the mold. Green sand is favored for its cost-effectiveness and reusability, often being recycled multiple times in the foundry process.
types of sand in foundry
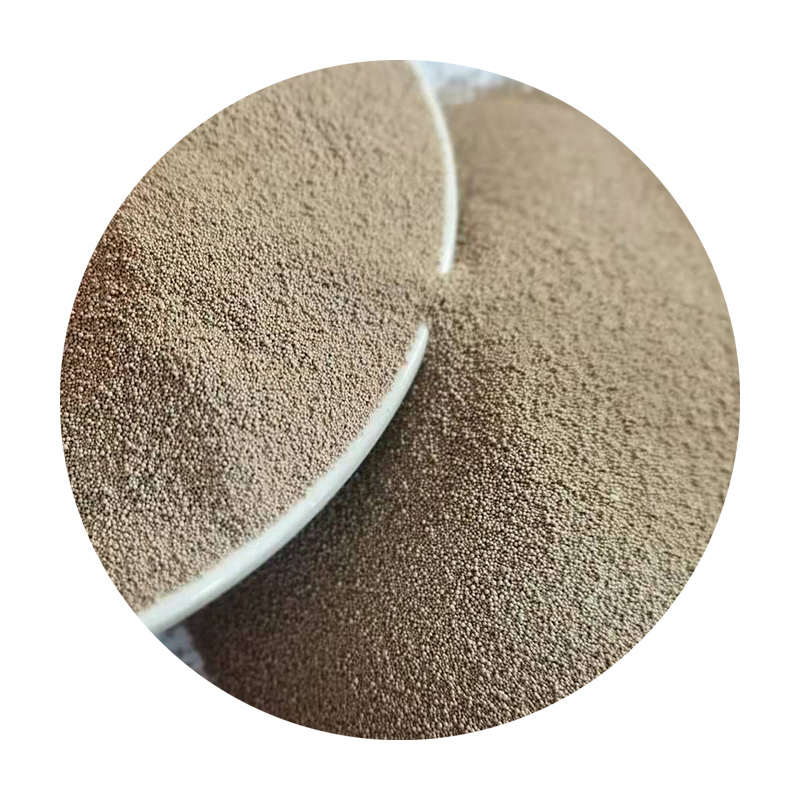
3. Resin-Bonded Sand
Resin-bonded sand employs synthetic resins as a binder instead of traditional clay. This type of sand offers several advantages, including improved strength and dimensional accuracy. Resin-bonded sand can be designed to cure at room temperature or through heat application, allowing for flexibility in the casting process. One of the key benefits of this sand type is its ability to form molds with finer contours and smoother finishes, making it ideal for high-precision components in industries like automotive and aerospace. While it tends to be more expensive than green sand, its performance characteristics often justify the investment.
4. Investment Casting Sand
Investment casting sand, also known as lost-wax casting, utilizes a fine-grained silica or zircon sand mixed with a binder. This method is notable for producing highly detailed and intricate parts with a superior surface finish. The sand is used to create molds that can capture fine details, which is crucial for intricate designs. The molds are often coated with a thin layer of investment material, leading to reduced post-casting finishing work. With investment casting, the incorporated sands can withstand the high temperatures of molten metal, ensuring minimal distortion during the casting process.
Conclusion
The choice of sand in foundry casting plays a pivotal role in determining the quality of the final product. Silica sand, green sand, resin-bonded sand, and investment casting sand each possess distinct properties that cater to various casting needs. Understanding the characteristics of these sands allows foundries to optimize their processes, enhance the quality of their castings, and reduce production costs. As the foundry industry continues to evolve, ongoing research and development will likely lead to innovations in sand types and their applications, further improving casting techniques and final product quality.
Post time:Aug . 20, 2024 15:48
Next:د ۳D چاپونو لپاره د لندبل ریت کولو څرنګوالی