Steps in Sand Casting A Comprehensive Guide
Sand casting is one of the oldest and most versatile casting methods used in the metalworking industry. This process is particularly favored for its ability to create complex shapes with high precision and relatively low cost. Understanding the steps involved in sand casting can provide insights into its effectiveness and efficiency in producing metallic parts. This article will outline the major steps in the sand casting process.
1. Pattern Making
The first step in sand casting is the creation of a pattern, which is a replica of the final product to be cast. Patterns can be made from various materials, including wood, metal, or plastic. The choice of material often depends on the quantity of castings needed and the complexity of the design. Patterns are typically oversized to account for metal shrinkage that occurs as it cools. There are different types of patterns, such as single-piece, split, or core patterns, depending on the shape and design of the final product.
2. Preparing the Mold
Once the pattern is complete, the next step is to create a mold. This process involves enclosing the pattern in a mixture of sand and a binder, which gives the sand its shape. The sand is compacted around the pattern to ensure that it captures all the intricate details of the design. After the sand hardens, the pattern is carefully removed, leaving a cavity that mirrors the pattern. This mold may consist of two halves (parting line) which are then rejoined for the pouring of molten metal.
In cases where the casting requires internal cavities or hollow sections, cores are created. Cores are typically made from a thermosetting resin or sand, allowing them to be placed within the mold. The core is positioned in the mold cavity prior to pouring the metal, ensuring that the final piece has the desired internal features. This step is crucial for complex designs that cannot be achieved with the mold alone.
4. Melting the Metal
steps in sand casting
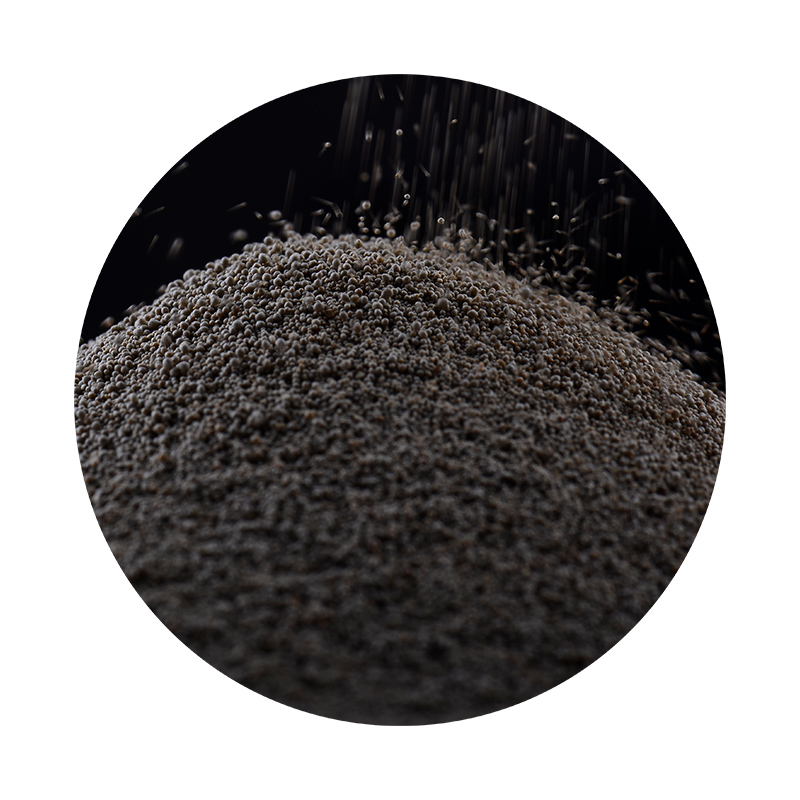
After the mold has been prepared, the next step involves melting the metal to be cast. This is usually done in a furnace, where the selected metal—such as aluminum, iron, or bronze—is heated to its melting point. The type of furnace used can vary based on the metal being melted and the desired production volume. Once the metal is molten and has reached the right temperature, it is ready to be poured into the mold.
5. Pouring the Metal
This step involves carefully pouring the molten metal into the prepared mold. Accuracy and timing are critical to prevent issues such as solidification before the mold is filled or the formation of air pockets within the casting. The pouring can be done manually or through automated systems for high-volume production. After the mold has been filled, the metal is allowed to cool and solidify, which can take a varying amount of time depending on the metal and the size of the casting.
6. Removing the Casting
Once the metal has cooled and solidified, the next step is to remove the casting from the mold. This is done by breaking apart the sand mold, which is usually one of the advantages of sand casting it allows for easy removal of the finished product. Care should be taken to avoid damaging the casting during this process.
7. Finishing Operations
The final step in the sand casting process is finishing. This may involve cleaning the casting to remove any residual sand, trimming off excess material, and performing any necessary machining to achieve the desired dimensions and surface finish. Additional processes such as heat treatment, plating, or painting may also be applied to enhance the mechanical properties and appearance of the casting.
In conclusion, sand casting is a multi-step process that allows for the efficient production of complex metal parts. From pattern making to finishing operations, each step plays a crucial role in ensuring the quality and precision of the final product. Understanding these steps provides valuable insight into one of the most fundamental methods of metal casting widely used in various industries today.
Post time:Jul . 31, 2024 19:26
Next:Incorporating Sand into Resin for Enhanced Texture and Durability in Crafts and Projects