The Lost Foam Casting Method An Innovative Approach to Metal Fabrication
Lost foam casting is an advanced metal casting technique that has gained popularity in recent years due to its ability to produce intricate shapes with exceptional surface finishes. This method, which builds upon the principles of traditional casting, employs a foam pattern that is vaporized during the casting process. This article will explore the principles of lost foam casting, its advantages, applications, and future prospects in the metalworking industry.
Principles of Lost Foam Casting
The lost foam casting method begins with the production of a foam pattern, typically made from polystyrene. This pattern is created using an expanded polystyrene (EPS) foam, which is highly customizable and can be manufactured to match the desired dimensions and intricate details of the final product. Once the foam pattern is made, it is coated with a sand mixture, often combined with bonding agents, to form a mold.
The key characteristic of lost foam casting is the elimination of the need for a traditional mold. Instead of using a rigid mold, the foam pattern is placed directly into the sand, where it is surrounded and coated by the sand mixture. After this preparation, molten metal is poured into the mold. As the molten metal fills the cavity formed by the foam pattern, it simultaneously vaporizes and displaces the foam. This leads to the formation of a metal component that accurately reflects the geometry of the original foam pattern.
Advantages of Lost Foam Casting
One of the most significant advantages of lost foam casting is its ability to produce complex shapes with minimal machining requirements. Since the foam pattern can be designed with intricate details, the final metal part often requires little to no further processing. This reduces manufacturing time and costs, making lost foam casting an attractive option for industries seeking efficiency.
Additionally, lost foam casting can accommodate a variety of metals, including aluminum, iron, and zinc, making it versatile for different applications. The method also yields components with improved surface finishes and uniform density, enhancing the overall quality of the product.
lost foam casting method
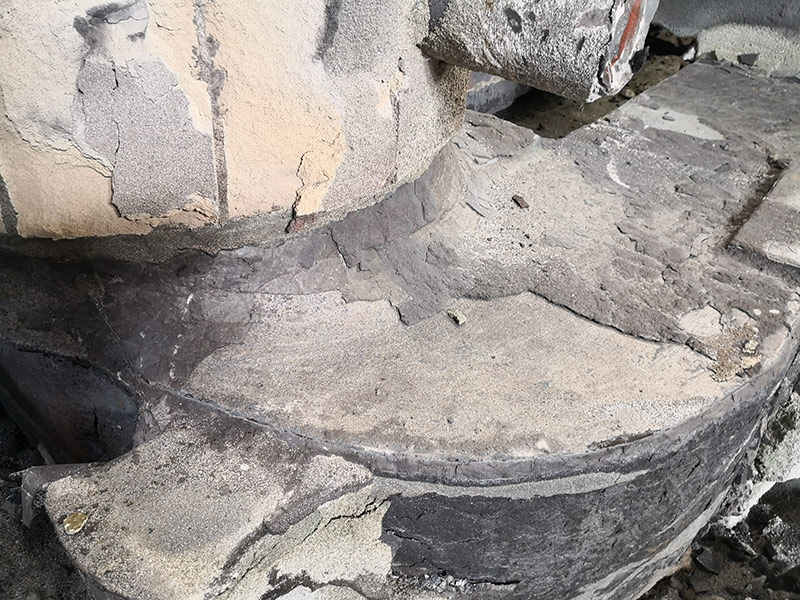
Another notable benefit is the minimal waste produced during the process. Traditional casting methods often result in excess material that must be machined away, contributing to waste and increased production costs. In contrast, because the foam pattern is fully consumed during the casting process, there is no excess material, making lost foam casting a more sustainable option.
Applications of Lost Foam Casting
Lost foam casting is utilized across various industries due to its versatility and efficiency. It's particularly prominent in the automotive and aerospace sectors, where lightweight and intricate components are essential. Manufacturers use this method to produce engine blocks, brackets, and other complex shapes that must meet stringent performance standards.
The method is also gaining traction in the manufacturing of custom products and smaller batch productions, allowing companies to offer tailored solutions without incurring high setup costs. Additionally, the energy-efficient nature of lost foam casting makes it a suitable choice for businesses looking to minimize their carbon footprint.
Future Prospects
As technology continues to advance, the lost foam casting method is expected to evolve further. Innovations in materials, including the potential use of biodegradable foams, could enhance the sustainability of the process. Moreover, the integration of computer-aided design (CAD) and computer numerical control (CNC) machining with lost foam casting will likely facilitate even more complex geometries and improve precision.
In conclusion, lost foam casting represents a significant evolution in metal fabrication techniques. With its inherent advantages in efficiency, complexity, and sustainability, this method is poised to play a crucial role in the future of manufacturing, catering to the growing demand for innovative, lightweight, and high-quality metal components across various industries.
Post time:Aug . 21, 2024 21:39
Next:Innovative Applications of Lost Foam Casting in Modern Manufacturing Techniques