Furan Resin Sand Casting
Furan resin sand casting is a widely used technique in the manufacturing industry that combines the versatility of sand casting with the advantages of furan resin as a binder. This method has gained popularity due to its efficiency and the quality of the cast products it can produce.
Furan resin, a phenolic resin derived from furan, is known for its excellent thermal stability, chemical resistance, and high strength. These properties make it an ideal choice for binding sand in the casting process. Furan resin sand casting is particularly beneficial for creating complex shapes and fine details, which are often difficult to achieve with traditional methods.
The casting process typically begins with the preparation of the sand mixture. In this phase, silica sand is combined with furan resin and a hardener. The furan resin reacts with the hardener, creating a durable and rigid mold when heated. This mixture results in a mold that possesses improved mechanical properties compared to conventional sand molds. By allowing for greater accuracy and surface finish, furan resin sand casting is increasingly preferred for intricate parts, especially in industries such as automotive, aerospace, and heavy machinery.
One of the key advantages of furan resin sand casting is its ability to produce molds that can withstand high temperatures. This characteristic is essential when pouring molten metal, as it can reach temperatures exceeding 1000°C (1832°F). The thermal stability of furan resin ensures that the molds maintain their integrity during the casting process, leading to fewer defects and a higher yield of finished products.
furan resin sand casting
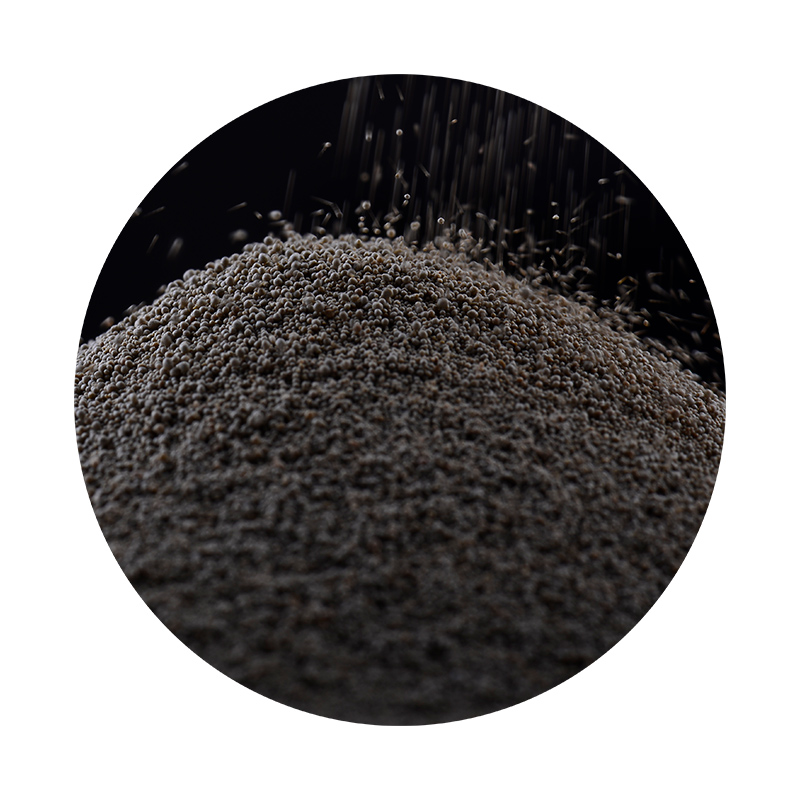
Additionally, the rapid curing time of furan resin enhances productivity. Once mixed, the sand can be shaped into molds relatively quickly, allowing manufacturers to reduce lead times and optimize their production schedules. This speed becomes crucial in environments where time-to-market is critical, as companies are compelled to meet increasing consumer demands without compromising quality.
Another significant benefit is the reduced environmental impact. Compared to traditional phenolic resins, furan resin generates fewer volatile organic compounds (VOCs) during the curing process. This characteristic aligns with modern manufacturing practices, which emphasize sustainability and adherence to environmental regulations. Furthermore, the use of furan resin allows for a more efficient recycling of sand, combining ecological benefits with economic advantages.
Despite these advantages, there are challenges associated with furan resin sand casting. The initial setup costs may be higher due to the need for specialized equipment and materials. Moreover, proper handling and storage of furan resin require safety precautions due to its chemical nature. Adequate ventilation, personal protective equipment, and training for workers are essential to mitigate any health risks associated with exposure.
In conclusion, furan resin sand casting has established itself as a valuable process in modern manufacturing. Its ability to produce high-quality, intricate metal components efficiently and sustainably makes it an attractive option for various industries. As technology continues to advance, it is anticipated that further innovations will enhance the capabilities and applications of furan resin in the casting sector, thus solidifying its role in the future of manufacturing. Whether for small-scale production or large industrial applications, furan resin sand casting offers a promising solution that balances performance with environmental responsibility.
Post time:Aug . 09, 2024 01:40
Next:Innovative Techniques and Applications in Three-Dimensional Sand Printing Technology for Modern Manufacturing