Custom Sand Casting A Versatile Manufacturing Process
Custom sand casting is a well-established manufacturing process that has been utilized for centuries in various industries. This technique involves pouring molten metal into sand molds to create complex shapes and components, making it an ideal solution for businesses seeking tailored parts for their products. This article will explore the intricacies of custom sand casting, including its advantages, applications, and the process involved.
The Sand Casting Process
The sand casting process begins with the creation of a mold, typically made from fine sand mixed with a binding agent, such as clay or resin. The sand mold is shaped to form a cavity that reflects the desired geometry of the final product. One of the significant benefits of sand casting is its ability to accommodate intricate designs, which would be challenging to achieve with other manufacturing methods.
Once the mold is prepared, the next step is to melt the metal that will be cast. Common materials used in sand casting include aluminum, brass, bronze, and iron. The choice of metal often depends on the specific requirements of the application, such as strength, weight, and corrosion resistance. Once the metal reaches the appropriate temperature, it is poured into the mold cavity. After the metal has cooled and solidified, the sand mold is broken away, revealing the finished component.
Advantages of Custom Sand Casting
One of the primary advantages of custom sand casting is its versatility. The process allows for the production of both simple and complex parts in a wide range of sizes, making it suitable for various industries, including automotive, aerospace, and construction. Additionally, sand casting can be used to create both small-scale prototypes and large production runs, providing flexibility for manufacturers.
custom sand casting
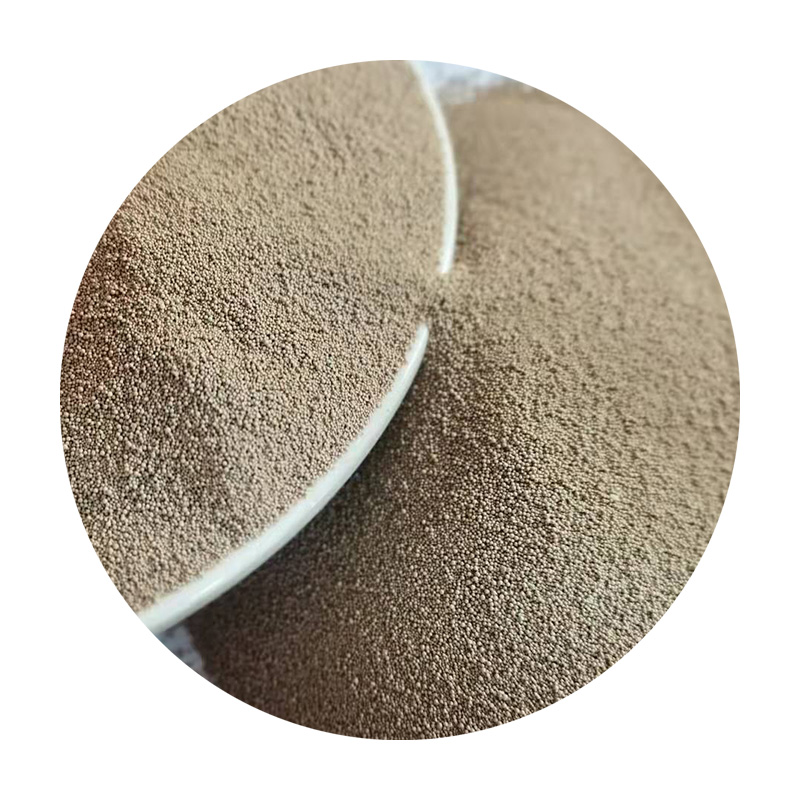
Another notable advantage is the cost-effectiveness of sand casting. The materials involved, particularly sand, are relatively inexpensive compared to other molding materials. Furthermore, the process requires minimal tooling, which can significantly reduce initial setup costs. This makes custom sand casting an attractive option for companies looking to produce parts without incurring substantial financial risks.
Custom sand casting also offers excellent mechanical properties in the final products. Cast components often exhibit good strength, hardness, and wear resistance, which are crucial for many industrial applications. The ability to precisely control the cooling rate during the process can further enhance the material properties of the finished product.
Applications of Custom Sand Casting
The applications of custom sand casting are vast and varied. In the automotive industry, sand casting is commonly used to produce engine blocks, cylinder heads, and various other components that require durability and precision. The aerospace sector also benefits from this process, as it allows for the creation of lightweight yet strong components that are essential for aircraft performance.
Moreover, custom sand casting plays a significant role in the manufacturing of machinery and industrial equipment. Various parts, such as housings, brackets, and fittings, are often produced using this method due to the high levels of customization it offers. Even art and sculpture industries utilize sand casting techniques to create intricate designs and forms.
Conclusion
In summary, custom sand casting is a versatile and cost-effective manufacturing process that continues to play a crucial role across many industries. Its ability to produce complex shapes from a variety of metals makes it an ideal choice for businesses seeking tailored solutions. As technology advances, the methods and materials used in sand casting are expected to evolve, further enhancing its capabilities and applications. Whether for prototyping or large-scale production, custom sand casting remains a go-to choice for many manufacturers worldwide.
Post time:Aug . 14, 2024 18:44
Next:Comprehensive Sand Casting Solutions for Custom Metal Parts and Quality Manufacturing Services