The Role of Ceramic Foundry Sand in Modern Casting Processes
Ceramic foundry sand, a high-performance alternative to traditional sands used in the casting industry, has gained traction in recent years due to its numerous advantages. This specialized material is primarily composed of fine-grained, manufactured ceramic materials that enhance the casting process, improve product quality, and reduce environmental impacts. As industries evolve and demand for precision and sustainability increases, ceramic foundry sand is becoming a vital component in manufacturing practices.
One of the most significant advantages of ceramic foundry sand is its excellent thermal properties. Ceramic materials have high thermal stability and can withstand extreme temperatures, making them ideal for the casting of metals. Unlike traditional silica sand, which can undergo thermal expansion and result in defects, ceramic foundry sand maintains its integrity under heat. This stability minimizes casting defects such as warping and cracking, leading to higher quality end products with fewer rework requirements.
Additionally, ceramic foundry sand offers superior strength and durability
. Its hard and spherical particles provide excellent mold and core strengths, enabling the production of intricate designs with fine details. The uniform particle size distribution also contributes to improved flowability and compaction during the molding process, ensuring consistent thickness and strength across the mold. This is particularly beneficial in industries such as aerospace and automotive, where precision and reliability are paramount.ceramic foundry sand
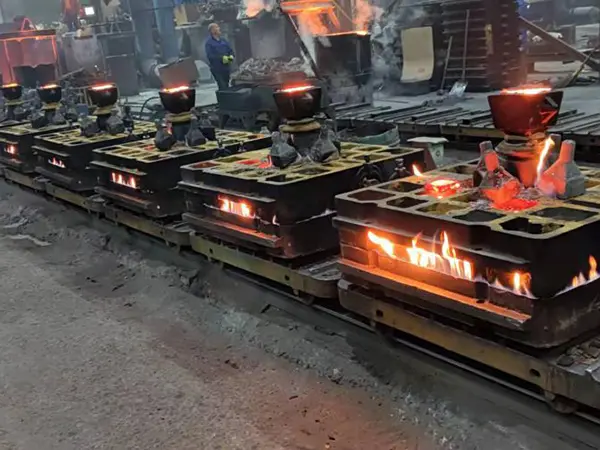
From an environmental perspective, ceramic foundry sand presents a more sustainable option compared to traditional sands. The production and use of silica sand are associated with significant environmental concerns, including habitat disruption and respiratory health hazards from silica dust. In contrast, ceramic foundry sand is often made from recycled materials, such as alumina and zirconia, significantly reducing its ecological footprint. Moreover, as it can be reused multiple times without degradation in quality, it contributes to lower waste generation and aligns with the principles of a circular economy.
Furthermore, the use of ceramic foundry sand can lead to cost savings for manufacturers. Although the initial investment in ceramic materials may be higher than that of traditional sands, the long-term benefits far outweigh these costs. The durability and reusability of ceramic sand lead to lower material consumption, reduced labor costs associated with cleanup and reclamation, and decreased shipping costs due to its lightweight nature. Additionally, fewer defects and reworks translate into enhanced productivity and reduced operational downtime.
Another noteworthy aspect of ceramic foundry sand is its compatibility with various binder systems, allowing foundries to adopt modern binding technologies without sacrificing performance. This versatility enhances process flexibility and enables manufacturers to experiment with different binder formulations to optimize casting properties and improve overall efficiency.
In conclusion, ceramic foundry sand is revolutionizing the casting industry by addressing several pressing challenges. Its superior thermal and mechanical properties, coupled with its environmental benefits and cost efficiency, make it an appealing choice for foundries looking to enhance their operations. As technology advances and industries continue to prioritize quality and sustainability, the adoption of ceramic foundry sand is likely to grow, paving the way for innovations in casting processes and the manufacturing of high-performance components. The future of casting lies in such smart materials, promising not only improved product quality but also a greener, more sustainable manufacturing landscape.
Post time:Jul . 31, 2024 20:01
Next:Essential Stages in the Sand Casting Process for Effective Metal Casting Techniques