Understanding Sand Casting in Engineering
Sand casting is one of the most widely used metal casting processes in engineering and manufacturing. This versatile technique has stood the test of time, dating back thousands of years, and continues to be pivotal in the production of complex metal components across various industries. In this article, we will explore what sand casting is, how it works, and its benefits and applications in modern engineering.
What is Sand Casting?
Sand casting is a metal casting process characterized by the use of sand as the primary mold material. The process involves creating a mold from a mixture of sand, clay, and water, which can then be used to shape molten metal into various forms. The versatility of sand allows for intricate designs and shapes, making it ideal for producing a wide array of components, from small parts to large industrial pieces.
The Sand Casting Process
The sand casting process can be broken down into several key steps
1. Pattern Creation The first step in sand casting is to create a pattern of the desired object. This pattern is usually made from metal, plastic, or wood and is an exact replica of the final product. The pattern is designed to include allowances for shrinkage and machining.
2. Mold Preparation The pattern is placed in a sand mixture (often called molding sand), which is typically composed of silica sand, a binder (like clay), and water. The sand is packed tightly around the pattern, forming a mold cavity when the pattern is removed.
3. Core Making (if necessary) For more complex shapes, cores made of sand may be required to create internal cavities within the casting. These cores are also made with sand and placed in the mold before pouring the molten metal.
4. Pouring the Metal Once the mold is prepared, molten metal is poured into the mold cavity through a sprue or pouring basin. The temperature of the molten metal must be carefully controlled to ensure proper flow and reduce defects.
what is sand casting in engineering
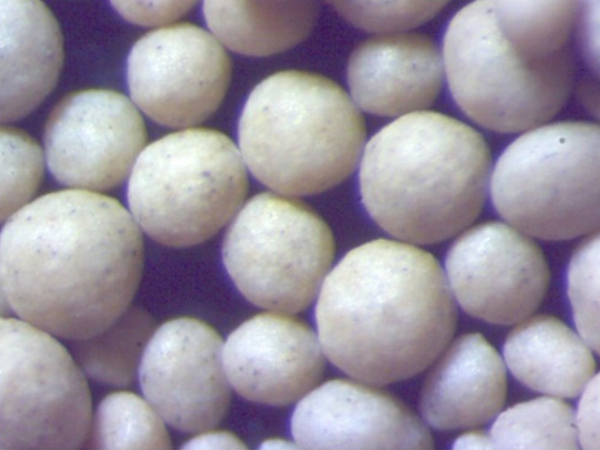
5. Cooling and Solidification After the metal is poured, it is left to cool and solidify. Cooling time can vary based on the size of the casting and the type of metal used.
6. Mold Removal and Finishing Once the metal has solidified, the sand mold is broken away to reveal the raw casting. The casting often requires finishing processes, such as machining, grinding, or polishing, to achieve the final desired shape and surface finish.
Advantages of Sand Casting
One of the major advantages of sand casting is its adaptability. The process can accommodate a wide range of metal types, including ferrous and non-ferrous metals. Additionally, sand casting can produce large components with excellent dimensional accuracy, making it suitable for a variety of applications, from automotive parts to aerospace components.
Another significant benefit is cost-effectiveness. Unlike more advanced casting methods, sand casting requires relatively low investment for tooling and equipment, making it an economically viable option for both small and large production runs. Sand casts can also be produced quickly, which is advantageous for prototype development.
Applications in Engineering
Sand casting finds extensive applications in various sectors of engineering. In the automotive industry, it is used for manufacturing engine blocks, cylinder heads, and other critical components. The aerospace sector utilizes sand casting for producing lightweight, complex designs required in aircraft. Additionally, the construction and industrial equipment industries also rely on sand casting for machinery parts and structural components.
Conclusion
In conclusion, sand casting remains a fundamental process in the field of engineering and manufacturing. Its versatility, cost-effectiveness, and ability to produce complex shapes make it a go-to method for a variety of applications. As technology advances, sand casting continues to evolve, integrating modern techniques while preserving its traditional roots. Understanding sand casting is essential for those in the engineering field, as it serves as a foundation for creating some of the most critical components used in today’s industries.
Post time:Aug . 02, 2024 14:52
Next:Effective Techniques for Sanding Cast Iron Surfaces to Achieve a Smooth Finish