Lost Foam Casting A Versatile Method for Precision Manufacturing
Lost foam casting (LFC) is an innovative metal casting process that has gained significant attention in recent years due to its precision and versatility. This method, which involves creating a foam pattern that is subsequently coated with a refractory material and then filled with molten metal, has opened new avenues in various manufacturing sectors, including automotive, aerospace, and industrial machinery.
Lost Foam Casting A Versatile Method for Precision Manufacturing
One of the primary advantages of lost foam casting is its ability to produce intricate shapes with excellent surface finishes. Traditional sand casting methods often require additional machining to achieve desired tolerances and finishes, while lost foam casting minimizes these secondary operations. The smooth finish and fine details achievable with LFC are particularly beneficial in industries where precision is paramount, such as in the production of engine components and turbine blades.
lost foam casting examples
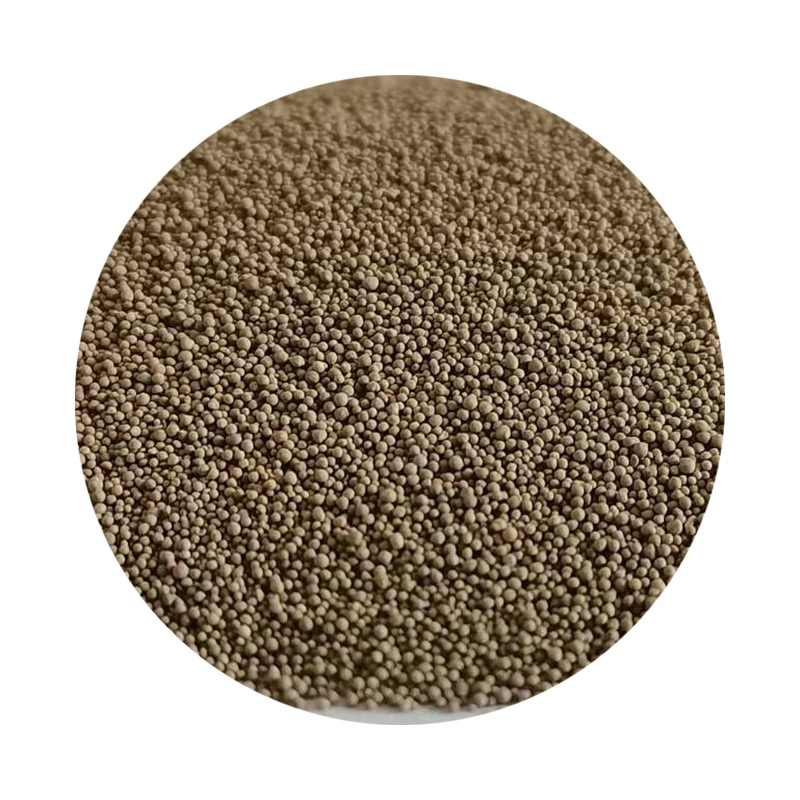
Moreover, LFC allows for the incorporation of complex internal features that would be difficult or impossible to achieve with conventional casting methods. For instance, cooling channels within a part can be integrated seamlessly into the design, optimizing thermal performance in applications like HVAC systems and electric motors. This capability not only enhances performance but also reduces the weight of components, which is a crucial factor in aerospace and automotive applications where fuel efficiency and payload capacity are critical.
Environmental considerations have also driven the adoption of lost foam casting. The process generates minimal waste, as the foam patterns can be produced from recyclable materials. Additionally, the reduction in machining requirements means less material is lost during production, contributing to a more sustainable manufacturing cycle. As industries worldwide strive to improve their environmental impact, LFC presents an appealing option for creating complex components with reduced material consumption.
Despite its numerous advantages, lost foam casting is not without challenges. The process requires precise control of parameters such as temperature and pouring speed to ensure a successful pour and minimize defects like porosity or misalignment. However, advancements in technology and process monitoring have significantly improved the consistency and reliability of LFC, making it a viable alternative to traditional methods for many applications.
In conclusion, lost foam casting offers a unique combination of precision, complexity, and sustainability, positioning itself as a crucial technology in modern manufacturing. With continued development and innovation, this casting process is poised to expand its impact across various industries, enabling the production of high-performance components that meet the evolving demands of design and functionality. As manufacturers increasingly seek efficient and environmentally friendly solutions, the role of lost foam casting will likely become even more prominent in the years to come.
Post time:Aug . 21, 2024 20:42
Next:Applications and Benefits of Ceramsite Foundry Sand in Industrial Processes