Sand Cast Metal An Overview of the Process and Applications
Sand casting, also known as sand mold casting, is one of the oldest and most widely used metal casting processes. It involves the use of sand as the primary mold material to create complex metal objects and parts. The flexibility, cost-effectiveness, and ease of creating molds in various shapes make sand casting a favored choice across various industries, including automotive, aerospace, and art.
The Process of Sand Casting
The sand casting process begins with preparing a sand mold, which consists of a mixture of sand, clay, and water that creates a pliable yet sturdy mold capable of capturing fine details. Typically, silica sand is utilized due to its high melting point and ability to withstand the thermal stresses of molten metal. The process can be broken down into several key steps
1. Pattern Making A pattern, usually made from wood, metal, or plastic, is created to form the shape of the final product. The pattern is slightly larger than the desired finished piece to account for the shrinkage that occurs during cooling.
2. Mold Preparation The pattern is placed in a box, known as a flask, and sand is packed around it, creating a mold cavity. After removing the pattern, the two halves of the mold are assembled, with channels known as gates incorporated into the design to allow molten metal to flow in.
3. Melting and Pouring Once the mold is prepared, metal is melted in a furnace. Common metals used in sand casting include aluminum, brass, and cast iron. After reaching the correct melting temperature, the molten metal is poured into the mold through the gates.
4. Cooling The molten metal is allowed to cool and solidify. This cooling period can vary based on the specific metal used and the size of the casting.
5. Mold Removal and Finishing After the metal has cooled, the mold is broken away, revealing the cast metal object. Finishing processes, such as sanding, grinding, or machining, may be conducted to achieve the desired surface finish and accuracy.
sand cast metal
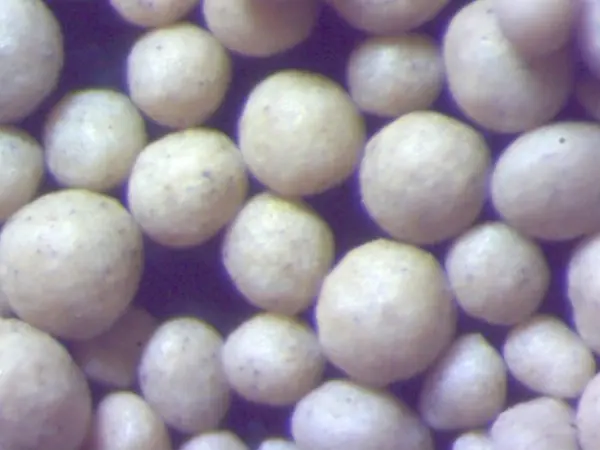
Advantages of Sand Casting
Sand casting offers numerous advantages that contribute to its widespread use. One of the most significant benefits is its versatility; it can accommodate a wide range of metal alloys and allows for the creation of complex geometries. Additionally, the materials used for sand molds are relatively inexpensive, making the process cost-effective, especially for low-to-medium production runs.
Another compelling advantage is the ability to produce large castings. Many industries rely on sand casting to create heavy components, such as engine blocks and structural parts for machinery. The process also facilitates changes in design without extensive costs, making it an excellent option for prototypes and custom parts.
Applications of Sand Casting
Sand casting finds application in various industries. The automotive sector frequently utilizes sand casting for engine parts, transmission cases, and other structural components. The aerospace industry also employs this technique to produce complex and lightweight components, optimizing performance while reducing weight.
Additionally, sand casting is prevalent in the creation of artistic sculptures and decorative pieces, allowing artists to bring their visions to life with intricate detail. The adaptability and functionality of sand casting make it a vital process in modern manufacturing.
Conclusion
In conclusion, sand casting stands as a cornerstone in the field of metallurgy and manufacturing. With its rich history and continued relevance, the process showcases a perfect blend of tradition and technology. Its advantages in terms of cost, versatility, and capability to produce complex shapes ensure that sand casting will remain an integral part of metalworking for years to come. As industries continue to innovate, sand casting will evolve alongside them, proving its timelessness in the world of metal production.
Post time:Aug . 07, 2024 12:05
Next:The Evolution and Significance of Sand Casting Techniques Throughout History