Sand Casting Foundry An Overview
Sand casting is a versatile and widely used metal casting process that involves creating a mold from sand to shape molten metal into desired components. This age-old technique is favored for its simplicity, cost-effectiveness, and the ability to produce complex shapes. The sand casting foundry plays a crucial role in various industries, from automotive to aerospace, contributing to the production of critical components that are both functional and intricate.
The Sand Casting Process
The sand casting process begins with the preparation of the sand mold. A mixture of sand, clay, and water is used to create a mold that can withstand the high temperatures of molten metal. The sand is compacted around a pattern, which is typically made from metal or wood, to form the cavity that will ultimately define the shape of the finished product. Once the pattern is removed, a two-part mold is often created to allow for easy extraction of the casting once it has cooled.
After the mold is prepared, molten metal is poured into the cavity. The heat of the molten metal causes the sand to form a solid shell around it, maintaining the shape until it solidifies. This method is particularly well-suited for metals such as iron, aluminum, and copper alloys. Once the metal has cooled and solidified, the sand mold is broken away, revealing the cast metal product.
Advantages of Sand Casting
One of the primary advantages of sand casting is its flexibility. Sand molds can be easily created for a wide range of part sizes and shapes, making this process ideal for both small-scale production runs and large manufacturing outputs. Furthermore, the sand used in these molds is reusable, which adds to the cost-effectiveness and sustainability of the process.
sand casting foundry
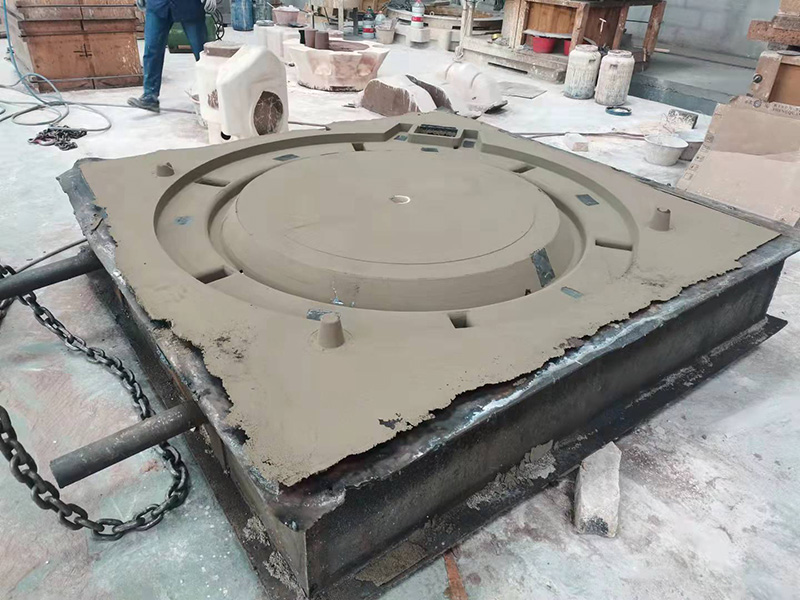
Another significant benefit is the ability to produce intricate designs. With modern technologies, including CAD and 3D printing, patterns can be created with exceptional precision, allowing for highly detailed castings. This capability is particularly beneficial in industries that require high-performance parts with complex geometries, such as aerospace and automotive sectors.
Challenges and Considerations
Despite its many advantages, sand casting foundries also face certain challenges. One notable issue is the quality of the sand. Impurities in the sand can lead to defects in the cast, which may affect the strength and durability of the final product. Therefore, foundries must invest in high-quality materials and maintain strict quality control processes to ensure the best outcomes.
Additionally, the casting process can produce significant waste, both in terms of excess material and emissions. Sustainable practices, such as recycling sand and using environmentally friendly binders, are increasingly being adopted to mitigate these impacts. Advanced technologies, such as computer simulations and automated systems, are also being implemented to improve efficiency and reduce waste in the sand casting process.
Conclusion
The sand casting foundry remains a vital part of the manufacturing landscape. Its ability to produce complex metal components quickly and cost-effectively ensures its continued relevance in modern industry. As technologies evolve and sustainability becomes a priority, the sand casting process is likely to adapt and improve, retaining its status as a go-to method for metal casting. With a rich history and a promising future, sand casting will continue to pave the way for innovation in manufacturing for years to come.
Post time:Aug . 09, 2024 00:45
Next:An Overview of Sand Casting Techniques and Procedures for Efficient Metal Fabrication