The Art and Science of Sand Casting An Overview of Sand Casting Factories
Sand casting, a timeless and versatile manufacturing process, has been a cornerstone in the production of metal components for centuries. This method involves creating a mold from sand, which is then filled with molten metal to form intricate parts. Sand casting factories play a crucial role in various industries, including automotive, aerospace, and machinery, by providing essential components that meet rigorous quality standards.
The Sand Casting Process
The process begins with the creation of a mold. A pattern, typically made of wood or metal, is constructed to the desired shape of the final product. This pattern is then embedded in a mixture of sand, clay, and water to form the mold. The compacted sand holds its shape, allowing for the intricate details of the pattern to be transferred to the final product.
Once the mold is ready, it is assembled into two halves the cope (top) and the drag (bottom). The two halves are precisely aligned and clamped together to prevent any leakage of molten metal. After that, the mold is heated to remove any moisture, reducing the risk of defects in the final casting.
The next step involves pouring the molten metal into the mold through a pouring basin and sprue. The choice of metal depends on the specific requirements of the component being produced; common metals include aluminum, iron, and bronze. The molten metal flows into the cavity of the mold, taking on its shape as it cools and solidifies.
Once the metal has cooled sufficiently, the sand mold is broken apart, revealing the casting within. The final step involves trimming away any excess material, known as flash, and performing necessary finishing processes such as machining or surface treatment to ensure the component meets specifications.
sand casting factory
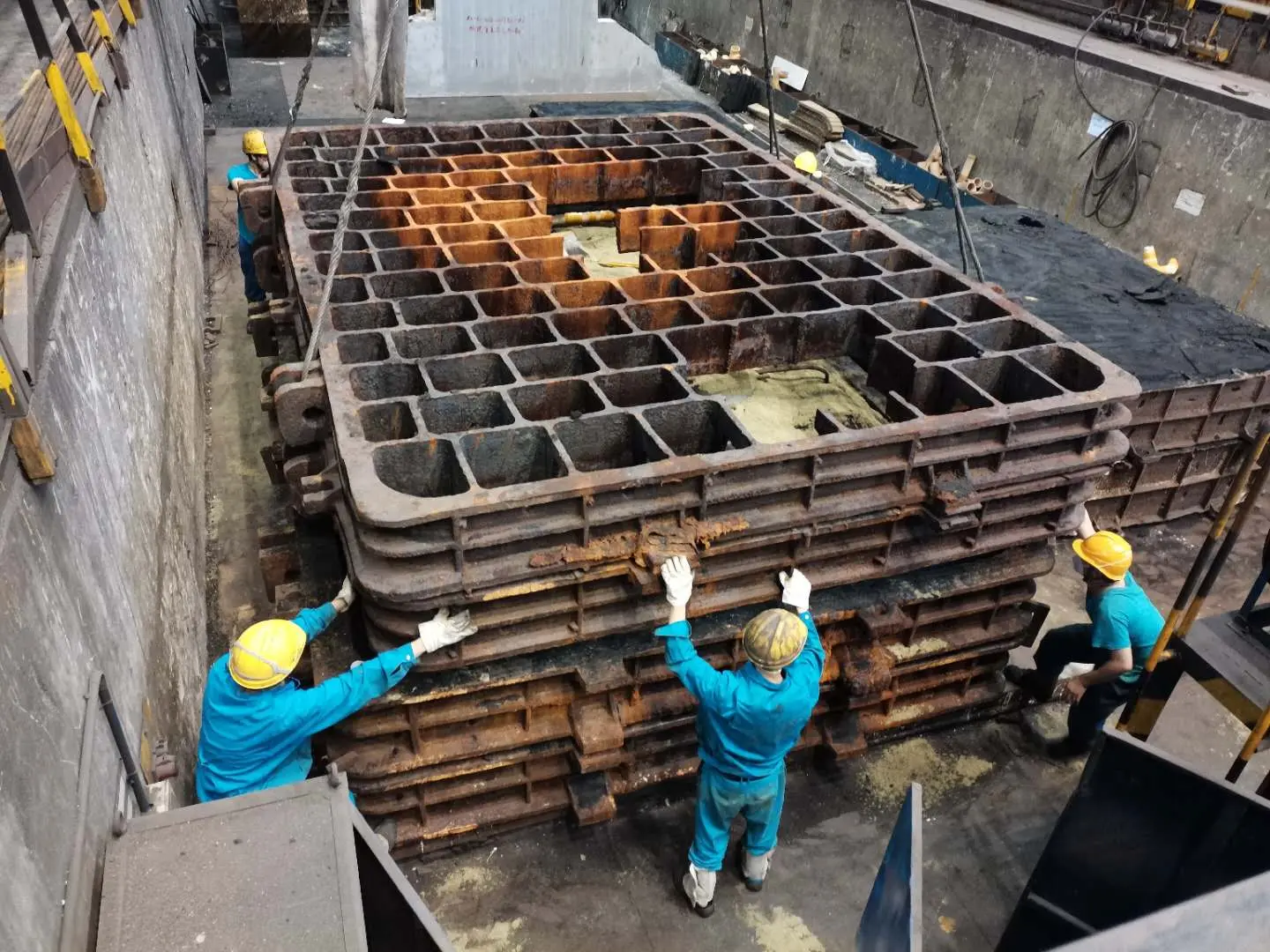
Advantages of Sand Casting
One of the principal advantages of sand casting is its adaptability. The process can produce small to large components with complex geometries, and molds can easily be modified to accommodate design changes. This flexibility is especially advantageous in industries where rapid prototyping and custom components are required.
Moreover, sand casting is cost-effective for both low and high production volumes. The materials used, primarily sand and metal, are relatively inexpensive, and the process does not require extensive tooling, which can significantly reduce startup costs. This makes sand casting an attractive option for startups and established manufacturers alike.
Environmental Considerations
In recent years, there has been increasing emphasis on sustainable practices within sand casting factories. Many facilities are taking significant steps to minimize their environmental footprint by recycling sand and using eco-friendly molding materials. Innovations in technology, such as 3D printing for mold creation, are also being explored to enhance efficiency and reduce waste.
Conclusion
Sand casting remains an essential manufacturing technique in today’s industrial landscape. Sand casting factories work at the intersection of art and science, transforming raw materials into functional components that power various industries. As technology advances, these factories are likely to continue evolving, embracing new methodologies while maintaining the traditional strengths of sand casting. Whether for a simple component or a sophisticated assembly, the contributions of sand casting factories are integral to our modern economy and infrastructure.
Post time:Aug . 03, 2024 01:19
Next:Understanding the Process and Benefits of Sand Casting in Engineering Applications and Industries