Understanding Ceramsite Foundry Sand A Material Revolution in Casting
In the realm of manufacturing, the importance of high-quality materials cannot be overstated, especially in the foundry industry where precision in casting is critical. One such innovative material gaining traction is ceramsite foundry sand. This advanced material is transforming the way foundries approach metal casting, providing numerous advantages over traditional options.
Ceramsite foundry sand is produced from processed clay, which is then fired at high temperatures to create spherical, lightweight particles. This unique production process endows ceramsite sand with distinct characteristics that make it a superior choice for many foundry applications. One of the most significant benefits of ceramsite sand is its exceptional thermal stability. Unlike traditional sand, ceramsite retains its shape and integrity under high temperatures, making it ideal for casting metals that require precise heat management.
Moreover, ceramsite foundry sand has a lower thermal expansion coefficient compared to silica sand
. This property is crucial in preventing dimensional changes during the cooling process of castings, which helps mitigate defects such as warping and cracking. The predictability of ceramsite sand leads to improved casting accuracy and a higher quality finished product, which is imperative for sectors that require stringent tolerances and reliability, such as aerospace and automotive industries.ceramsite foundry sand
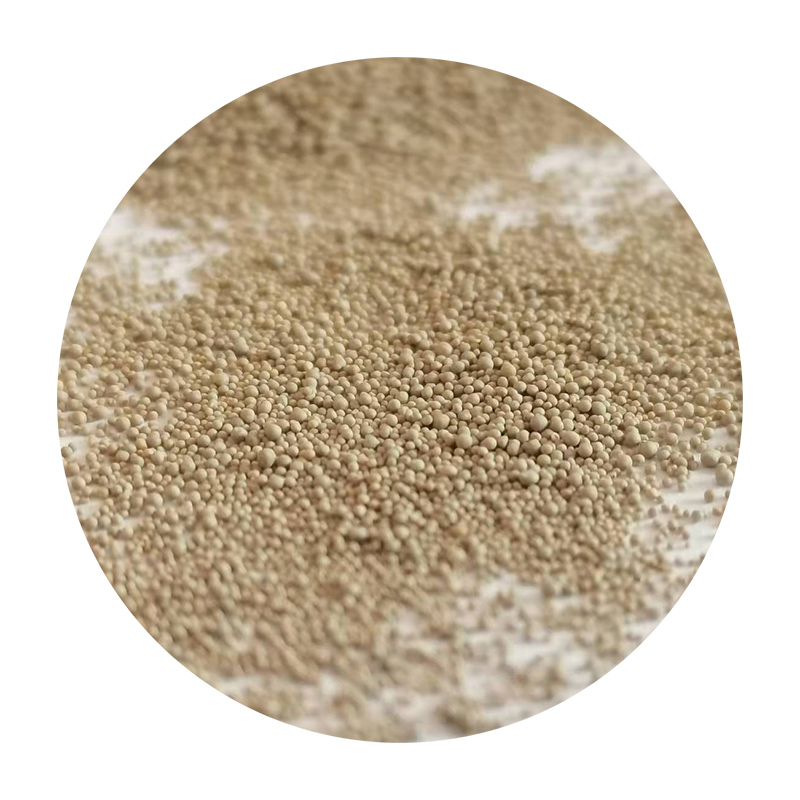
Another key advantage of ceramsite sand is its excellent flowability and ability to form intricate molds. The spherical shape of ceramsite particles allows for better packing density, which leads to improved mold strength and reduced porosity in castings. Foundries that utilize ceramsite sand can achieve thinner mold walls and tighter tolerances, resulting in a more efficient use of materials and a decrease in waste. This attribute is particularly significant as industries around the world strive to enhance their sustainability practices and reduce environmental impacts.
In terms of environmental benefits, ceramsite foundry sand is often produced from natural clay, which can make it a more eco-friendly option compared to synthetic sands. Moreover, ceramsite can be recycled multiple times, further minimizing waste. This attribute aligns perfectly with the growing demand for sustainable practices across all sectors, including foundry operations. The reduced need for fresh sand and the ability to reuse materials contribute to a more circular economy within the foundry industry.
While the advantages of ceramsite foundry sand are clear, it is also important to consider economic factors. The initial investment in ceramsite sand may be higher than that of traditional sand alternatives. However, the long-term savings generated from reduced defects, lower material consumption, and improved efficiencies often outweigh the upfront costs. Foundries embracing this innovative material may find themselves with a competitive edge as they produce higher quality castings at a lower operational cost.
In conclusion, ceramsite foundry sand represents a significant advancement in casting technology. Its unique properties – including thermal stability, low expansion rates, excellent flowability, and environmental sustainability – make it an ideal choice for modern foundries aiming to enhance their production processes. As industries continue to evolve and place greater emphasis on quality and sustainability, the adoption of ceramsite foundry sand is likely to increase, contributing to the future of casting and manufacturing. Embracing this material is not merely a trend; it is a strategic move towards more advanced, efficient, and environmentally conscious foundry operations.
Post time:Aug . 09, 2024 01:55
Next:Innovative Applications of Furan Resin in the Sand Casting Process for Enhanced Performance and Sustainability