Lost Foam Casting An Innovative Approach in Metal Foundry
Lost foam casting (LFC) is an advanced and efficient metal casting process that has garnered attention in recent years for its precision and cost-effectiveness. This method, which involves the use of expendable foam patterns, is particularly valued in industries where complicated shapes and high-quality finishes are essential. Its practical applications range from automotive and aerospace components to artistic sculptures and industrial fittings.
The lost foam casting process begins with creating a pattern made from a polymer foam, typically polystyrene. This pattern is shaped according to the desired final product, encompassing all the details and intricacies needed in the final cast. The foam pattern is then coated with a ceramic material to provide a shell that can withstand the extreme temperatures encountered during metal pouring. Once the shell is set, the foam pattern is placed in a mold box, and molten metal is poured directly into the cavity.
One of the primary advantages of lost foam casting is its ability to produce complex geometries that would be difficult or impossible to achieve with traditional methods such as sand casting or die casting. The foam pattern vaporizes upon contact with the molten metal, filling the space and creating a near-net-shape product. This process minimizes the need for secondary machining and finishing processes, thereby reducing production time and material waste.
lost foam casting
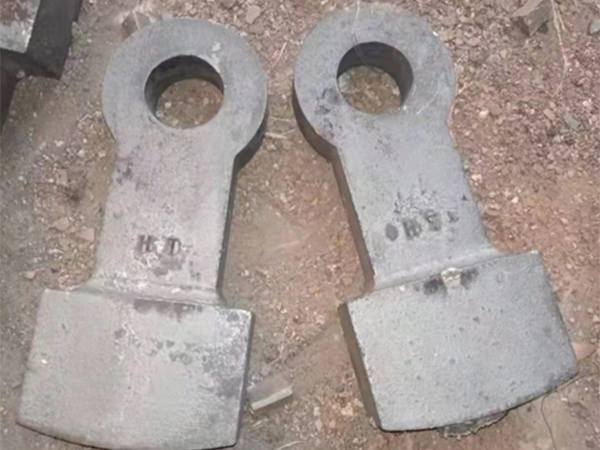
Moreover, lost foam casting is extremely versatile. It can be used to cast a variety of metals, including aluminum, iron, and steel. This flexibility makes it ideal for industries requiring different materials for their components. Additionally, the ability to reproduce detailed textures and intricate designs makes lost foam casting a popular choice for artistic applications, such as sculptures and custom decorative pieces.
From an economic perspective, lost foam casting presents several benefits. It allows for lower production costs due to reduced material waste and labor savings associated with fewer machining processes. The efficiency of this method can lead to shorter lead times, helping manufacturers meet tight deadlines and adapt to market demands swiftly. Furthermore, the compatibility of lost foam casting with automation and advanced manufacturing technologies enhances its allure in modern production environments.
Despite its numerous advantages, lost foam casting also faces challenges that potential users should consider. The initial investment in equipment and the development of accurate foam patterns can be significant. Additionally, the process requires a careful balance of parameters, including the temperature of the molten metal and the curing time of the ceramic shell, to achieve optimal results. Manufacturers must possess technical expertise to troubleshoot any issues that may arise during the casting process.
In conclusion, lost foam casting is an innovative casting technique that offers numerous advantages in terms of precision, cost-effectiveness, and versatility. As industries continue to seek efficient manufacturing methods, LFC stands out as a compelling option for producing high-quality components. With advancements in materials and technology, the future of lost foam casting looks promising, suggesting that this process will play an increasingly vital role in modern manufacturing landscapes. As designers and engineers continue to push the limits of technology, lost foam casting will likely evolve, opening new avenues for creativity and innovation in metal casting.
Post time:Aug . 14, 2024 19:02
Next:Exploring the Benefits and Applications of Custom Sand Casting in Modern Manufacturing Techniques